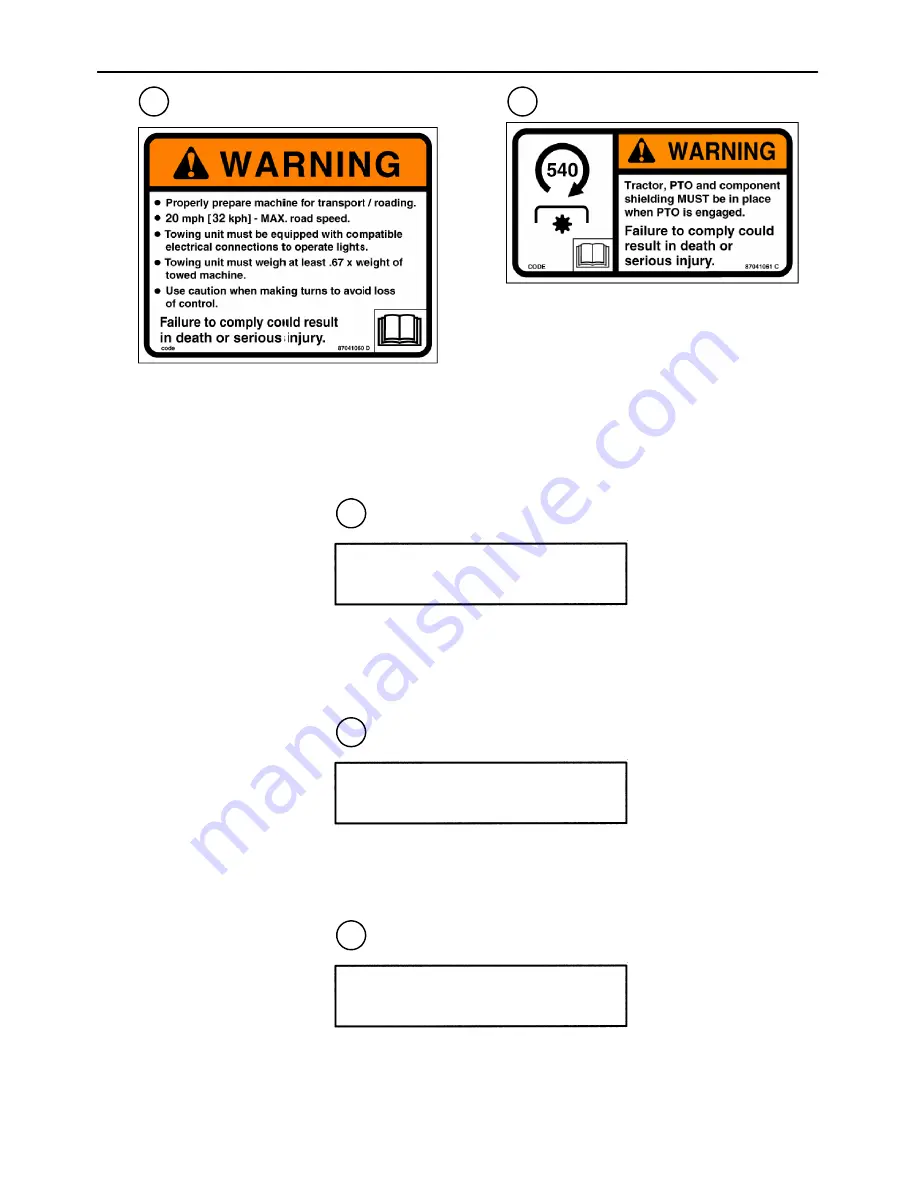
0-8
7
8
Part #87041060
WARNING: Properly prepare machine for
transport. Use caution when towing unit.
Failure to comply could result in death or
serious injury.
Part #87041061
Warning: Shielding must be in place when
PTO is engaged. Failure to comply could
result in death or serous
9
Part #86547782
Reflective Tape, Yellow
10
Part #86547781
Reflective Tape, Red
11
Part #86547783
Reflective Tape, Orange
Содержание Haybine 499
Страница 1: ... 5HSODFHV OO 3UHYLRXV VVXHV ...
Страница 2: ... 1 PHULFD ...
Страница 28: ...SECTION 1 GENERAL INFORMATION 1 18 ...
Страница 50: ...SECTION 2 OPERATION 2 22 ...
Страница 60: ...SECTION 3 LUBRICATION 3 10 ...
Страница 71: ...SECTION 4 MAINTENANCE 4 11 9 Tighten bolts 1 and nuts 2 10004725 1 1 2 12 ...
Страница 110: ...SECTION 4 MAINTENANCE 4 50 ...
Страница 114: ...SECTION 5 TROUBLESHOOTING 5 4 ...
Страница 122: ...SECTION 7 SPECIFICATIONS 7 4 ...
Страница 126: ...7 8 ...
Страница 128: ...7 10 ...