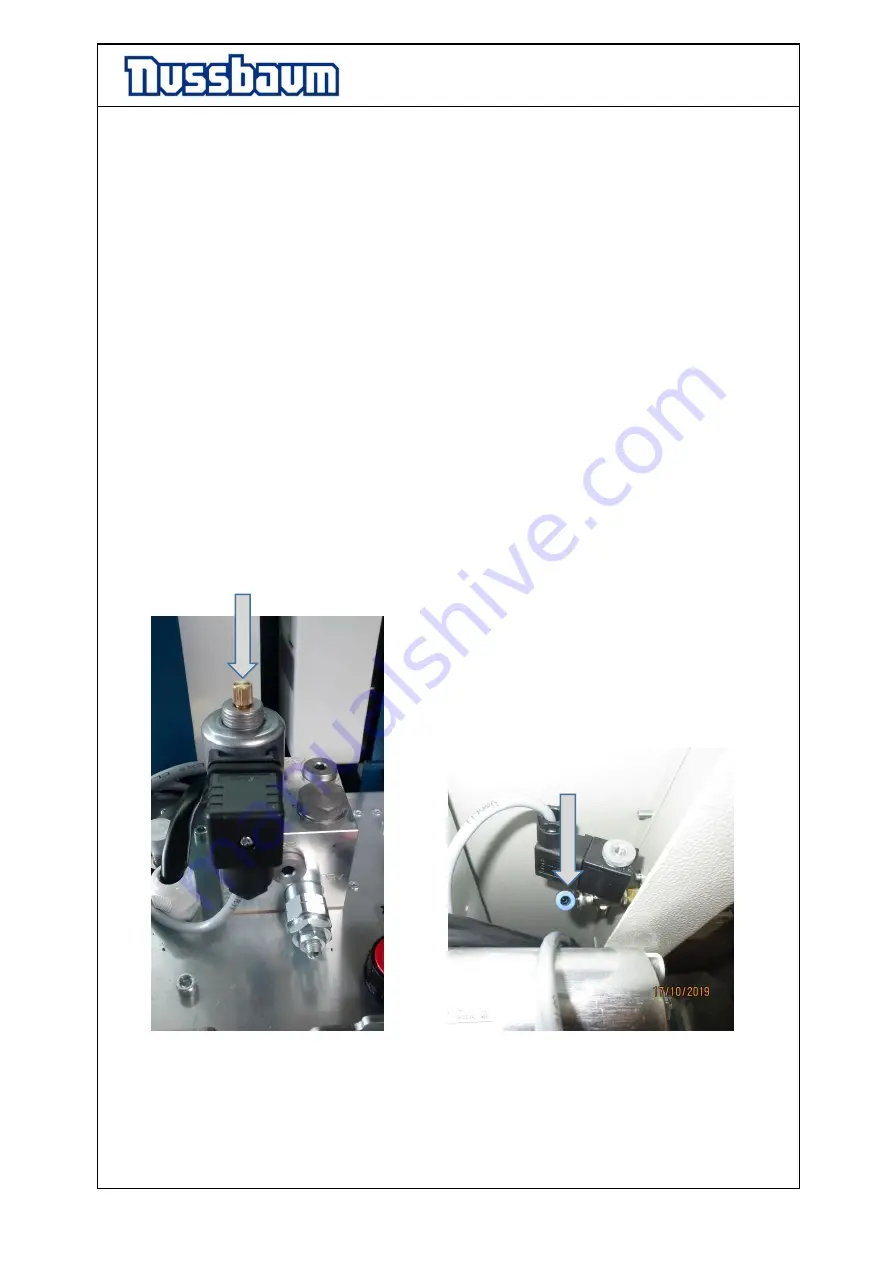
Operating Manual and Inspection Book
TOP LIFT TSK 12000 DJ
- 31 -
6.2.1 Defect of the hydraulic valve
If there is a defect in the hydraulic valve there is still the option of moving the lift
to its lowest position so the vehicle can be drive off the lift.
1.
Push the "Lower" button and the latches must unlock.
2.
If the safety latches are locked, they must be lifted with a suitable tool (hyd.
lifter) if needed until the safety latch opens due to the attached com-
pressed air.
3.
Open the top cover of the external unit.
4.
Unscrew the cap on the hydraulic valve (see Fig. 2a).
5.
Push the "Lower" button and simultaneously open the hydraulic valve to start
the lowering procedure.
Lowering
6.
The entire lowering process must be continuously observed.
7.
Once the lift is at the lowest position, the vehicle can be driven off the lift.
8.
Close the hydraulic valve again and turn on the cap.
9.
The lift must be stopped until defective parts have been exchanges and the
lift is in a technical perfect condition again.
10.
If required, do maintenance.
Fig. 2a: Hydraulic emergency lowering,
remove cap and open valve
Fig. 2b: Pneumatic air supply for actuating
the ratchet cylinders.
Содержание TOP LIFT TSK 12000 DJ
Страница 2: ......
Страница 9: ...Operating Manual and Inspection Book TOP LIFT TSK 12000 DJ 9 ...
Страница 15: ...Operating Manual and Inspection Book TOP LIFT TSK 12000 DJ 15 3 2 Data sheet ...
Страница 16: ...Operating Manual and Inspection Book TOP LIFT TSK 12000 DJ 16 ...
Страница 17: ...Operating Manual and Inspection Book TOP LIFT TSK 12000 DJ 17 ...
Страница 18: ...Operating Manual and Inspection Book TOP LIFT TSK 12000 DJ 18 3 3 Hydraulic plan ...
Страница 20: ...Operating Manual and Inspection Book TOP LIFT TSK 12000 DJ 20 3 4 Pneumatic plan ...
Страница 22: ...Operating Manual and Inspection Book TOP LIFT TSK 12000 DJ 22 ...
Страница 23: ...Operating Manual and Inspection Book TOP LIFT TSK 12000 DJ 23 ...
Страница 24: ...Operating Manual and Inspection Book TOP LIFT TSK 12000 DJ 24 ...
Страница 25: ...Operating Manual and Inspection Book TOP LIFT TSK 12000 DJ 25 ...
Страница 34: ...Operating Manual and Inspection Book TOP LIFT TSK 12000 DJ 34 7 1 Lift maintenance plan ...
Страница 35: ...Operating Manual and Inspection Book TOP LIFT TSK 12000 DJ 35 ...
Страница 36: ...Operating Manual and Inspection Book TOP LIFT TSK 12000 DJ 36 ...
Страница 37: ...Operating Manual and Inspection Book TOP LIFT TSK 12000 DJ 37 ...
Страница 51: ...Operating Manual and Inspection Book TOP LIFT TSK 12000 DJ 51 10 Spare part list ...
Страница 52: ...Operating Manual and Inspection Book TOP LIFT TSK 12000 DJ 52 ...
Страница 53: ...Operating Manual and Inspection Book TOP LIFT TSK 12000 DJ 53 ...
Страница 54: ...Operating Manual and Inspection Book TOP LIFT TSK 12000 DJ 54 ...
Страница 55: ...Operating Manual and Inspection Book TOP LIFT TSK 12000 DJ 55 ...