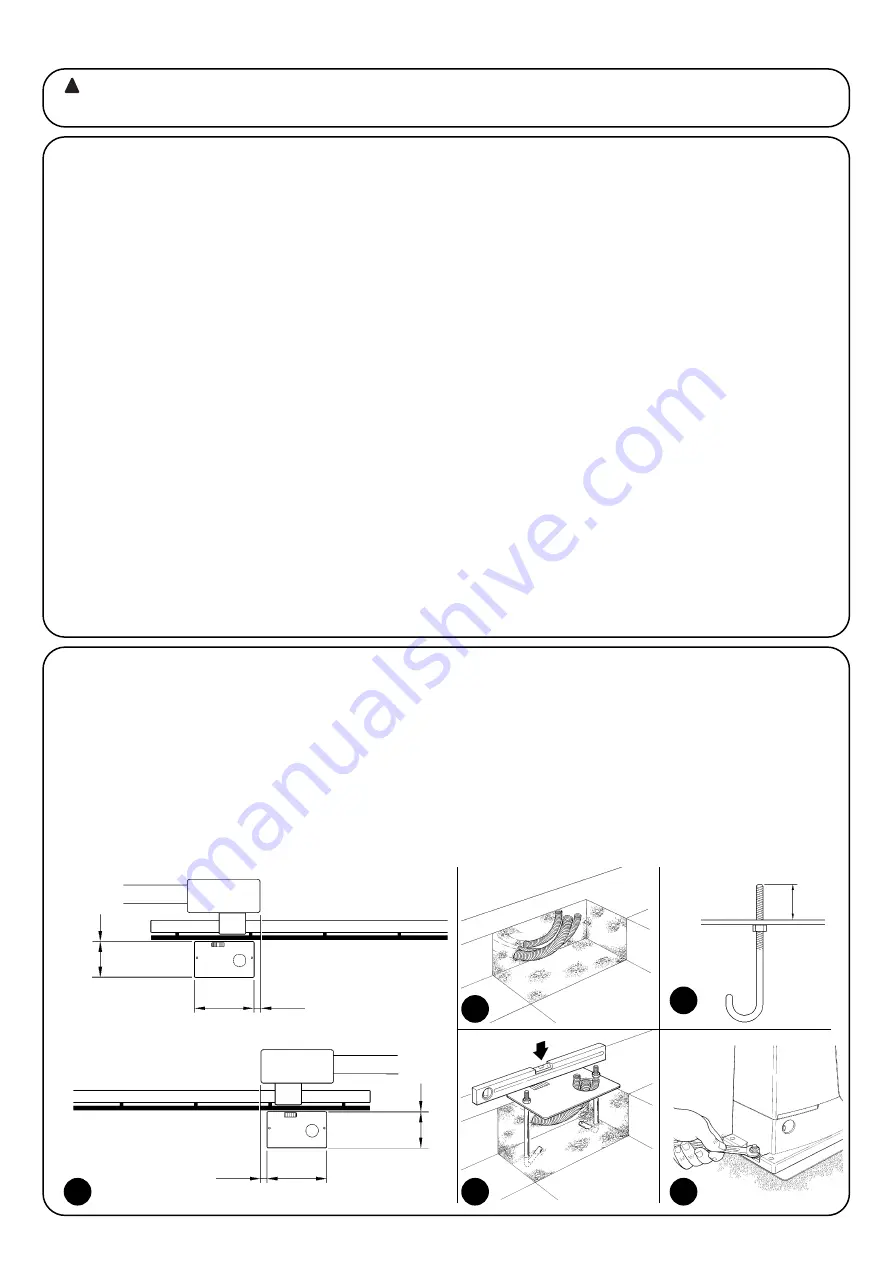
7
GB
7
3.2) Installation of the gearmotor
The gearmotor must be fastened directly to an already existing
mounting surface using suitable means, for example expansion
screw anchors. Otherwise, in order to fasten the gearmotor the
installer must:
1.
Dig a foundation hole with suitable dimensions referring to Figure 3.
2.
Prepare one or more conduits for the electrical cables as shown
in figure 4.
3.
Assemble the two clamps on the foundation plate setting one nut
underneath and one on top of the plate. The nut underneath the
plate must be as shown in Figure 5 screwed so that the thread-
ed part protrudes above the plate by approximately 25÷35 mm.
4.
Pour the concrete and, before it starts to harden, set the founda-
tion plate to the values shown in Figure 3. Check that it is paral-
lel to the leaf and perfectly level (Figure 6). Wait for the concrete
to harden completely.
5.
Remove the 2 upper nuts of the plate and then place the gear-
motor onto them. Check that it is perfectly parallel to the leaf,
then screw the two nuts and washers supplied, as shown in Fig-
ure 7.
The installation of ROBUS must be carried out by qualified personnel in compliance with current legislation, standards and
regulations, and the directions provided in this manual.
!
3) Installation
3.1) Preliminary checks
Before proceeding with the installation of ROBUS you must:
•Check that all the materials are in excellent condition, suitable for
use and that they conform to the standards currently in force.
• Make sure that the structure of the gate is suitable for automation.
• Make sure that the weight and dimensions of the leaf fall within the
specified operating limits provided in chapter “2.1 Operating lim-
its”.
• Check that the force required to start the movement of the leaf is
less than half the “maximum torque”, and that the force required to
keep the leaf in movement is less than half the “nominal torque”.
Compare the resulting values with those specified in Chapter “8
Technical Characteristics”. The manufacturers recommend a 50%
margin on the force, as unfavourable climatic conditions may
cause an increase in the friction.
• Make sure that there are no points of greater friction in the open-
ing or closing travel of the gate leaves.
• Make sure there is no danger of the gate derailing.
• Make sure that the mechanical stops are sturdy enough and that
there is no risk of the deformation even when the leaf hits the
mechanical stop violently.
• Make sure that the gate is well balanced: it must not move by itself
when it is placed in any position.
•Make sure that the area where the gearmotor is fixed is not subject
to flooding. If necessary, mount the gearmotor raised from the
ground.
• Make sure that the installation area enables the release of the gear-
motor and that it is safe and easy to release it.
• Make sure that the mounting positions of the various devices are
protected from impacts and that the mounting surfaces are suffi-
ciently sturdy.
• Components must never be immersed in water or other liquids.
• Keep ROBUS away from heat sources and open flames; in acid,
saline or potentially explosive atmosphere; this could damage
ROBUS and cause malfunctions or dangerous situations.
• If there is an access door in the leaf, or within the range of move-
ment of the gate, make sure that it does not obstruct normal trav-
el. Mount a suitable interblock system if necessary.
• Only connect the control unit to a power supply line equipped with
a safety grounding system.
• The power supply line must be protected by suitable magneto-
thermal and differential switches.
• A disconnection device must be inserted in the power supply line
from the electrical mains (the distance between the contacts must
be at least 3.5 mm with an overvoltage category of III) or equiva-
lent system, for example an outlet and relative plug. If the discon-
nection device for the power supply is not mounted near the
automation, it must have a locking system to prevent unintention-
al, unauthorised connection.
3
4
5
6
25÷35
7
192
330
0÷50
0÷50
330
192
0÷10
0÷10