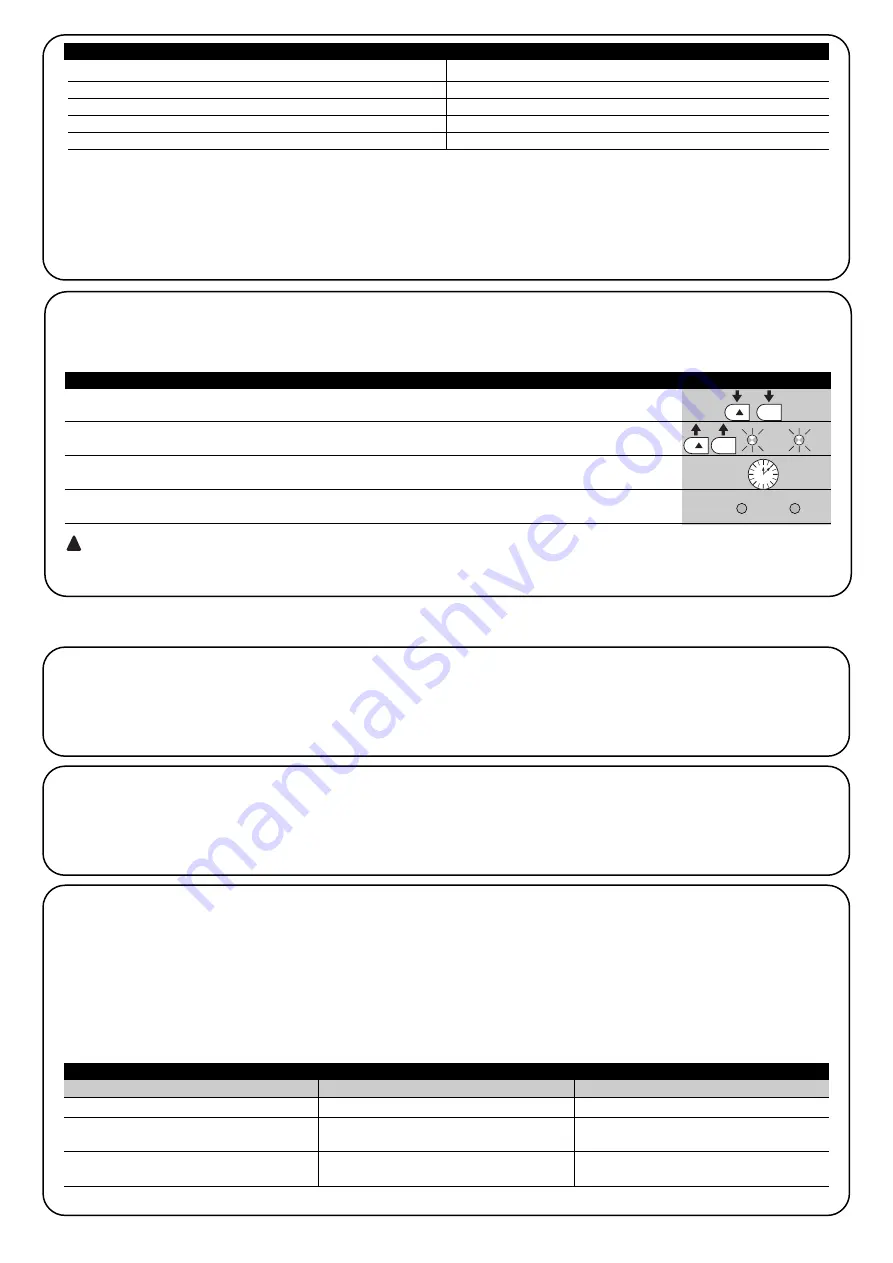
19
GB
7.4.1) “Always open” Function
The “Always open” function is a control unit feature which enables the
user to control an opening manoeuvre when the “Step-by-Step” com-
mand lasts longer than 2 seconds. This is useful for connecting a timer
contact to the “Step-by-Step” terminal in order to keep the gate open for
a certain length of time, for example. This feature is valid with any kind of
“Step-by-Step” input programming, except for “Close”. Please refer to
the “Step-by-Step Function” parameter in Table 9.
7.4.2) Move anyway” function
In the event that one of the safety devices is not functioning proper-
ly or is out of use, it is still possible to command and move the gate
in “Man present” mode.
Please refer to the Paragraph “Control with safety devices out of
order” in the enclosure “Instructions and Warnings for users of the
ROBUS gearmotor” for further information.
7.4.3) Maintenance warning
With ROBUS the user is warned when the automation requires a mainte-
nance control. The number of manoeuvres after the warning can be select-
ed from 8 levels, by means of the “Maintenance warning” adjustable para-
meter (see table 9).
Adjustment level 1 is “automatic” and takes into consideration the severity
of the manoeuvre, this being the force and duration of the manoeuvre, while
the other adjustments are established based on the number of manoeuvres.
The maintenance request signal is given by means of the flashing light
(Flash) or by the light connected to the S.C.A. output when pro-
grammed as a “Maintenance light” (see table 9). The flashing light
“Flash” and the maintenance light give the signals indicated in table
16, based on the number of manoeuvres performed in respect to the
limits that have been programmed.
7.4) Special functions
Tabella 14: ROBUS Slave programming independent from ROBUS Master
Level one functions (ON-OFF functions)
Level two functions (adjustable parameters)
Stand-by
Motor speed
Peak
Open Gate Indicator Output
Slave Mode
Motor force
Error list
On Slave it is possible to connect:
• A flashing light (Flash)
• An open gate light (S.C.A.)
• A sensitive edge (Stop)
• A command device (Step by Step) that controls the complete opening of the Slave leaf only.
• The Open and Close inputs are not used on the Slave
7.3.6) Recognition of Other Devices
Normally the recognition of the devices connected to the BlueBUS and the STOP input takes place during the installation stage. However, if new
devices are added or old ones removed, the recognition process can be gone through again by proceeding as shown in Figure 15.
1.
Press keys
[
▲
]
and
[Set]
and hold them down
2.
Release the keys when L1 and L2 LED’s start flashing very quickly (after approx. 3 s)
L1
L2
3.
Wait a few seconds for the control unit to finish recognizing the devices
4.
When the recognition stage is completed L1 and L2 LED’s will go off, the STOP LED must remain on,
while L1…L8 LED’s will light up according to the status of the relative ON-OFF functions
L1
L2
After you have added or removed any devices, the automation system must be tested again according to the directions
contained in paragraph 5.1 “Testing”.
!
Tabella 15: Recognition of Other Devices
Example
SET
SET
Number of manoeuvres
Flash signal
Maintenance light signal
Lower than 80% of the limit
Between 81 and 100% of the limit
Over 100% of the limit
Normal (0.5s on, 0.5s off)
Remains on for 2s at the beginning of the
manoeuvre then carries on normally
Remains ON for 2s at the start and end of
the manoeuvre then carries on normally
On for 2s when opening begins
Flashes throughout the manoeuvre
Always flashes .
Tabella 16: maintenance warning with Flash and maintenance light