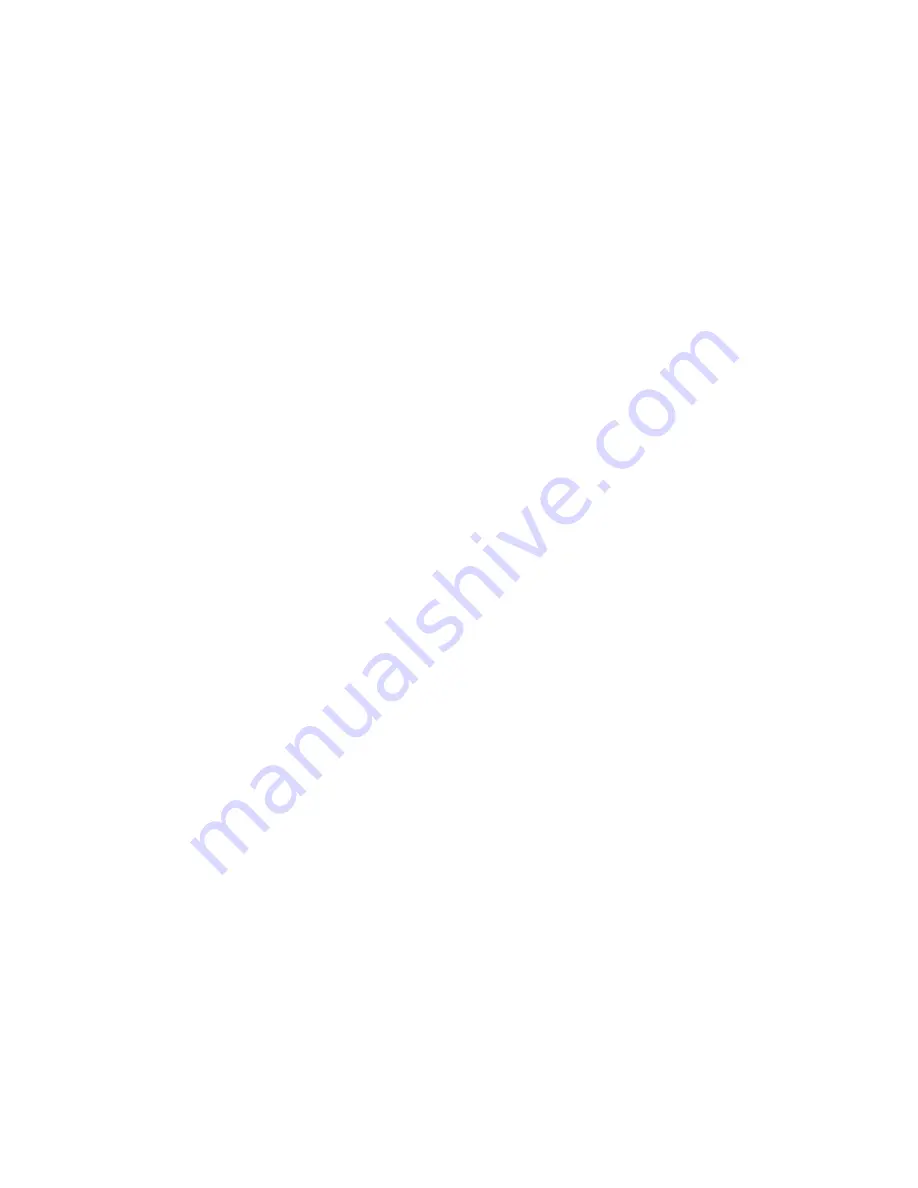
OM0239
Page 31 of 72
April 2021
6.3.6
Terminal Purging and Wipe Down
Following completion of work, allow the cabinet to run for 2-3 minute period without personnel activity to purge
the cabinet. A surface disinfection of the interior surfaces (see Cleaning Procedures section) should be repeated
after removal of all materials, cultures, apparatus, etc. A careful check of grills and diffuser grids should be made
for spilled or splashed nutrients which may support fungus growth and resulting spore liberation that
contaminates the protected work environment.
6.3.7
Paper Catch/Prefilter
A permanent paper catch is installed behind the rear divider panel of the work zone. This area forms the return air
path to the motor/blower; and if the airflow is blocked, it could seriously affect the performance of the cabinet.
Therefore, THE PAPER CATCH SHOULD BE CHECKED AND CLEANED ON A MINIMUM OF A WEEKLY BASIS. A daily
basis if procedures dictate the use of paper products. Any paper removed must be properly disposed of as
Contaminated Hazardous Waste.
The above procedures also apply to all cabinets configured with a prefilter.
6.3.8
Shut Down
Turn off blowers and lights. Do not use cabinet as a depository for excess lab equipment during periods of non-
operation. If antineoplastic agents are being prepared in the cabinet, it is recommended to let the cabinet run 24
hours per day. This lessens the possibility that contaminants may escape.
6.4 Ergonomics
Ergonomics, the study or accommodation of work practices is extremely important for proper cabinet usage and user
health and safety. An evaluation of normal work practices should be performed with each user when working in a cabinet.
Evaluation criteria should be at a minimum:
a. Proper user posture
b. Effective work zone layout for work practice
c. Vision or sightlines
For each of the above evaluation criterion, several work aids may be supplied to accommodate the user.
•
Ergonomic chair - A six-way articulating seat and back control for personalized adjustment to assure proper user
posture. Be sure feet are resting on the floor, chair foot support or foot rest. Also be sure back is fully supported
with proper chair adjustments.
•
Forearm/elbow support - The cabinet is provided with a non-metallic forearm support on the work access opening.
Periodic mini-breaks during work practice should be taken resting forearm to avoid stress and fatigue. Elbow rests
that can provide support for particular work practices, such as pipetting are optional. Also available as an option,
closed cell foam disposable forearm pads to reduce pressure points and add comfort.
•
Effective workzone layout - Always prepare your work procedure to minimize reach to avoid neck and shoulder
stress and fatigue. Rotating tables used to maximum workzone and minimize reach are optional.
•
Vision and sightline - Always prepare your work procedure to eliminate glare and bright reflections on the window.
Keep your window clean and sightlines clear to your effective workzone.
6.5 Cleaning Procedures
6.5.1
General
Cleaning laboratory equipment is important in terms of both functionality and general good housekeeping. The
information provided below is intended to a
id the development of facility Standard Operating Procedures (SOP’s)
for cleaning the equipment. It is strongly recommended that all cleaning materials used be tested and verified in
terms of both effectiveness and material compatibility before they are written into the cleaning SOP
documentation.
a. The airflow blower should be operating during the cleaning process to maintain sterility and/or containment
during the cleaning process.
b. Raise window to gain additional access if desired.
c. Apply appropriate cleaning material or surface disinfectant to surfaces. Most surface disinfectants require a
specific contact time depending the materials used within the work zone.
CONSULT APPROPRIATE DISINFECTANT
DOCUMENTATION FOR PROPER APPLICATION AND SAFETY PRECAUTIONS
.
c-1. Stainless steel (type 304) has noted material compatibility concerns with Acids, Chlorides and Halogens.
IF
THESE MATERIALS ARE USED AND ALLOWED TO BE LEFT ON THE STAINLESS STEEL SURFACE, OXIDATION AND
DEGRADATION WILL OCCUR
. Only by re-wiping surfaces with either sterile water or 70% IPA will remove harmful
materials from the stainless steel surface.
Содержание LabGard ES NU-543-300S
Страница 7: ...OM0239 Page 7 of 72 April 2021 ...
Страница 9: ...OM0239 Page 9 of 72 April 2021 ...
Страница 10: ...OM0239 Page 10 of 72 April 2021 ...
Страница 11: ...OM0239 Page 11 of 72 April 2021 ...
Страница 12: ...OM0239 Page 12 of 72 April 2021 ...
Страница 16: ...OM0239 Page 16 of 72 April 2021 ...
Страница 21: ...OM0239 Page 21 of 72 April 2021 ...
Страница 35: ...OM0239 Page 35 of 72 April 2021 ...
Страница 67: ...OM0239 Page 67 of 72 April 2021 ...
Страница 68: ...OM0239 Page 68 of 72 April 2021 ...
Страница 69: ...OM0239 Page 69 of 72 April 2021 ...
Страница 70: ...OM0239 Page 70 of 72 April 2021 ...
Страница 71: ...OM0239 Page 71 of 72 April 2021 ...
Страница 72: ...OM0239 Page 72 of 72 April 2021 ...