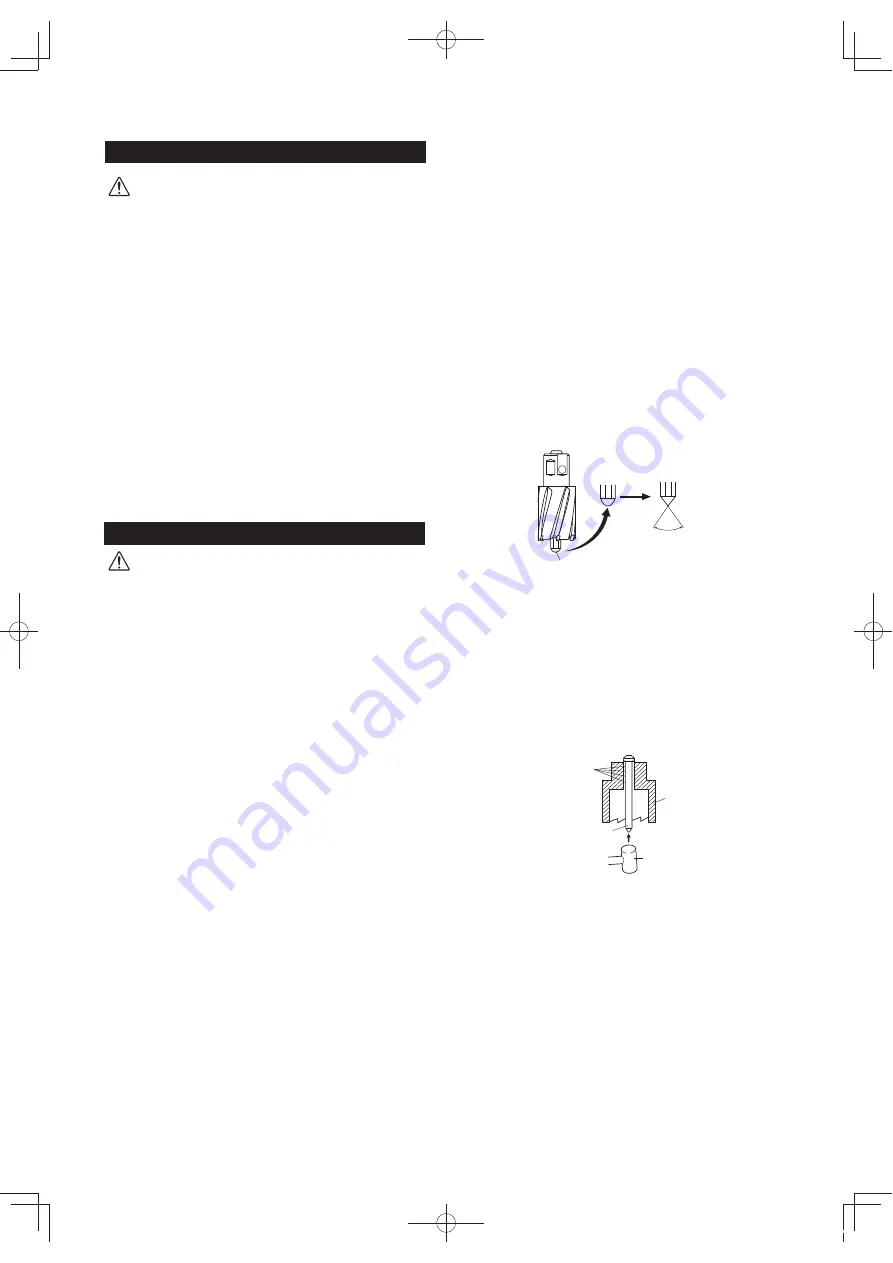
19
8 TROUBLESHOOTING
WARNING
●
Do not attempt to repair the tool by yourself.
This will cause damage to the tool and danger to
yourself when you use it again.
●
If any of the following, or other symptoms occur,
or if there are other matters concerning usage
that you do not understand, please consult the
sales agent from whom you purchased the tool or
an authorized dealer.
Various errors are indicated by LED with this
machine in which the contents of error can be
identi
fi
ed by the color of LED.
Refer to “4-4 Various Safety Functions and
Error Detection Functions” for details including
countermeasures for various errors.
9 MAINTENANCE AND INSPECTION
WARNING
●
When performing maintenance or inspection work,
turn the magnet switch off and remove the battery
pack from the machine. Furthermore, unplug the
power supply plug of the charger from the electric
outlet.
●
Periodically check for looseness of screws
fastened at each part. Tighten the screw if it is
loose.
●
After work, store at a dry area where the
temperature is less than 50°C and is out of reach
of children.
●
After work, do not store at an area where volatile
that has possibility of ignition or explosion is kept.
●
Do not put conductive items such as chips, nails
and copper wires in the storage case.
●
Attach a terminal cover to the battery pack when
storing.
9-1 Greasing of sliding surfaces
From time to time, the sliding surfaces between the
body and the Slide Board should be greased.
9-2 Loose Slide Board adjustment
●
When adjusting looseness of the slide board,
check that the slide board is located at the slide
b o a r d a d jus t m e n t s c r e w p o si t ion b e f o r e
tightening.
Any looseness between the body and the Slide
Board will adversely affect drilling precision, leading
to premature wear on the cutter. When looseness is
encountered, eliminate it by uniformly re-tightening
the four Slide Board adjustment screws on the
lateral side of the body to the extent that the Drill
Motor will not fall under its dead weight. The screws
are designed to work as a double-lock, so they
should be securely tightened by turning the nuts.
9-3 Sharpening of Pilot Pin tip
If the Pilot Pin tip is dull, the pin will not be able to
fi
t
itself into the punching hole, causing poor drilling
precision. It should be inspected from time to time,
and , if the Pilot Pin tip is found to be dull, sharpen the
tip or replace with a new one. Exercise caution during
the sharpening operation as any rough grinding
softens the tip due to annealing, even to the point of
disabling it in some cases. (Fig. 34)
Pilot Pin
Sharpen
the tip
Optimal angle 70°
(Fig. 34)
9-4 Loosen a tight Pilot Pin
When the cutter needs to be replaced, pull out and
change the Pilot Pin which acts as a guide. However, if
Metal chips are caught between the cutter and the pin,
the pin may be dif
fi
cult to be pulled out. Tap the end of
the pin gently with a wooden mallet as you pull it out.
(Fig. 35)
Pilot Pin
Cutter
Metal chips
Wooden mallet
(Fig. 35)
9-5 Cutter grinding
When the cutter needs re-grinding, consult the sales
agent from whom you purchased the tool or an authorized
dealer.
9-6 Inspection and Replacement of Carbon Brush
Periodically inspect the abrasion condition of the
carbon brush.
Replace the carbon brush with a new carbon brush
when the remaining length of the carbon brush is 8 to
9 mm since the recti
fi
cation will deteriorate and may
cause machine failure when left unreplaced. (Fig. 36)
15.+/2+..]AJ?+050.]C,glbb/7
/2,7,/.28//8.7NK