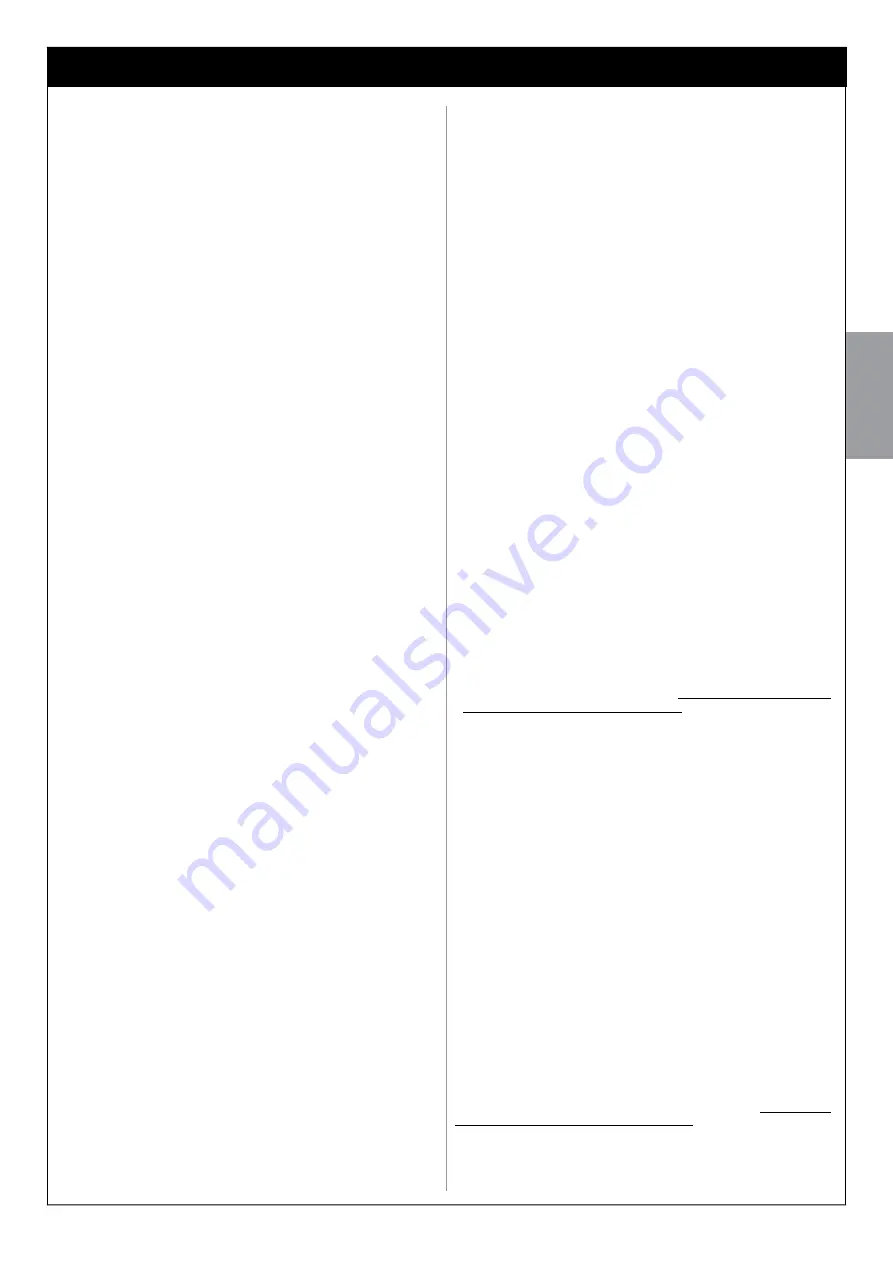
English –
3
English
KNOWLEDGE OF THE PRODUCT AND PREPARATION FOR INSTALLATION
––– STEP 4 –––
4.1 - PRE-INSTALLATION WORKS
4.1.1 - Establish the position of devices in the system
With reference to
fig. 1
and
fig. 2
, locate the approximate position for
installing each device in the system.
Fig. 1
shows a system built with this
product plus other optional accessories. The various elements are posi-
tioned according to a standard and usual layout. The components are:
a
- 1 CLB207 control unit
b
- 1 FL200 flashing indicator with built-in antenna
c
- 1 pair of PH200 photocells (made up of a TX and an RX)
d
- 2 end stops
e
- 2 IN100 electromechanical gearmotors
WARNING! - Some of these devices are optional and may not be
present in this package (see the Nice Home product catalogue).
WARNINGS:
The fixed control devices must be positioned:
- in sight of the automation;
-
away from its moving parts;
- at a height of at least 1.5 m from the ground,
- not accessible by the public.
4.1.2 - Establish the position of all connection cables
Refer to the instructions in paragraph 4.2 to establish the layout of the
raceways for electric cable ducting.
4.1.3 - Ensure all equipment and materials for work are available
Before starting work, ensure that you have all equipment and materials
required to complete the work. Ensure that all items are in good condition
and comply with local safety standards.
4.1.4 - Completing the set-up work
Prepare the area for installation of the devices, completing all preliminary
work, such as:
- excavation of routes for the cable ducting for the electrical cables (alter-
natively, external raceways may be used);
- installation of the cable ducting and their attachment in concrete;
- sizing of all electrical cables to the desired length (see section 4.2) and
their passage in the ducting.
Warning! - At this stage do not imple-
ment any type of electrical connection.
Warnings
:
• Ducting and raceways are used to protect the electrical cables from
damage due to accidental impacts.
• When laying the ducting, also take into account that due to possible
deposits of water in the routing ducts, the ducting might create con-
densation in the control unit, with consequent damage to the electronic
circuits.
• Place the ends of the ducting in the vicinity of the points provided for
affixing the devices.
4.2 - PREPARING ELECTRICAL CABLES
To prepare all connection cables, proceed as follows.
a)
- Observe
fig. 2
to understand how the various devices should be con-
nected to the control unit and the terminals to be used for each con-
nection.
Important
- Only devices which support “ECSbus” technol-
ogy can be connected to the “ECSbus” terminal.
b)
- Observe
fig. 1
to understand how to position the electrical cables.
Then draw a similar diagram on paper, adapting it to the specific
requirements of your system.
Note
- This diagram will be useful,
both to guide the excavation of the routes for the cable ducting, and
for drawing up a complete list of the cables required.
c)
- Read
Table 2
to determine the type of cables to use; then use the
diagram you just drew and the measurements taken to determine the
length of each individual cable.
Warning! - No cable must exceed
the specific maximum length stated in Table 2.
WARNING
- The “ECSbus” technology allows you to connect multiple
devices together using, between one device and the next, a single “bus”
cable, with two internal electrical conductors. The connection between
the devices can have a “
cascade
”, a “
star
” or a “
mixed
” configuration,
between the first two.
––– STEP 2 –––
2.1 - PRODUCT DESCRIPTION AND INTENDED USE
The device is a control unit designed for handling mechanical actuators
on automation mechanisms in gates for residential use. Section 3.2 lists
the products that can be handled by this equipment.
Any use other than
as specified herein or in environmental conditions other than as
stated in this manual is to be considered improper and is strictly
prohibited!
The control unit comprises a board and incorporated radio receiver which
receives the commands sent by the user via a transmitter. It can memo-
rise up to 256 ECCO5... transmitters (if memorised in “Mode 1”) and up to
6 pairs of PH200 photocells.
Connection of the control unit with the various devices is by means of a
single 2-wire cable (“ECSbus” system). Furthermore, the control unit can
be powered by a fixed electrical mains supply (230 V) or, alternatively, by
the Nice Home SOLEKIT solar power system.
If powered off the mains, it can be fitted with a backup battery (mod.
PR100, optional accessory) which ensures that the automation can exe-
cute a certain number of manoeuvres, during the hours following a loss of
power (electrical black-out).
––– STEP 3 –––
3.1 - CHECK SUITABILITY OF GATE TO BE AUTOMATED
AND THE ENVIRONMENT
• Ensure that the mechanical structure of the gate is suitable for auto-
mation and complies with local standards. For this check, refer to the
information specified on the gate dataplate.
Important
- This product
cannot automate a gate that is not already secure and efficient; moreo-
ver, it cannot resolve defects caused by improper installation of the gate
or from poor maintenance.
• Manually move the gate leaves in the two directions (open/closed) and
make sure that the movement takes place with a constant friction at
every point along its course (there should be no points requiring more
nor less effort).
• If there is an access door in the gate, or within the range of movement
of the gate, make sure that it does not obstruct normal travel and, if
necessary, install an appropriate interlock system.
• Manually bring the door of the gate into any position; then, leave it
closed and make sure that it does not move.
• Ensure that the environment in which the gearmotor is to be installed
has sufficient space to be able to perform the manual manoeuvre of
releasing the gearmotor.
• Make sure that the surfaces selected for installation of the devices are
strong and can provide stable attachment; choose a flat surface for the
photocells that can ensure proper alignment of the torque (Tx and Rx).
• Ensure that all devices to be installed are in a sheltered location and
protected against the risk of accidental knocks.
3.2 - PRODUCT APPLICATION LIMIT
The control unit can operate with the gearmotor listed below, which has
the following weight and door weight and length limitations. Make sure
the gate meets these specifications.
IN100 - maximum length 1.8 m
- maximum weight 100 kg
The shape of the gate and weather conditions (such as strong winds) may
reduce these maximum values; in this case the user must measure the
torque required to move the leafs in the worst conditions and compare
this value with the technical specifications.
- Ensure that all limitations, conditions and warnings in this manual can
be fully observed.
Содержание CLB207
Страница 2: ...Fran ais...
Страница 9: ...Fran ais 7 Fran ais 8 7 1 Led SAFE 3 2 4 5 mm 01 03 05 02 04 9...
Страница 10: ...8 Fran ais Fran ais 6 mm x4 05 B 6 mm x4 05 A 2 1 aerial flash 2 1 06 07 08 09 02 03 04 01 10...
Страница 26: ...Fran ais...
Страница 33: ...English 7 English 8 7 1 Led SAFE 3 2 4 5 mm 01 03 05 02 04 9...
Страница 34: ...8 English English 6 mm x4 05 B 6 mm x4 05 A 2 1 aerial flash 2 1 06 07 08 09 02 03 04 01 10...
Страница 50: ......
Страница 57: ...Italiano 7 Italiano 8 7 1 Led SAFE 3 2 4 5 mm 01 03 05 02 04 9...
Страница 58: ...8 Italiano Italiano 6 mm x4 05 B 6 mm x4 05 A 2 1 aerial flash 2 1 06 07 08 09 02 03 04 01 10...
Страница 74: ...Fran ais...
Страница 81: ...Polski 7 Polski 8 7 1 Led SAFE 3 2 4 5 mm 01 03 05 02 04 9...
Страница 82: ...8 Polski Polski 6 mm x4 05 B 6 mm x4 05 A 2 1 aerial flash 2 1 06 07 08 09 02 03 04 01 10...