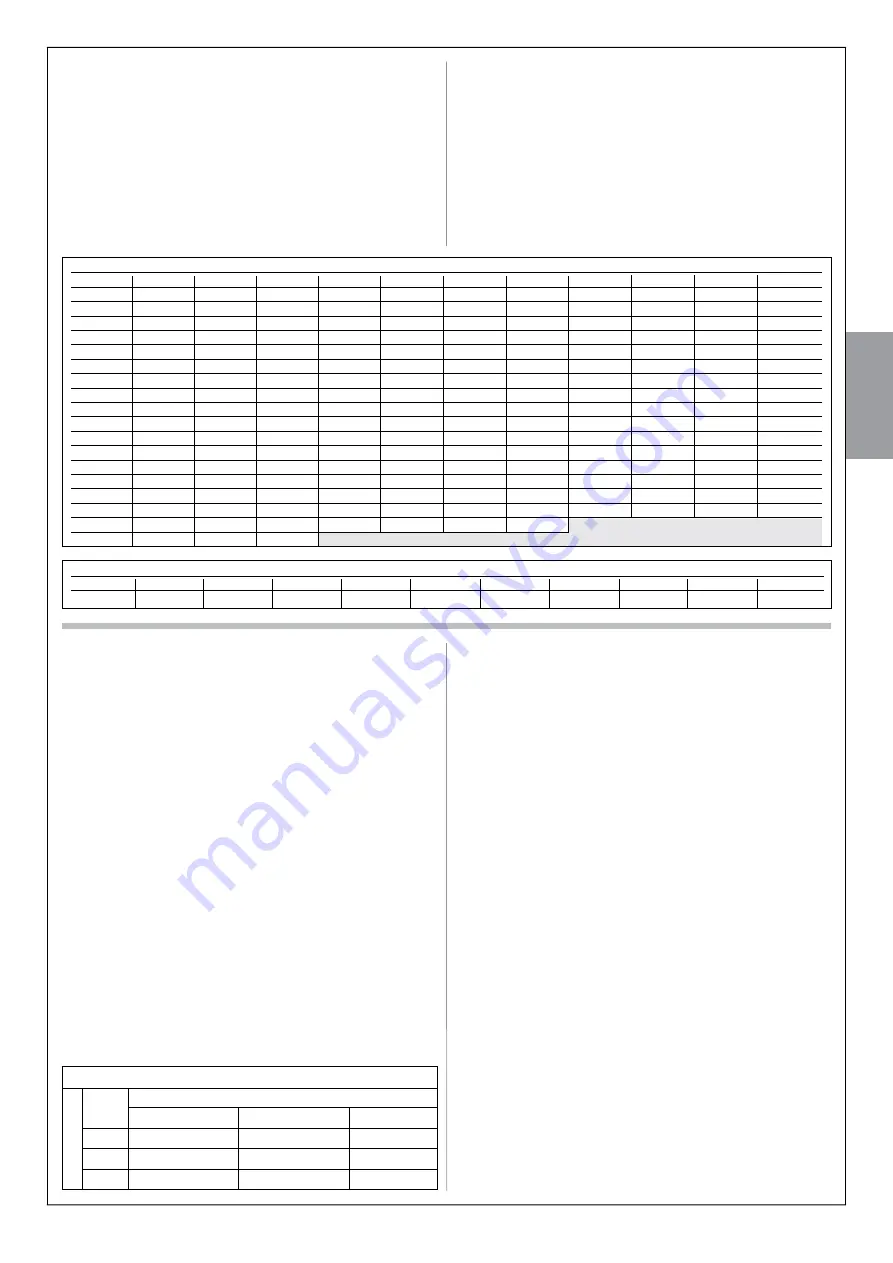
English –
15
English
06.
In
table A
below, select the box corresponding to the intersection of
the row with the value of Ed and the column with the value of K. The
box contains the maximum possible number of cycles per day (e.g.
Ed= 2800 and K= 105; daily cycles ≈ 22).
If the number obtained is too low for the intended use or is located in the
“area not recommended for use”, 2 or more photovoltaic panels may be
considered, or use of a photovoltaic panel with a higher power. Contact
the Nice technical assistance service for further information.
The method described, allows you to calculate the maximum possible num-
ber of cycles
per day
that the automation is capable of carrying out, accord-
ing to the solar energy supplied. The calculated value is considered an aver-
age value and the same for all days of the week. Considering the presence
of the battery, which acts as an energy “accumulator”, and the fact that the
battery also provides automation autonomy for long spells of bad weather
(when the photovoltaic panel produces very little energy) it may be possible to
exceed the calculated maximum possible number of cycles per day, provided
that the average of 10-15 days remains within the envisaged limits.
Table B
below shows the maximum possible number of cycles, accord-
ing to the
severity index
(K) of the manoeuvre, using
the stored solar
energy
of the accumulator. It is considered that initially the battery is
completely charged (e.g. after a prolonged period of good weather or
recharging via the optional PCB power supply unit) and that the manoeu-
vres are performed within a period of 30 days.
When the battery runs out of the stored energy, the led starts to indicate
the battery low signal by flashing briefly every 5 seconds, accompanied
by a “beep”.
TABLE A - Maximum possible number of cycles per day
Ed
K≤75
K=100
K=125
K=150
K=175 K=200
K=225
K=250
K=275
K=300
K≥325
9500
123
92
74
61
53 46
41
37
33
31
28
9000
116
87
70
58
50 44
39
35
32
29
27
8500
109
82
66
55
47 41
36
33
30
27
25
8000
103
77
62
51
44 39
34
31
28
26
24
7500
96
72
58
48
41 36
32
29
26
24
22
7000
89
67
54
45
38 34
30
27
24
22
21
6500
83
62
50
41
35 31
28
25
23
21
19
6000
76
57
46
38
33 29
25
23
21
19
18
5500
69
52
42
35
30 26
23
21
19
17
16
5000
63
47
38
31
27 24
21
19
17
16
14
4500
56
42
34
28
24 21
19
17
15
14
13
4000
49
37
30
25
21 19
16
15
13
12
11
3500
43
32
26
21
18 16
14
13
12
11
10
3000
36
27
22
18
15 14
12
11
10
9
8
2500
29
22
18
15
13 11
10
9
8
7
7
2000
23
17
14
11
10 9
8
7
6
6
5
1500
16
12
10
8
7 6
5
1000
9 7 6
TABLE B - Maximum number of cycles using exclusively battery power
K≤75
K=100
K=125
K=150
K=175
K=200
K=225
K=250
K=275
K=300
K≥325
741
556
445
371
318
278
247
222
202
185
171
Area of use not recommended
9.3 - ADDING OR REMOVING DEVICES
Devices can be added to or removed at any time.
Warning! – Do not add devices before you have checked that they
are fully compatible with the control unit and the motor it controls;
for details please refer to the NICE Support Service.
9.3.1 - ECSbus
ECSbus is a system that enables connections of ECSbus devices using
just two wires, which convey both electrical power and communication
signals. All devices are connected in parallel on the same 2 wires of the
ECSbus; each device is recognised individually as it is assigned a unique
address during installation.
Photocells and other devices using this system can be connected to
ECSbus, such as safety devices, control buttons, indicator lights etc. For
information about ECSbus devices, see the Nice Home product cata-
logue or visit www.niceforyou.com.
A special learning phase enables the control unit to recognise all con-
nected devices individually, and enables precise diagnostics procedures.
For this reason, each time a device connected to ECSbus is added or
removed, the learning phase must be performed on the control unit; see
paragraph 10.3.3 “Learning other devices”.
9.3.2 - STOP Input
STOP is the input that causes immediate shutdown of the movement (fol-
lowed by a brief inversion of the manoeuvre). Devices with output featur-
ing normally open “NO” contacts, and devices with normally closed “NC”
contacts, as well as devices with 8.2k
Ω
constant resistance output, like
sensitive edges, can be connected to this input.
Multiple devices, even of different types, can be connected to the STOP
input if suitable arrangements are made; see
Table 7
.
TABLE 7
2
nd
device type:
1
st
device type:
NO
NC
8,2K
Ω
NO
In parallel (
note 2
)
(
note 1
)
In parallel
NC
(
note 1
)
In series (
note 3
)
In series
8,2K
Ω
In parallel
In series
(
note 4
)
Note 1.
NO and NC combinations are possible by placing the 2 con-
tacts in parallel, taking care to place a 8.2 k
Ω
resistance in parallel to
the NC contact (thus enabling the combination of 3 devices: NO, NC
and 8.2k
Ω
).
Note 2.
Any number of NO devices can be connected to each other in
parallel.
Note 3.
Any number of NC devices can be connected to each other in
series.
Note 4.
Only two devices with 8.2k
Ω
constant resistance output can be
connected in parallel; if needed, multiple devices must be connected in
“cascade” configuration with a single 8.2 k
Ω
terminal resistance.
Warning! – If the STOP input is used to connect devices with safety
functions, only the devices with 8.2K
Ω
constant resistance output
guarantee safety category 3.
As with the ECSbus, the control unit recognises the type of device con-
nected to the STOP input during the learning phase; subsequently the
control unit gives a STOP command when it detects a variation with
respect to the learned state.
9.3.3 - Recognition of other devices
The learning operation of the devices connected to the ECSbus and
STOP input is usually carried out during the installation phase; if devices
are added or removed the learning operation can be carried out again as
follows:
01.
Press the
P2
button
[B]
(
fig. 21
) on the control unit for at least three
seconds, then release the button.
02.
Wait a few seconds for the control unit to complete the device learn-
ing phase.
03.
When the recognition procedure is complete, the
P2
led
[A]
(
fig. 21
)
will go off. If the
led
P2
flashes it means there is an error; see para-
graph 10.5 “Troubleshooting”.
04.
After having added or removed a device the automation test must be
carried out again as specified in paragraph 7.1 “Testing”.
Содержание CLB207
Страница 2: ...Fran ais...
Страница 9: ...Fran ais 7 Fran ais 8 7 1 Led SAFE 3 2 4 5 mm 01 03 05 02 04 9...
Страница 10: ...8 Fran ais Fran ais 6 mm x4 05 B 6 mm x4 05 A 2 1 aerial flash 2 1 06 07 08 09 02 03 04 01 10...
Страница 26: ...Fran ais...
Страница 33: ...English 7 English 8 7 1 Led SAFE 3 2 4 5 mm 01 03 05 02 04 9...
Страница 34: ...8 English English 6 mm x4 05 B 6 mm x4 05 A 2 1 aerial flash 2 1 06 07 08 09 02 03 04 01 10...
Страница 50: ......
Страница 57: ...Italiano 7 Italiano 8 7 1 Led SAFE 3 2 4 5 mm 01 03 05 02 04 9...
Страница 58: ...8 Italiano Italiano 6 mm x4 05 B 6 mm x4 05 A 2 1 aerial flash 2 1 06 07 08 09 02 03 04 01 10...
Страница 74: ...Fran ais...
Страница 81: ...Polski 7 Polski 8 7 1 Led SAFE 3 2 4 5 mm 01 03 05 02 04 9...
Страница 82: ...8 Polski Polski 6 mm x4 05 B 6 mm x4 05 A 2 1 aerial flash 2 1 06 07 08 09 02 03 04 01 10...