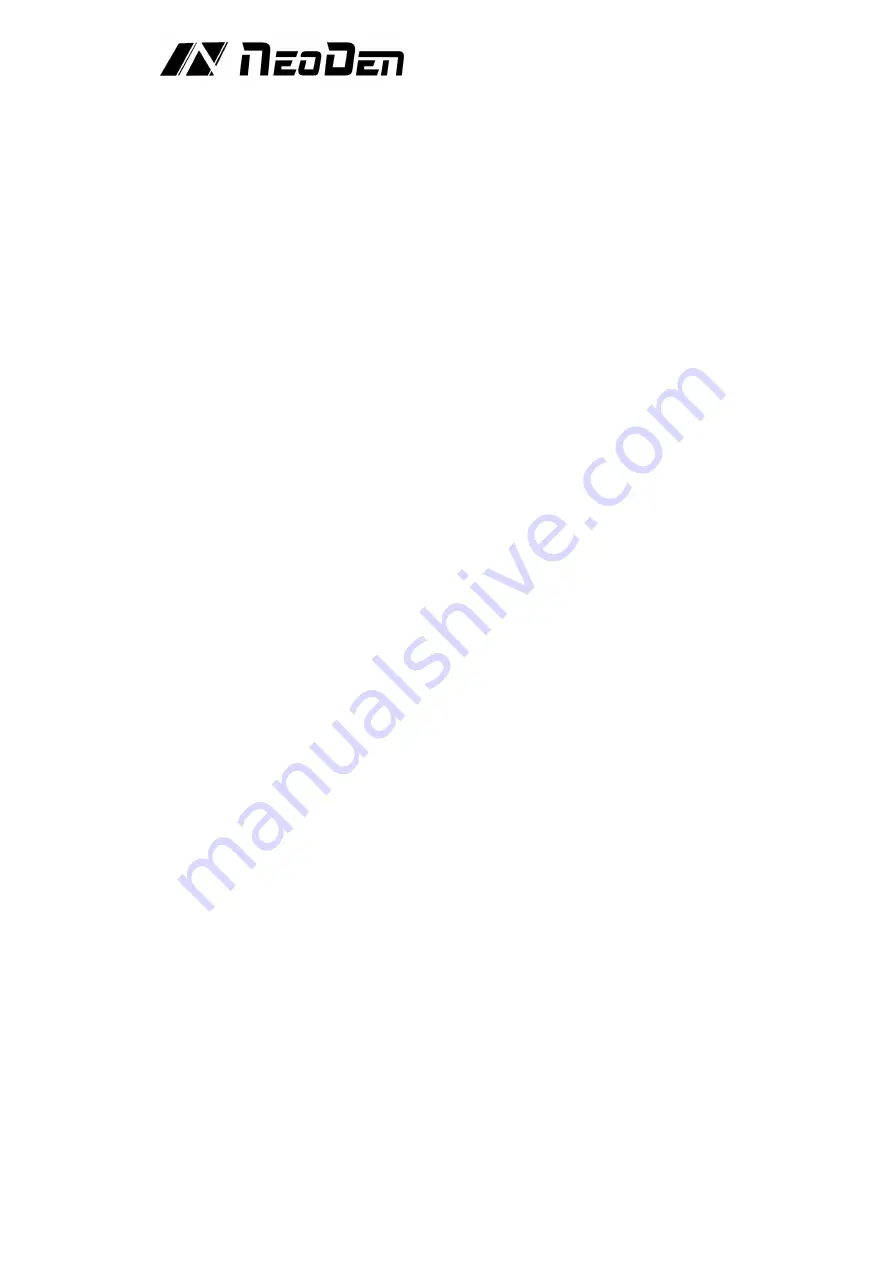
13
component ends and pins. The solder paste softens, collapses and covers the pad,
isolating the pad and component pins from oxygen. When the PCB enters the heat
preservation area, the PCB and components are fully preheated to prevent the
damage of PCB and components caused by the rapidly raise of temperature.When
the PCB enters into the soldering area, the temperature rises rapidly to make the
solder paste melt. The liquid soldering tin enters the cooling area to solidify the
solder joint and complete the reflow soldering. The temperature wave is the key to
ensure the soldering quality. The temperature rise slope and peak temperature of
the actual temperature wave and the solder paste temperature wave should be
basically consistent. Before 160
℃
, the heating rate should be controlled at about
1
℃
/ s. if the heating rate is too fast, on the one hand, the components and PCB
will be heated too fast, which will damage the components and easily cause PCB
deformation; on the other hand, the solvent in solder paste will volatilize too
quickly, which will easily splash metal components and produce solder balls. The
peak temperature is generally set at 20
℃
- 40
℃
higher than the melting
temperature of solder, and the reflow time is 10s-60s. If the peak temperature is
low or the reflow time is short, the soldering will not be sufficient, and in serious
cases, the solder paste will not melt; if the peak value is too high or the reflow time
is long, it will cause metal powder oxidation, affect the soldering quality, and even
damage the components and PCB.
5.2 Setting of temperature wave
Set according to the temperature wave of solder paste and the soldering principle
provided above. Solder paste with different metal content should have different
temperature wave, and the reflow temperature wave should be set according to the
temperature wave provided by the solder paste manufacturer. In addition, the
temperature wave is also related to the density and size of the heated PCB and
components.
An optimized reflow temperature wave is one of the most important factors to
obtain high quality solder joints in printed circuit board (PCB) assembly using
surface mount components. The temperature wave is a function of the temperature
applied on the circuit assembly to time. During the reflow process, it represents the
temperature at a specific point on the PCB to form a wave at any given time.
Several parameters affect the shape of the wave, the most important of which is the
belt speed and the temperature setting of each zone. The belt speed determines the
duration of exposure of the board to the set temperature of each zone. Increasing
the duration allows more time for the circuit assembly to approach the temperature
setting of the zone. The total duration of each zone determines the total processing
time.
The temperature setting of each zone affects the temperature rising speed of PCB,
and high temperature produces a large temperature difference between PCB and
zone temperature. The set temperature of the increase zone allows the board to
reach the given temperature faster. Therefore, it is necessary to make a figure to
determine the PCB temperature wave. Next is the outline of this step to generate
and optimize the graphics.
The following equipment and Auxiliary tools are required before starting the wave
procedure
High precision temperature profiler ( with IN12C), thermocouple (with IN12C),
tools for attaching thermocouple to PCB (mainly high temperature tape) and solder
paste parameter table.
There are several ways to attach thermocouple to PCB. The better way is to use