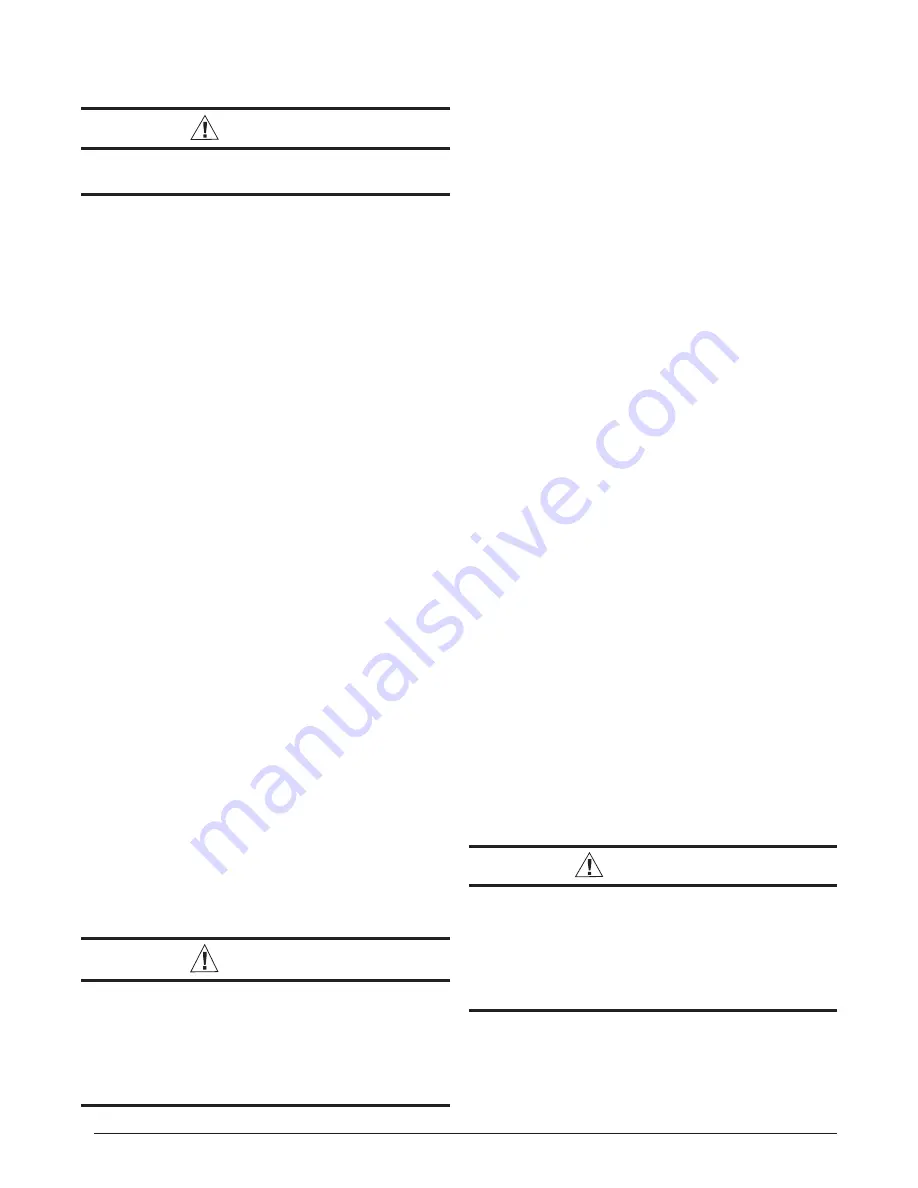
4
Operation of Furnace During Construction
CAUTION:
Failure to follow these instructions will void the
factory warranty and may signifi cantly reduce
the life or the performance of the furnace, and/
or result in other unsafe conditions. It is the
responsibility of the installing contractor to
insure these provisions are met.
Operating gas furnaces in construction environments can
cause a variety of problems with the furnace. Proper use
of commercial portable space heating equipment during
construction is recommended. This gas furnace may be
used during construction if it is not in violation of any
applicable codes and the following criteria are met:
• The installation must meet all applicable codes. The
furnace must be permanently installed according to
the instructions supplied with the furnace including
electrical supply, gas supply, duct work and venting. The
furnace must be controlled by a thermostat properly
installed according to the instructions supplied with the
furnace and thermostat. The installation must include
a properly installed fi lter in the return air system with
no by-pass air. The fi lter must be inspected frequently
and replaced when necessary.
• Combustion air must be supplied from outside the
structure and located such that dust and gases
from construction activity are not introduced into the
combustion system.
• Before occupying the structure: The fi lter must be
replaced or cleaned, the duct work must be inspected
and cleaned of any construction debris, and the furnace
must be cleaned and/or repaired if found to be dirty,
damaged, or malfunctioning in any way by a qualifi ed
HVAC technician. The furnace shall be inspected and
approved by applicable local authority even if this
requires redundant inspections.
• Serial numbers for furnaces used during construction
must be submitted in writing (fax and email also
acceptable). This information will be used to track the
long-term affects of the use during construction on
furnaces. Proof of this submittal shall be available for
the fi nal inspection of the furnace prior to occupancy.
• This furnace is designed to operate with return air
temperatures in ranges normally found in occupied
residences, including setbacks. Minimum continuous
return temperature must not be below 60° F (15° C).
Occasionally a temporary return temperature of 55° F
(12° C) is acceptable. However, operation with a return
temperature below 55° F (12° C) is not allowed.
Combustion Air Quality
CAUTION:
Combustion air must not be drawn from a
corrosive atmosphere.
To maximize heat exchanger life, the combustion air
must be free of chemicals that can form corrosive acidic
compounds in the combustion gases. The recommended
source of combustion air is to use outdoor air. However,
the use of indoor air in most applications is acceptable
except as listed:
• If the furnace is installed in a confi ned space, it is
required that the necessary combustion air come from
the outdoors by way of attic, crawl space, air duct, or
direct opening. For Installations in confi ned spaces, see
pages 7 - 8 for combustion air requirements.
• Installations in these locations may require outdoor air
for combustion, due to chemical exposures:
Commercial buildings
Buildings with indoor pools
Furnaces installed in laundry rooms
Furnaces installed in hobby or craft rooms
Furnaces installed near chemical storage areas
• Exposure to the following substances in the combustion
air supply may require outdoor air
for combustion:
Permanent wave solutions
Chlorinated waxes and cleaners
Chlorine based swimming pool chemicals
Water softening chemicals
De-icing salts or chemicals
Carbon tetrachloride
Halogen type refrigerants
Cleaning solvents (perchloroethylene)
Printing inks, paint removers, varnishes, etc.
Hydrochloric acid
Cements and glues
Antistatic fabric softeners
Masonry acid washing materials
Installation in a Garage
WARNING:
Do not place combustible materials on or
against the furnace cabinet or within 6 inches
of the vent pipe. Do not place combustible
materials, including gasoline or any other
fl ammable vapors and liquids, in the vicinity
of the furnace.
This gas-fi red furnace may be installed in a residential
garage with the provision that the burners and igniter
are located no less than 18 inches (457mm) above the
fl oor. The furnace must be located or protected to prevent
physical damage by vehicles.