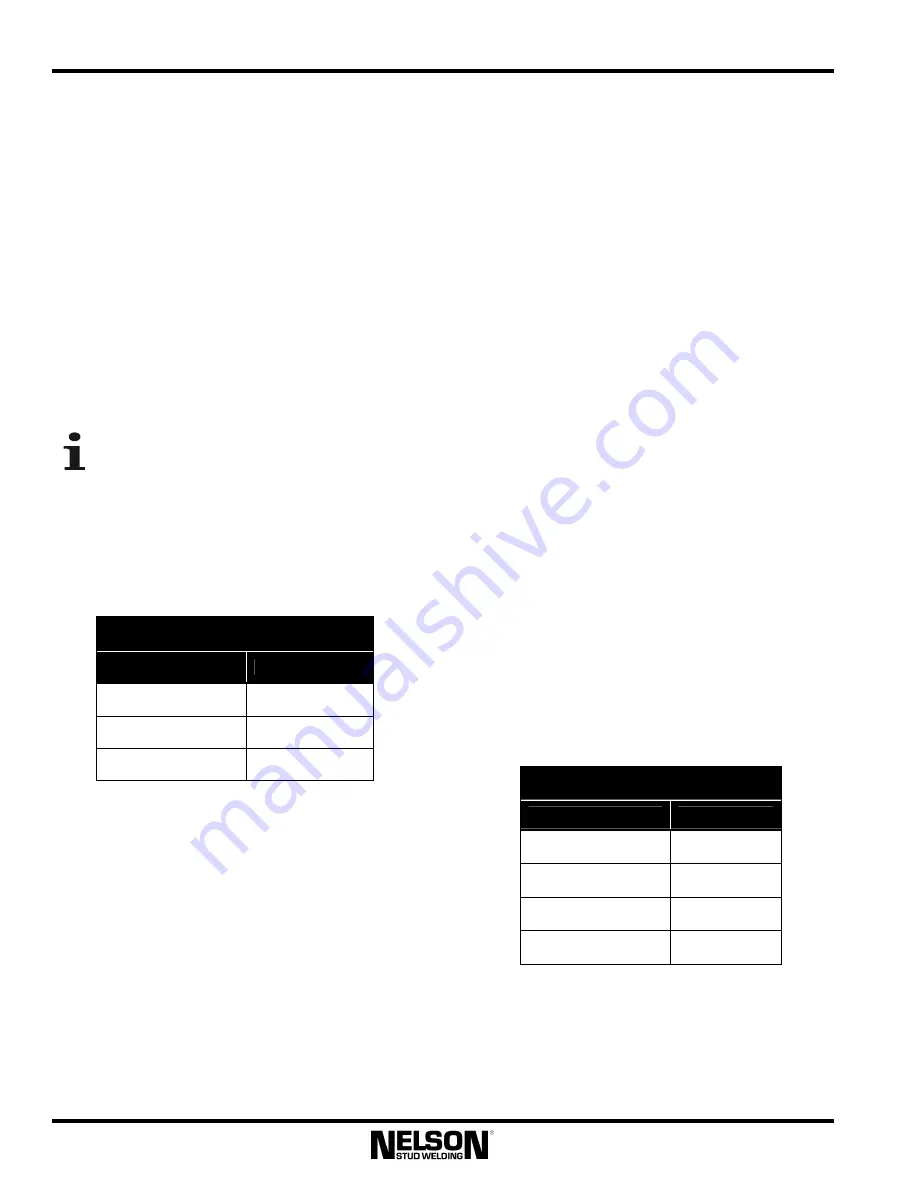
Nelweld Operations and Service Manual
- 20 -
•
Burn through the base material.
In most arc welding processes the weld fillet
metal comes from the addition of filler metal
from a stick electrode or a spool of welding wire.
In stud welding a portion of the stud itself is the
source of the weld metal. The length of the stud
that is melted to develop the flash is called
burn-
off
, and is defined as the difference in length
between a welded stud and its original length.
The length reduction or burn-off is a very good
gauge of weld quality, since the burn-off is
determined by the weld settings of time, current,
lift, and plunge. Proper burn-off also indicates
that there was no bind or hang-up during the
plunge motion of the gun.
The most convenient method of checking
burn-off is to stand an unwelded stud
upside down (load end up) next to a
welded stud to compare the length difference.
After weld height can also be checked with a
sliding carpenter’s level/square tool. The
Stud
Burnoff Length
table shows typical burn-off
length reductions when welding to bare plate of
sufficient thickness.
Stud Burn-Off Lengths
(not including flux load)
Stud Diameter
Length Reduction
3/16” through 1/2”
(5mm through 12mm)
1/8”
(3mm)
5/8” through 7/8”
(16mm through 22mm)
3/16”
(5mm)
1” and over
(25mm and over)
1/4”
(6mm)
2.7.5 Physical Weld Inspection
Two studs should be welded according to
qualified settings during pre-production testing.
Following satisfactory visual inspection, they are
bent 30º or torque tested in the case of threaded
studs. This procedure should also be followed if
there is any change of operator or any change in
equipment, position, settings, etc. Studs that are
bent may be straightened to the original axis.
Studs should not be heated during bending or
straightening without approval by the Engineer of
Record
. Torque testing is done to a proof load
level slightly lower than the nominal yield of the
stud so there is no permanent distortion of the
threads. Torque test proof load requirements are
found in AWS D1.1, D1.5, or D1.6. The test studs
may be used in production.
The stud welding operator is responsible for pre-
production set up and testing. The operator shall
weld two studs to a production weld plate or to a
piece of material similar to the weld plate in
material composition and within 25% of the
production weld plate thickness.
Inspections during production are also the
responsibility of the operator. Pre-production and
production inspection test results should be
recorded and approved by the welding supervisor.
Any
unsatisfactory
pre-production
and/or
production inspections and tests should be
brought to the welding supervisor’s attention and
corrections made, accompanied by additional
tests with fully satisfactory inspection and test
results before proceeding with further welding.
At regular intervals during production welding,
the studs welded after the last testing interval
should have the ceramic ferrules removed and
should be visually inspected. If the visual
inspection shows a full periphery weld flash,
without undercut, and satisfactory after weld
length, welding may continue. If the visual
inspection shows a lack of flash or insufficient
weld burn off, the questionable studs should be
marked and appropriate supervisory personnel
notified.
Minimum Weld Flash Size
Stud Diameter
Weld Flash Size
3/16” through 7/16”
(5mm through 11mm)
3/16”
(5mm)
1/2”
(12mm)
1/4”
(6mm)
5/8” through 7/8”
(16mm through 22mm)
5/16”
(8mm)
1” and over
(25mm and over)
3/8”
(10mm)
In accordance with codes, contract documents or
quality assurance inspection criteria, studs
without a full peripheral flash, but with a
satisfactory after weld length may be bent 15º in
the direction opposite the lack of flash, or
Содержание Nelweld 4000
Страница 58: ...Nelweld Operations and Service Manual 58 7 5 Declaration of Conformity...
Страница 59: ...Nelweld Operations and Service Manual 59 8 0 Diagrams and Parts Lists 8 1 Front Section Not shown...
Страница 61: ...Nelweld Operations and Service Manual 61 8 2 Base and Side Cabinet Section...
Страница 65: ...Nelweld Operations and Service Manual 65 8 4 Rear Cabinet Section...
Страница 67: ...Nelweld Operations and Service Manual 67 8 5 Wiring Diagram...