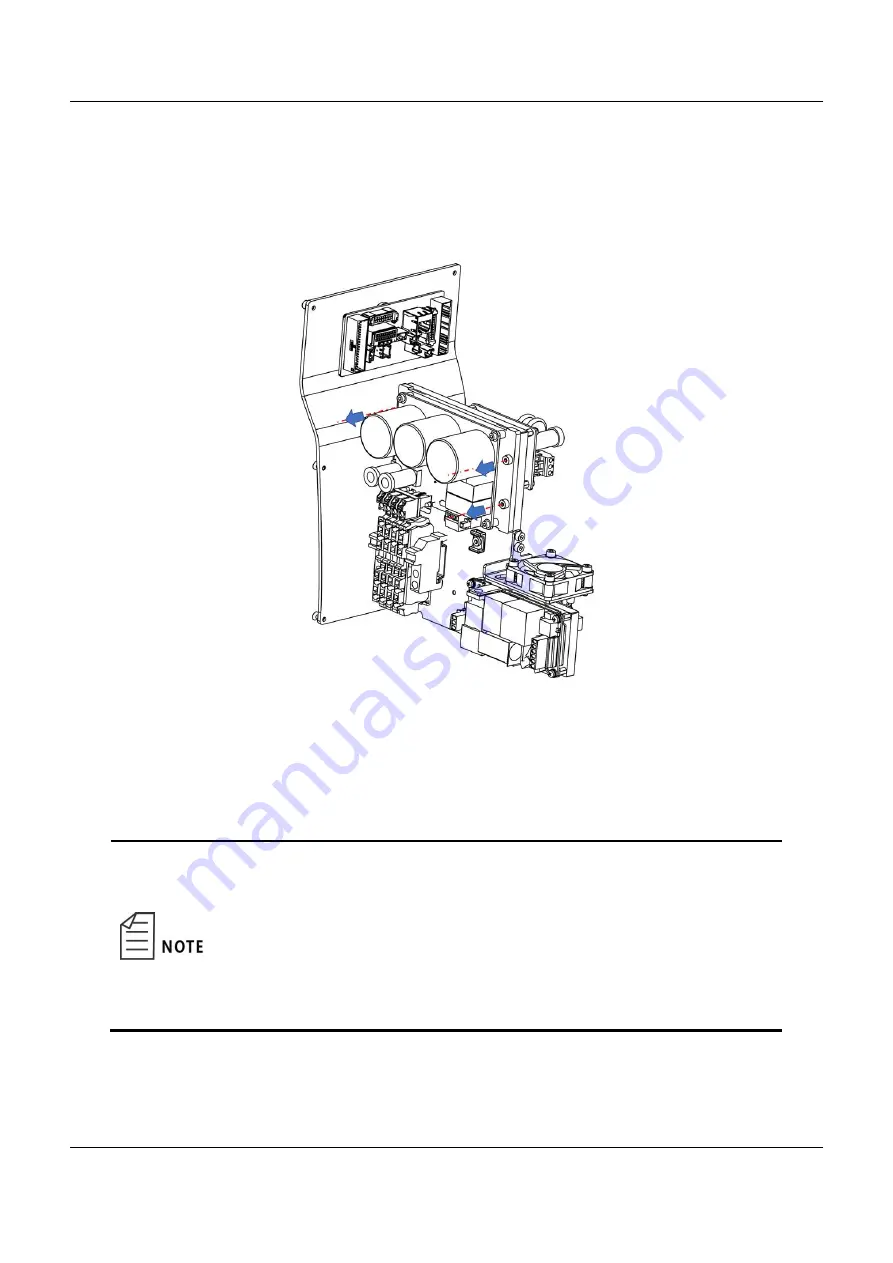
AH6 Robot Maintenance Manual
Document Version V1.1.2 (19/09/2022)
57
Step 2
Unplug all cables connected to the QBUS module.
Step 3
Use 3 mm Allen wrench to loosen screws on the QBUS module and remove
them, as shown in Figure 5-14.
Figure 5-14 Removal of fastening screws from QBUS module
Step 4
Install a new QBUS module on the part in the base and tighten the screws,
and then connect all cables to the new QBUS module.
At the time of installation, users shall check whether the interfaces
match the line labels to avoid damage to the controller due to
wrong connection. Line labels corresponding to each interface are
shown in the figure below:
Содержание AH6
Страница 1: ...AH6 Robot Maintenance Manual Document Version V1 1 2 19 09 2022 I...
Страница 16: ......
Страница 83: ...AH6 Robot Maintenance Manual Document Version V1 1 2 19 09 2022 67...