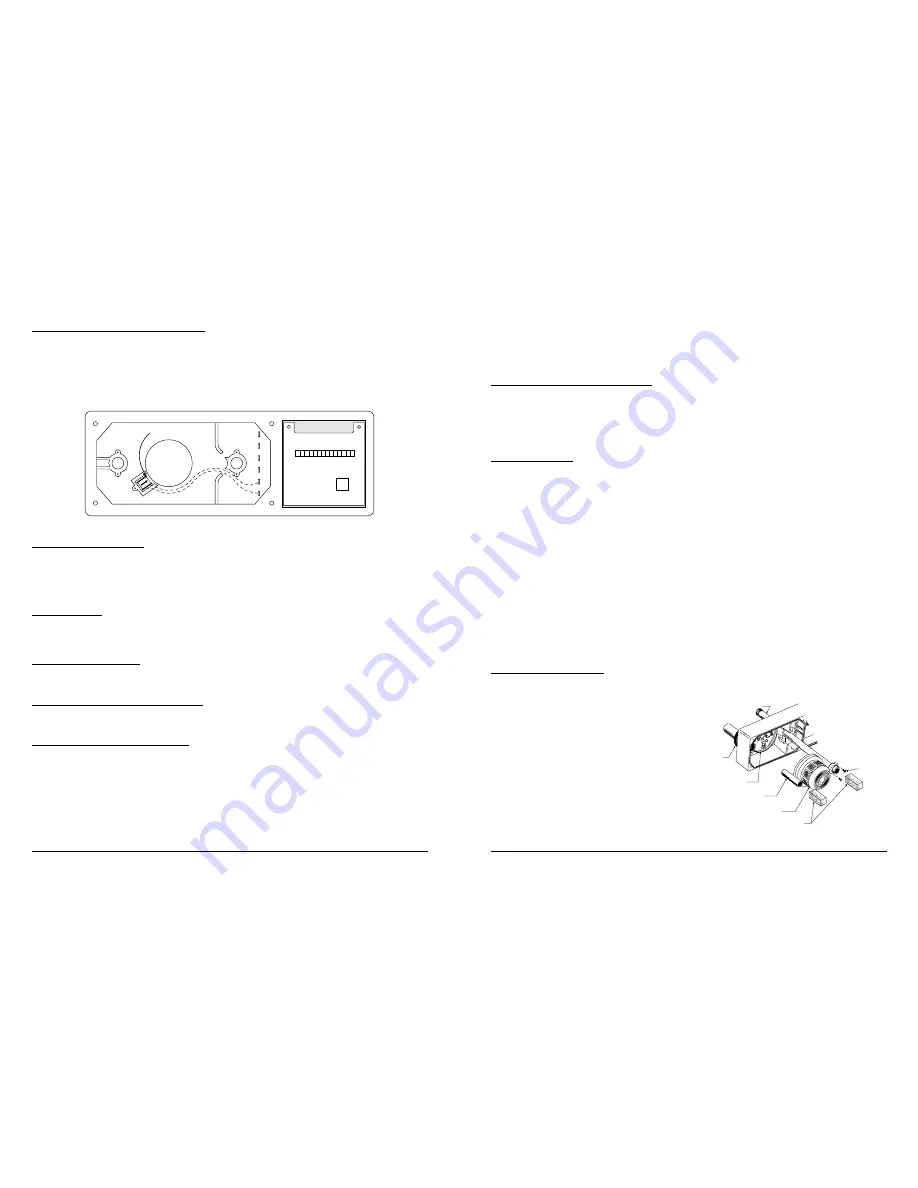
NOTE: Air currents inside the duct may cause excessive vibration. This vibration can slowly open the seal around the
tube and permit air to escape. To prevent this from occurring, a 3-inch floor flange, available at most plumbing
supply houses, may be used. This flange/connector mounting technique makes the initial installation easier
because a 1-inch to 1-1/4-inch hole may be drilled where the flange/connector will be used. It is easier to push
the inlet tube through the larger hole.
MODIFICATION OF INLET SAMPLING TUBES
There may be applications where duct widths are not what is specified for the installation. In such cases, it is
permissible to modify an inlet sampling tube that is longer than necessary to span the duct width.
Use a 0.193-inch diameter (#11) drill and add the appropriate number of holes so that the total number of holes
exposed to the air flow in the duct is 10 to 12. Space the additional holes as evenly as possible over the length of the
tube.
STEP 5. FIELD WIRING
Wiring Installation Guidelines
All wiring must be installed in compliance with the Canadian Electrical Code and the local codes having jurisdiction.
Proper wire gauges should be used. The conductors used to connect smoke detectors to control panels and accessory
devices should be color-coded to prevent wiring mistakes. Improper connections can prevent a system from
responding properly in the event of a fire.
For signal wiring, (the wiring between interconnected detectors or from detectors to auxiliary devices), it is
recommended that single-conductor wire be no smaller than 16 gauge (1.5 square mm), and that two- or three-
conductor wire be no smaller than 18 gauge (1.0 square mm). The last foot or so of conduit should be flexible steel
conduit (available in electrical supply houses) which facilitates easier installation and puts less strain on the conduit
holes in the housing. Solid conduit connections may be used if desired.
Smoke detectors and alarm system control panels have specifications for allowable loop resistance. Consult the
control panel manufacturer’s specifications for the total loop resistance allowed for the particular model control panel
being used before wiring the detector loop.
Wiring Instructions
The DHX-502 is designed for easy wiring. The housing provides a terminal strip with clamping plates. Wiring
connections are made by stripping approximately 1/2-inch of insulation from the end of the wire, sliding this bare end
under the plate, and tightening the clamping plate screw.
STEP 6. INSTALL THE FILTERS
Most duct installations are subject to dust accumulation. System filters remove a large percentage of this contami-
nation, but cannot remove all of it. Dust inside the duct detector causes problems. First, very fine particles of dust can
enter the detector sensing chamber and cause the unit to
go into alarm. Second, the accumulation of dust and dirt
necessitates a more frequent periodic cleaning schedule,
which can result in substantial cost and/or down time.
Disposable sampling tube filters can greatly reduce the
nuisance alarms caused by dust, and can also significantly
extend the maintenance interval. To install the sampling
tube filters, simply push the filter adapter into the exhaust
tube, and then push the filter onto the adapter tube on the
left, as shown in Figure 6. Then install the other filter over
the end of the inlet sampling tube.
B. RTS451/RTS451KEY REMOTE TEST STATION
The RTS451/RTS451KEY Remote Test Station facilitates test of the alarm capability of the duct detector as indicated
in the RTS451/RTS451KEY manual. The DHX-502 duct detector cannot be reset by the RTS451/RTS451KEY. It must
be reset at the system control panel.
To install the RTS451/RTS451KEY test coil, connect the device as shown in Figure 9;wire runs must be limited to 25
ohms or less per interconnecting wire. Place the coil in the detector housing with the arrow facing up and pointing
toward the detector as in Figure 9. Attach the coil leads to the housing terminals as shown; polarity is not important.
Firmly screw the bracket in place over the test coil.
DETECTOR
HEAD
TEST COIL
A78-1994-01
Figure 9. RTS451/RTS451KEY Test Coil Installation
7.3 MOD400 SENSITIVITY TEST
After verification of alarm capability, the MOD400 test module may be used with a voltmeter to check detector
sensitivity as indicated in the MOD400 installation manual. The housing cover must be removed to perform this test.
If the MOD400 readings indicate that the detector head is outside of the acceptable range, the detector head requires
cleaning. (See Periodic Maintenance Requirements on page 9.)
7.4 TROUBLE TEST
The capability of “TROUBLE” detection is tested by removing the detector head from the duct housing. The detector
head is removed by turning it counterclockwise about 10 degrees (Figure 8). The system control panel should indicate
a trouble condition. Reinserting the detector head should clear the trouble condition.
STEP 8. INSTALL THE COVER
Install the cover using the four screws. Be certain filters are installed as specified in Step 6. Make sure that the cover
fits into the base groove and that all gaskets are in their proper positions. Tighten the four cover screws to 10 in/lbs.
STEP 9. PERFORM THE FINAL SYSTEM CHECK
Place the magnet in position as shown in Figure 7. The LEDs on the detector should light. Any accessory LED(s) will
also light. The system control panel should indicate an alarm condition.
PERIODIC MAINTENANCE REQUIREMENTS
Air duct smoke detectors should be maintained at least once a year. They should be maintained more often if the
detector heads become obviously dirty in less than a year. The detectors must also be cleaned immediately after a
fire. Failure to properly maintain air duct smoke detectors may cause unnecessary false alarms.
It is recommended that a permanent Detector Test Log be set up and maintained, with a record for each individual
smoke detector in each building. Each detector should be clearly described, with information on the type of detector,
the model number, the serial number (if any), the location, and the type of environment. Data entries should include
test dates, type of test mode, test results, maintenance, and comments. A detector test log is included in this manual.
N500-04-00
8
I56-507-06
N500-04-00
5
I56-507-06
SAMPLING TUBE
FILTERS
SAMPLING TUBE
MOUNTING
SCREWS
DETECTOR HEAD
EXHAUST
FILTER ADAPTER
DETECTOR BASE
INLET SAMPLING TUBE
FOAM GASKET
A78-2106-00
Figure 6. Sampling Tube Filter Installation.