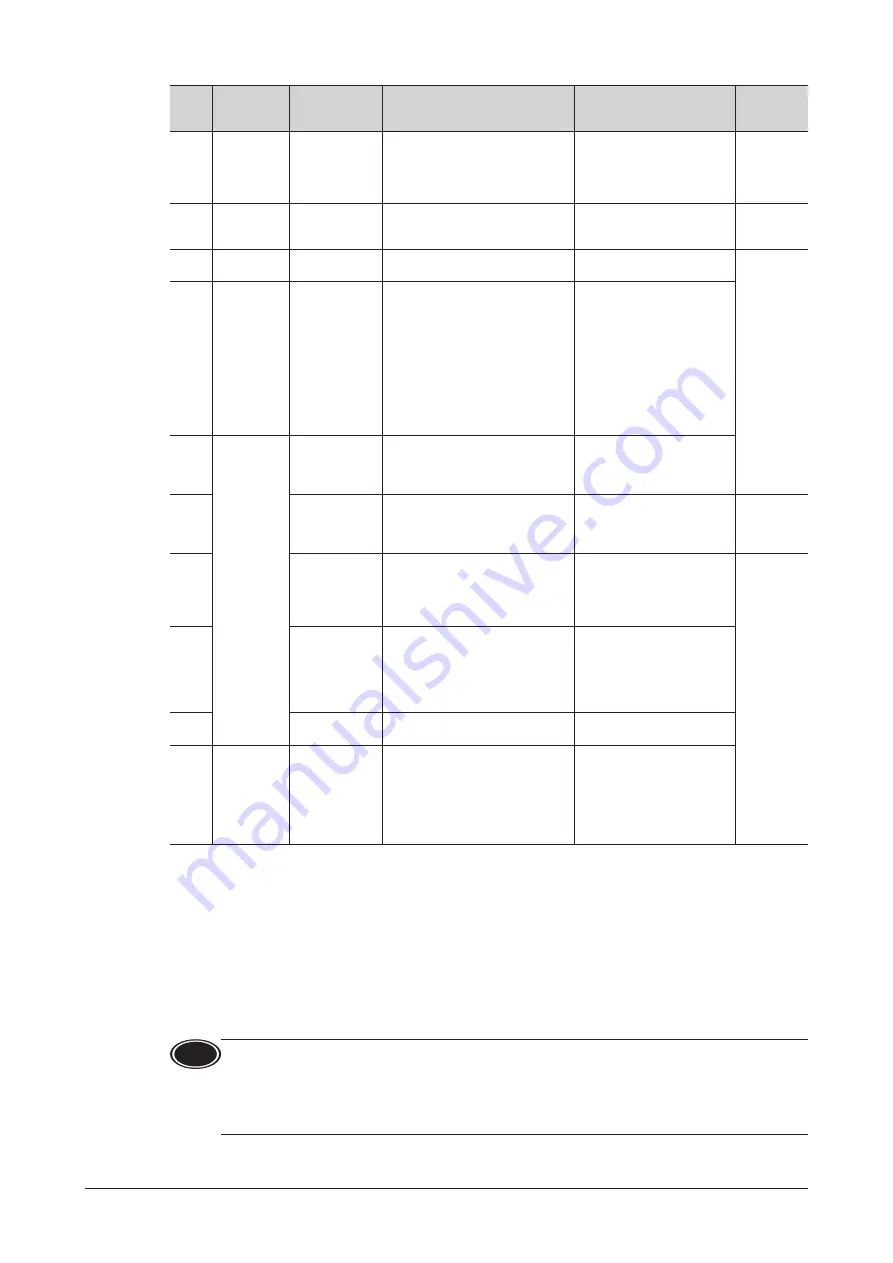
Alarms, warnings and communication errors
−36−
Alarm
code
Number of
times ALARM
LED blinks
Alarm type
Cause
Remedial action
Reset using
the ALARM-
RESET input
41h
8
EEPROM error
•
Stored data was damaged.
•
Data became no longer writable
or readable.
Initialize the parameters
using the
MEXE02
,
OPX-2A
,
or RS-485 communication,
and then turn on the power
supply again.
Not
possible
21h
9
Main circuit
overheat
The temperature inside the driver
exceeded the main circuit overheat
level.
Reconsider the ventilation
condition in the enclosure.
Possible
6Eh
10
External stop
*1
The EXT-ERROR input was turned
OFF.
Check the EXT-ERROR input.
Possible
46h
11
Prevention of
operation at
power-on
*2
The main power supply was
turned on when the FWD input or
REV input was being ON.
※
When the “3-wire input mode”
was set with the “Operation
input mode selection"
parameter, the main power
supply was turned on in a
state where the START/STOP
input and RUN/BRAKE input
were being ON.
Turn the FWD input and REV
input OFF, and turn on the
main power supply again.
※
When the “3-wire input
mode” was set with the
“Operation input mode
selection" parameter, turn
either the START/STOP
input or RUN/BRAKE input
OFF before turning on the
main power supply again.
81h
12
Network bus
error
The bus of host network of the
network converter was in a
disconnection state while the
motor was operated.
Check the connector and
cable of the host network.
83h
Communication
switch setting
error
No.4 of the communication
function switch (SW2) was turned
ON.
Turn No.4 of the
communication function
switch (SW2) OFF, and turn
on the power again.
Not
possible
84h
RS-485
communication
error
The number of consecutive RS-485
communication errors reached the
set value in the "Communication
error alarm" parameter.
•
Check the connection
between the driver and
programmable controller.
•
Check the setting of RS-485
communication.
Possible
85h
RS-485
communication
timeout
The time set in the
“Communication timeout”
parameter has elapsed, and
yet the communication could
not be established with the
programmable controller.
Check the connection
between the driver and
programmable controller.
8Eh
Network
converter error
An alarm was generated in the
network converter.
Check the alarm code of the
network converter.
2Dh
14
Main circuit
output error
*3
•
The motor power line was
disconnected or the motor
power connector came off.
•
When the operation input signal
was switched instantaneously,
the motor could not follow and
continued a state of not rotating.
•
Check the connection
between the driver and
motor.
•
Check the motor has
rotated before switching
the operation command.
*1
This alarm is generated when the EXT-ERROR is assigned to the X0 to X5 inputs.
*2
This alarm is generated when the “Prevention of operation at power-on alarm function” parameter is set to “Enable.”
*3
This alarm is not generated when the torque limiting value is set to less than 200%.
Alarm reset
Before resetting an alarm by performing one of the reset operations specified below, be sure to remove the cause
of the alarm and turn the FWD and REV input signals OFF to ensure safety. Refer to the USER MANUAL (Basic
Function) for the timing chart.
•
Turn the ALARM-RESET input ON (keep it ON for 10 ms or more) and then OFF.
•
Execute the reset alarm by the maintenance command.
•
Execute an alarm reset using the
MEXE02
or
OPX-2A
.
•
Cycle the main power. Also, cycle the control power supply when connecting it.
Note
•
Some alarms cannot be reset with the ALARM-RESET input,
MEXE02
,
OPX-2A
or maintenance
command. Check with the alarm list. To reset these alarms, cycle the driver power.
•
In the case of resetting an alarm via RS-485 communication, if the reset alarm is executed in a state
where the FWD input or REV input is being ON, it is dangerous because the motor will start rotating
after the alarm is reset. Be sure to turn both the FWD input and REV input OFF before resetting the
alarm.