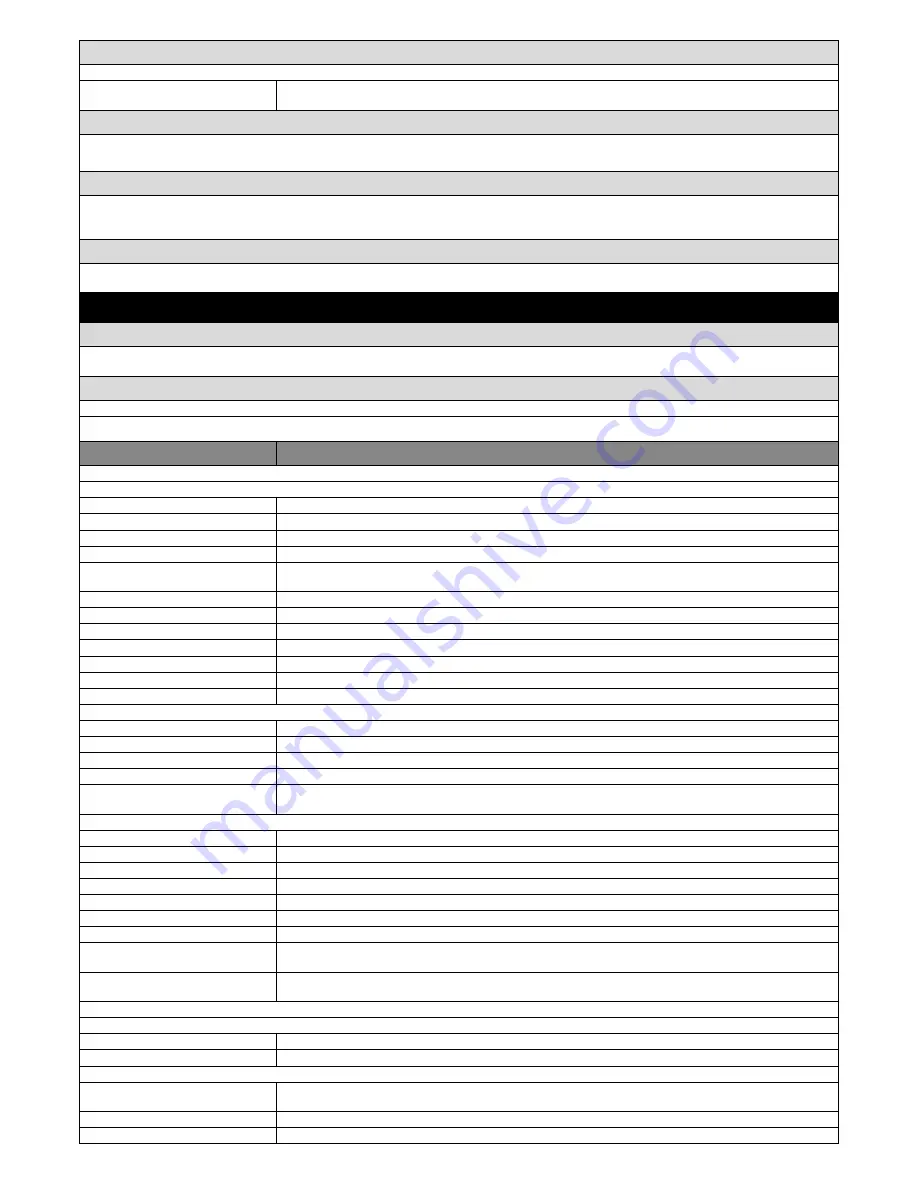
output 3
This output can be set to one fo the functions described in Table 3, including those described below
Fan (0x20)
This function activates the output (fan) when the barrier is moving, and for 1 minute after the end of a manoeuvre.
Output active 24 V DC / max 10W
Electric lock time
This parameter (in seconds) can be set to 0.1 - 10 s; the factory setting is 2 s. This function sets the time for which the output programmed as the electric
lock remains active.
Suction cup time
This parameter is expressed in seconds and can be set with a value from 0.1 to 10 sec.; the factory setting is 2 sec. This function enables programming on
the Control unit of the required time interval to pass between the end of a Closing manoeuvre and the start of an Opening manoeuvre, when the suction cup
is disengaged.
Courtesy light time
This parameter is expressed in seconds and can be set with a value from 0 to 250 sec.; the factory setting is 60 sec. This function programs the courtesy
light on time for the various outputs.
DIAGNOSTICS
Inputs / Outputs
This function enables the display of the operating status of all inputs and outputs present on the control unit. The functions of the inputs and outputs are
described in Table 4.
Automation position
Indicates the physical position of the encoder in encoder pulses relative to the closed position.
TABLE 4: Input/output DIAGNOSTICS
FUNCTION
DESCRIPTION
• Diagnosis 1 - IN
RADIO INPUTS (On / Off):
Channel 1
Indicates when radio receiver channel 1 is active.
Channel 2
Indicates when radio receiver channel 2 is active.
Channel 3
Indicates when radio receiver channel 3 is active.
Channel 4
Indicates when radio receiver channel 4 is active.
SERIAL RADIO INPUTS
Indicates when the control unit receives a serial command via BusT4 from a radio receiver; these commands range
from minimum 1 to maximum 15.
Loop1
Indicates when the loop is activated due to occupation by a metal body.
Loop2
Indicates when the loop is activated due to occupation by a metal body.
BOARD KEYS:
no. 1
Indicates when key 1 is pressed (= OPEN) on the control unit.
no. 2
Indicates when key 2 is pressed (= STOP) on the control unit.
no. 3
Indicates when key 3 is pressed (= CLOSE) on the control unit.
DIRECTION SELECTION
Indicates the status of the direction selector for a manoeuvre.
INPUT STATUS:
inp 1
Indicates when input 1 is active.
inp 2
Indicates when input 2 is active.
inp 3
Indicates when input 3 is active.
inp alt
Indicates when the alt input is active.
ALT CONFIGURATION
Indicates the type of connection on the alt terminal. The connections are of three types: not configured; NC; NO; 1
8K2 resistive edge; 2 8K2 resistive edges; 1 OSE optical edge; out of range.
MOTOR 1 (On / Off):
Limit switch on opening
Indicates when motor 1 reaches the maximum opening position.
Limit switch on closing
Indicates when motor 1 reaches the maximum closing position.
MANOEUVRE THRESHOLD:
Indicates the operating status of the manoeuvre limiter, expressed in levels:
Level 1: OK;
Level 2: THRESHOLD 1; the manoeuvre is started with a 2 second delay;
Level 3: THRESHOLD 2; the manoeuvre is started with a 5 second delay;
Level 4: MOTOR ALARM; the manoeuvre is only enabled with the hold-to-run control.
LAST 8 MANOEUVRES
Indicates any malfunctions occurring during normal operation of the application, showing the last 8 manoeuvres
completed.
OPEN
AUTOMATIC
Indicates if this function is active.
• Diagnosis 1 - OUT
GENERIC DATA:
Stand-by
Indicates when the automation is in the standby status.
POWER:
Indicates the type of electrical power used by the automation: mains (120/230 V AC) or backup battery (24 V DC)
MEMORY ERRORS:
Map M1
Indicates whether there is an error in the memorised data, related to the values for the force required by motor 1 to
complete a manoeuvre.
Rego
Indicates whether there is an error in the memorised data on the control unit regarding settable parameters.
Functions
Indicates whether there is an error in the memorised data regarding the functions programmable with Oview.