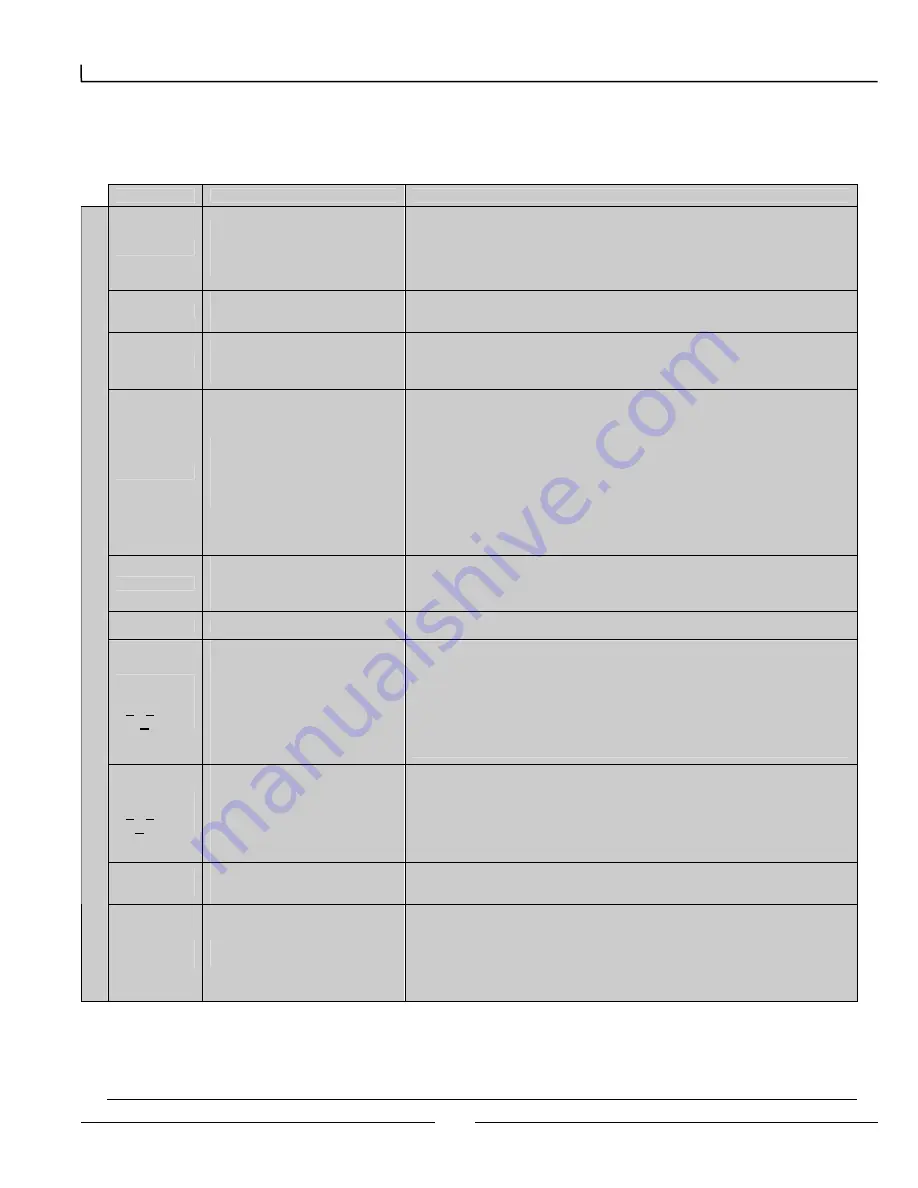
46
Matrix Installation and Operation Instructions
13.0 TROUBLE SHOOTING
This section is intended to assist the service technician in detecting and correcting common errors. The Matrix Boiler and Fan
Controls are equipped with an internal diagnostic system that verifies control operation. The following series of error codes has
been developed to aid in diagnosing control problems:
Symptom
Detected Problem
Solution
ER1
“Water Temperature Excessive”
Sentry has sensed a water
temperature in excess of 250ºF at
the Water Sensor.
1.
If the boiler is extremely hot check for adequate water pressure and
circulation, contact NTI for assistance.
2.
If not hot, check for sources of grounding or shorting at the Water Sensor
electrical connections, check wiring from Sensor to Boiler (Red) Control.
3.
Replace Water Sensor if the resistance is not in the correct range. (See
thermister resistance charts in Figures 13.1 and 13.2)
ER2
“Water Sensor Short Circuit”
Control has sensed a short circuit
in the Water Sensor circuit.
See ER1
ER3
“Water Sensor Open Circuit”
Control has sensed an open circuit
in the Water Sensor circuit.
1.
Check wiring to Water Sensor for open circuits or shorting to ground. (Note:
ER3 will be displayed if temperature sensed is less then 0
°
F.)
2.
Replace Water Sensor if the resistance is not in the correct range. (See
thermister resistance charts in Figures 13.1 and 13.2)
ER4
“24V Limit Error”
Control has sensed a lack of 24V
on the outlet of the burner relay
(B1). Lockout lasts for one hour
before automatically resetting.
1.
Reset power, if error goes away the problem is intermittent and was likely
caused by a tripped limit that has automatically reset, check for adequate
water pressure and flow rate. Allow the boiler to cycle and verify proper
operation including outlet water temperature and flue temperature. If
operation is unsuccessful and the error reoccurs:
2.
Matrix boilers are equipped with a low water pressure switch on the boiler
return that requires a minimum of 10PSI to complete the 24VAC ignition
circuit. Ensure the field-installed pressure gauge is reading a minimum of
12PSI. Replace water pressure switch if plumbing and pressure is correct
and if it measures an open circuit.
3.
Check for continuity through the 24VAC limit wiring and manifold and stack
limits, replace limits or wiring that are not a closed circuit.
ER6
“Flame Lock Out”
Control has sensed a lack of 24V
to the gas valve during operation
or a Fenwal ignition lockout.
There is a problem in the ignition sequence; it could be caused by a faulty igniter,
flame sensor, gas valve or improper line pressure or combustion. Check ignition
sequence to determine which component is not functioning.
(Control will retry
ignition sequence 1 hour after ER6 code originally occurs or if control is reset)
ER9
Internal Controller Fault
Indicates that the Controller has lost communication with an internal processor,
contact NTI.
ASO
Air Switch
Open
This is displayed when the boiler is
expecting the air switch to be
closed by a differential pressure
generated when the combustion
blower turns on. It can occur
momentarily during normal
operation. A problem is indicated
when ASO is displayed
continuously.
1.
Ensure the vinyl tubes, connected between the air switch and the ports on
the inlet pipe, are in the proper locations. Negative side of switch connects
to the port on the 1-1/2” PVC elbow.
2.
Check for blockage on the intake and exhaust vents.
3.
If fan is running the air switch may be faulty, ensure it is set at 0.2”wc.
4.
If fan is not running, check 120V wiring to blower, if ok remove low voltage
harness from blower, if blower fails to start, replace blower, if blower does
start the problem may be with blower or Controller.
ASC
Air Switch
Closed
This is displayed when the boiler
has turned the blower off and is
expecting the air switch to be
open. It can occur momentarily
during normal operation. A
problem is indicated when ASC is
displayed continuously.
1.
Does the combustion fan run continuously at full speed while the error is
displayed? If so check for 24V from transformer, also check transformer
fuse. If 24V is present check the low voltage wiring from Controller to
combustion blower, replace Controller or Blower.
2.
Is the combustion fan off? If so check for water in the air switch and air
switch tubes, replace switch if necessary.
3.
Check venting termination with required venting described in manual.
Controller
Locks-up
Excessive noise, current, or
voltage spikes in the 120V power
supply.
Contact NTI.
Bo
iler Co
n
tro
l (Red
F
ace)
Display Goes
Blank
No power to control or control
failure
1.
Check for 120V between terminals L1 and L2.
2.
If 120V exists turn power off and remove line voltage harness from Control.
Then check for resistance between L1 and L2 of control, if the circuit is open
(O.L) the internal fuse has blown. Check for shorts in wires leading to
circulator prior to replacing controller. (Note: If fuse is good the circuit will
read between 300 and 400 Ohms.)
3.
If 120V not present, check wiring and for 120V at source.