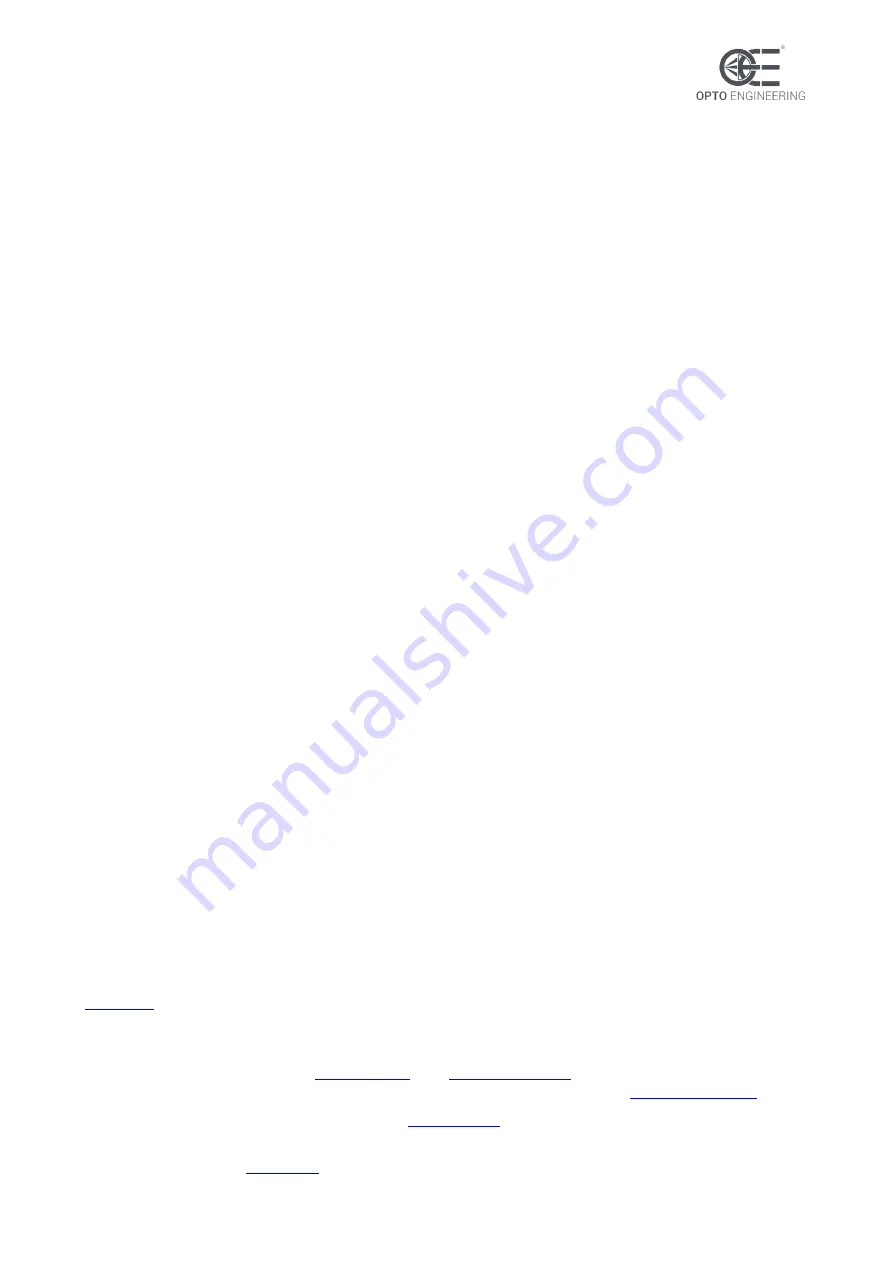
5
LTDVE4CH-20 | INSTRUCTIONS MANUAL
4. General description
Any machine vision application employs some kind of light controller. Light controllers are widely
used to both optimize illumination intensity and obtain repeatable trigger sequencing between lights
and vision cameras.
This controller is a compact unit that includes power supply conditioning, intensity control, timing
generation and advanced triggering functions.
The controller can be set up using a PC with serial RS485 or Ethernet interfaces. Configurations are
saved in non-volatile memory so that the controller will resume operation after a power cycle.
4.1. Benefits of current control
Most LED manufacturers suggest their products to be driven using a constant current source, not a
constant voltage source. This is because, using a constant voltage driving, small variations in
temperature or voltage at the LEDs can cause a noticeable change in their brightness.
Brightness control with voltage is also very difficult because of the non-linearity of brightness with
voltage. On the contrary, the brightness is approximately linear with current, so by driving the LEDs
with a known current, intensity control is linear.
This strobe controller has four independent, programmable, current-controlled pulsed or continuous
outputs with currents ranging from zero up to 20 A. In continuous mode the output current is internally
limited by the firmware to 2 A.
4.2. Operating mode
This controller operates both in pulsed and in continuous mode.
In pulsed mode the light is switched on only when necessary. A digital input is used as a trigger.
When a rising edge on the trigger signal is detected the output is pulsed for the programmed amount
of time.
Using this technique, it is possible to obtain excellent steady images of moving objects. The camera
can be set for an arbitrary long exposure time and the light turned on for a shorter time, just enough
to freeze the motion. This helps to overcome the problems usually related with integration start
uncertainty which, to some degree, afflict most commercial cameras.
The delay from the trigger to the output pulse, the width of the output pulse and the intensity of the
output pulse are all independently configurable. The pulse delay can range from 0 µs to 1 s. The
pulse width can range from 1 µs to 1 s. There are three ranges for the current pulse:
Low current, up to 200 mA (with resolution of 1 mA)
Mid current, up to 4 A (with resolution of 4 mA)
High current, up to 20 A (with resolution of 20 mA)
In continuous mode the light is always switched on, independently from the trigger signal. Using this
technique, the maximum current value for each channel has to be limited in order to prevent the
overheating of the controller. For more information about current and power limitations refer to
5. Getting started
Carefully read the sections on
Safety Notes
and check the product fits your
needs. Mount the controller using a DIN rail as described in the section on
Connect the controller as in the section on
. When the controller powers up it should
show the PWR LED lit with a stable green colour and the RUN LED lit with a pulsing green colour.
. The controller can be configured by using both a serial RS485