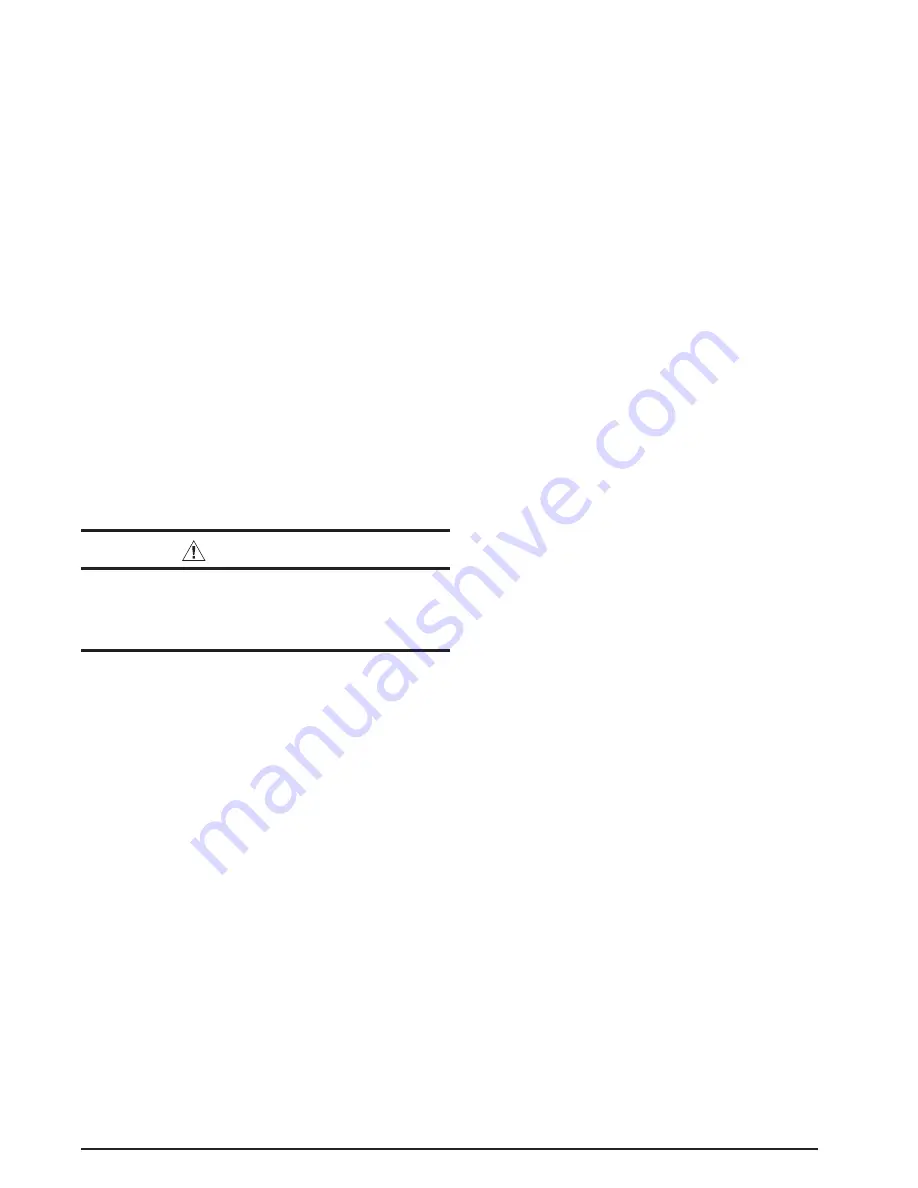
5
• Use transition fittings if the supply and/or return air openings
of the unit do not match the duct openings. These transitions
should be dimensioned in accordance with standard
practice as specified in the ASHRAE recommendations
for duct transitions.
• Flexible connectors may be used between the unit and the
ductwork to prevent transmission of vibration from the unit
to the structure. If electric heater kits are installed, heat
resistant material must be used for the flexible connector
at the supply air end of the unit.
• It is good practice to seal all connections and joints with
industrial grade sealing tape or liquid sealant. Requirements
for sealing ducts vary from region to region. Consult with
local codes for requirements specific to your area.
Unconditioned Spaces
All duct work passing through unconditioned space must
be properly insulated to minimize duct losses and prevent
condensation. Use insulation with an outer vapor barrier.
Refer to local codes for insulation material requirements.
Air Filters
B64 Series Air Handlers are not supplied with an air filter
when shipped from the factory. The installer must provide
a high velocity filter that is appropriately sized to the return
air duct opening or filter rack located in the bottom of the
unit. Accessing the filter does not require tools and can be
removed from the front of the unit by removing the filter
door. See Unit Maintenance (
) for filter sizes and
installation information.
WARNING:
Never operate the air handler without a filter
or with doors removed. Dust and lint can build
up on internal components, resulting in loss of
efficiency, equipment damage, and possible fire.
Acoustical Duct Work
• Certain installations may require the use of acoustical lining
inside the supply duct work. Acoustical insulation must be
in accordance with the current revision of the Sheet Metal
and Air Conditioning Contractors National Association
(SMACNA) application standard for duct liners. Duct lining
must be UL classified batts or blankets with a fire hazard
classification of FHC-25/50 or less.
• Fiber duct work may be used in place of internal duct liners
if the fiber duct work is in accordance with the current
revision of the SMACNA construction standard on fibrous
glass ducts. Fibrous duct work and internal acoustical
lining must be NFPA Class 1 air ducts when tested per
UL Standard 181 for Class 1 ducts.
• Damping ducts, flexible vibration isolators, or pleated
media-style filters on the return air inlet of the air handler
may be used to reduce the transmission of equipment
noise eminating from the air handler. These treatments
can produce a quieter installation, particularly in the
heated space. However, they can increase the pressure
drop in the duct system. Care must be taken to maintain
the proper maximum pressure rise across the air handler,
temperature rise and flow rate. This may mean increasing
the duct size and/or reducing the blower speed. These
treatments must be constructed and installed in accordance
with NFPA and SMACNA construction standards. Consult
with local codes for special requirements. For best sound
performance, be sure to install all the needed gaskets and
grommets around penetrations into the air handler, such
as for electrical wiring.
AIR HANDLER INSTALLATION
B64 series air handlers are shipped ready for vertical upflow
installation and are approved for attic, basement, alcove/closet
or crawlspace installation with zero clearance to combustibles.
See
for required installation clearances.
If installing an electric heater kit, please refer to the installation
instructions supplied with the kit for recommended duct
clearances to combustibles.
This appliance is approved only for indoor use.
• The unit must be leveled at installation and attached to a
properly installed duct system.
• The surface that the air handler is mounted on must provide
sound physical support of the unit.
• The air handler must be installed so that all electrical
components are protected from water.
• If a louvered door is installed across the front of this unit,
the appliance must be mounted flush or behind front edge
of finished wall.
• Always reinstall the doors on the air handler after servicing
or cleaning/changing the filters.
Do not operate the air
handler without all doors and covers in place.
Packaging Removal
Remove the shipping carton and User’s Manual from the
equipment. When removing the crate, use extra care so
tubing connections are not damaged. Do not pull on the
coils upper tubes.
Mounting Applications
Vertical only air handlers are factory ready for upflow
applications. These units may be applied in downflow
applications when applied with the appropriate field kit.
Factory ready horizontal air handlers may be applied in
upflow or horizontal-left and -right discharge applications.
These units may also be applied in downflow discharge when
applied with the appropriate field kit as specified in the units
Technical Specifications.
Through-the-floor installations require a 1/4” thick
noncombustible resilient gasket to be used whenever the
supply or return air ducts pass through the floor. The gasket
should be positioned between the duct, unit, and floor.
Upflow Installations
All air handlers are factory shipped, ready for upflow
installation. The horizontal drain pan may be removed from the
air handler when installing the unit in an upflow configuration.
All return air must enter from the bottom of the unit. A typical
upflow unit is shown in
Downflow Installations
The downflow accessory kit (See Technical Specifications) is
required for downflow applications. Instructions for installing
the downflow accessory kit are included with the kit. It is
recommended that the accessory be installed prior to installing
the unit. All return air in downflow applications must enter
through the top of the unit. A typical installation of the unit
in a downflow application is shown in
Horizontal Installations
The B64 Series air handler can be installed horizontally in
an attic, basement, crawl space or alcove. It can also be
suspended from a ceiling in a basement or utility room in
either a right to left airflow or left to right airflow as shown in
. Air handlers may or may not be shipped
from the factory with all the parts required for horizontal left
applications and horizontal right applications. If your unit
does not have parts for a horizontal application, a kit may
be available.