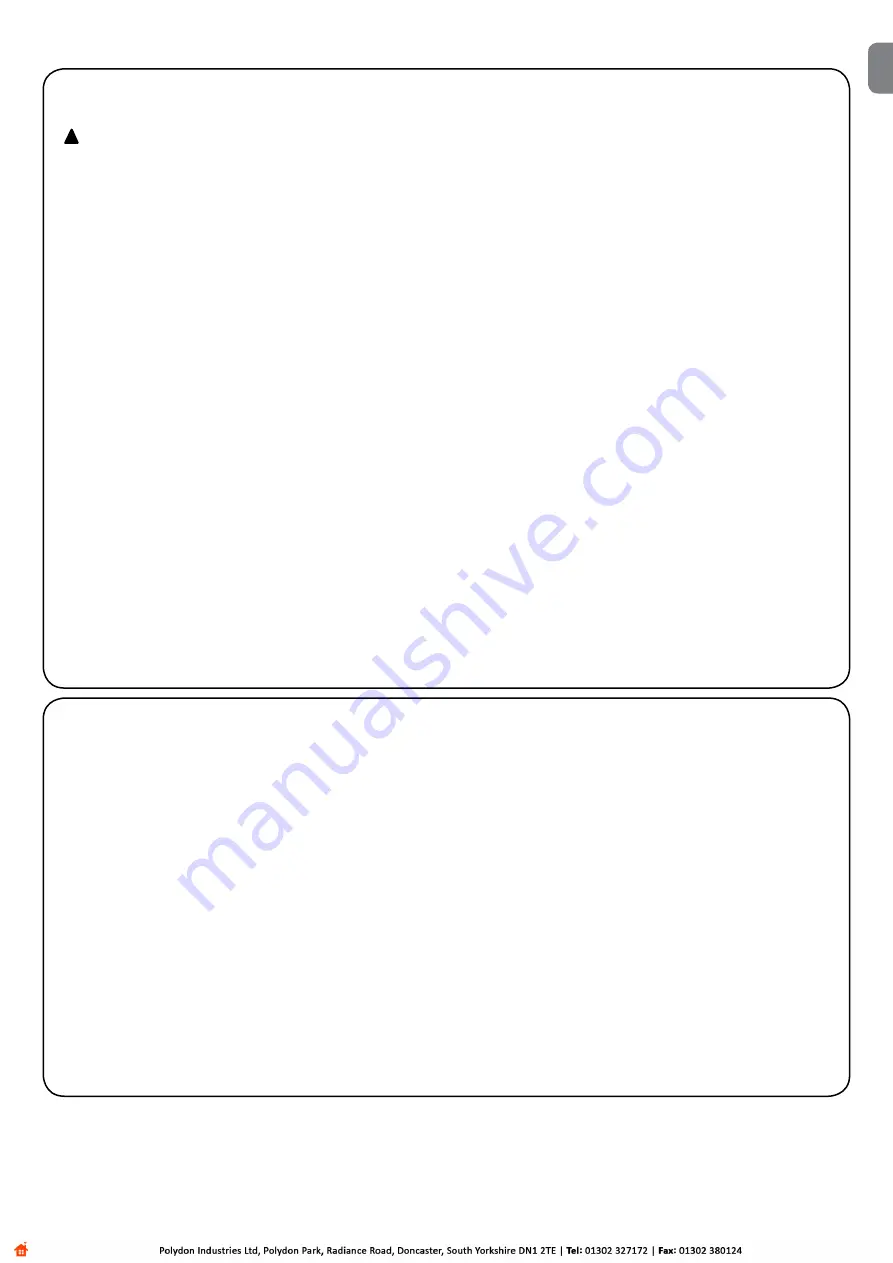
13
After the above checks and adjustments have been made, the sys-
tem can be tested.
!
The automation system must be tested by qualified and
experienced personnel who must establish what tests to per-
form based on the risks involved.
Testing is the most important part of the whole automation process.
Each single component, e.g. motor, emergency stop, photocells,
etc., may require a specific test phase; please follow the procedures
described in the operating instructions for each component.
To test the control unit, perform the following operations:
1.
Function selection:
• Set Dip Switch 1 to ON (Semi-automatic operation) and the
remaining ones to OFF
2.
Press the Open button and check that:
• the flashing light is activated
• the opening manoeuvre starts
• the movement stops when the opening limit stop is reached.
3.
Press the Close button and check that:
• the flashing light is activated
• the closing manoeuvre starts
• the movement stops when the closing limit stop is reached.
4.
Start an opening manoeuvre and make sure that during the
manoeuvre the triggering of a device:
• connected to the “Stop” input causes an immediate stop and a
short reverse run
• connected to the “Photo” input has no effect.
5.
Start a closing manoeuvre and make sure that during the
manoeuvre the triggering of a device:
• connected to the “Stop” input causes an immediate stop and a
short reverse run
• connected to the “Photo” input causes the stop and subse-
quent reversal of the manoeuvre
• connected to the “Photo1” input causes the stop and subse-
quent reversal of the manoeuvre.
6.
On the connected inputs, make sure that each activation of the
input generates a step in the following sequence:
• Step-by-step input: Sequence = Open – Stop – Close – Stop
• Open input: Sequence = Open – Stop – Open – Stopp
• Close input: Sequence = Close – Stop – Close – Stop
7.
If the “Phototest” function is used, check the efficiency of the test:
• Interrupt the “Photo” photocell, then start a manoeuvre and
check that it is not performed
• Interrupt the “Photo1” photocell, then start a manoeuvre and
check that it is not performed
• Short the “Photo” photocell contact, then start a manoeuvre
and check that it is not performed
• Short the “Photo1” photocell contact, then start a manoeuvre
and check that it is not performed
8.
Perform the tests for measuring the Impact Forces as required by
EN 12445.
If after the completion of the testing process additional functions are
activated which could affect the safety of the system, specific testing
of these functions must be performed.
6) Testing
6.1) Commissioning
Commissioning can take place only after all the testing phases of the
control unit and the other devices have been completed successfully.
It is not permissible to execute partial commissioning or to enable
use of the system in makeshift conditions.
1.
Prepare and store for at least 10 years the technical documenta-
tion for the automation, which must include at least the following:
assembly drawing of the automation, wiring diagram, analysis of
hazards and solutions adopted, manufacturer’s declaration of
conformity of all the devices installed (for A60 use the annexed
CE declaration of conformity); copy of the instruction manual and
maintenance schedule of the automation.
2.
Affix a dataplate on the gate providing at least the following
data:type of automation, name and address of manufacturer
(person responsible for the “commissioning”), serial number, year
of manufacture and “CE” marking.
3.
Post a permanent label or sign near the gate detailing the opera-
tions for the release and manual manoeuvre.
4.
Prepare the declaration of conformity of the automation system
and deliver it to the owner.
5.
Prepare the “Instructions and warnings for the use of the automa-
tion system” and deliver it to the owner.
6.
Prepare the maintenance schedule of the automation system and
deliver it to the owner (this must provide all directions regarding
the maintenance of the single automation devices).
7.
Before commissioning the automation system inform the owner in
writing regarding residual risks and hazards (e.g. in the “Instruc-
tions and warnings for the use of the automation system”).
EN
www.metalines.com
Содержание mindy A60
Страница 104: ...104 RU 3 2 3a 180 3 3 1 A60 3 5 III 3a 3b 3c 3d www metalines com sales metalines com...
Страница 106: ...106 RU 5 5a 2 EN 954 1 12 1996 10 5 5a 1 75 17 18 1 19 24 5a 10 1 1 3 5 www metalines com sales metalines com...
Страница 107: ...107 RU 3 6 17 18 24 OK NC FCA FCC M1 8 10 M2 11 13 OK 1 3 www metalines com sales metalines com...
Страница 109: ...109 RU 5 4 1 5 1 1 2 3 4 5 5 6 1 7 8 9 10 11 12 1 www metalines com sales metalines com...
Страница 111: ...111 RU 1 1 2 3 4 5 1 6 7 1 1 8 EN 12445 6 6 1 1 A60 10 2 CE 3 4 5 6 7 12 2 www metalines com sales metalines com...
Страница 113: ...113 RU Nice Nice A60 www metalines com sales metalines com...