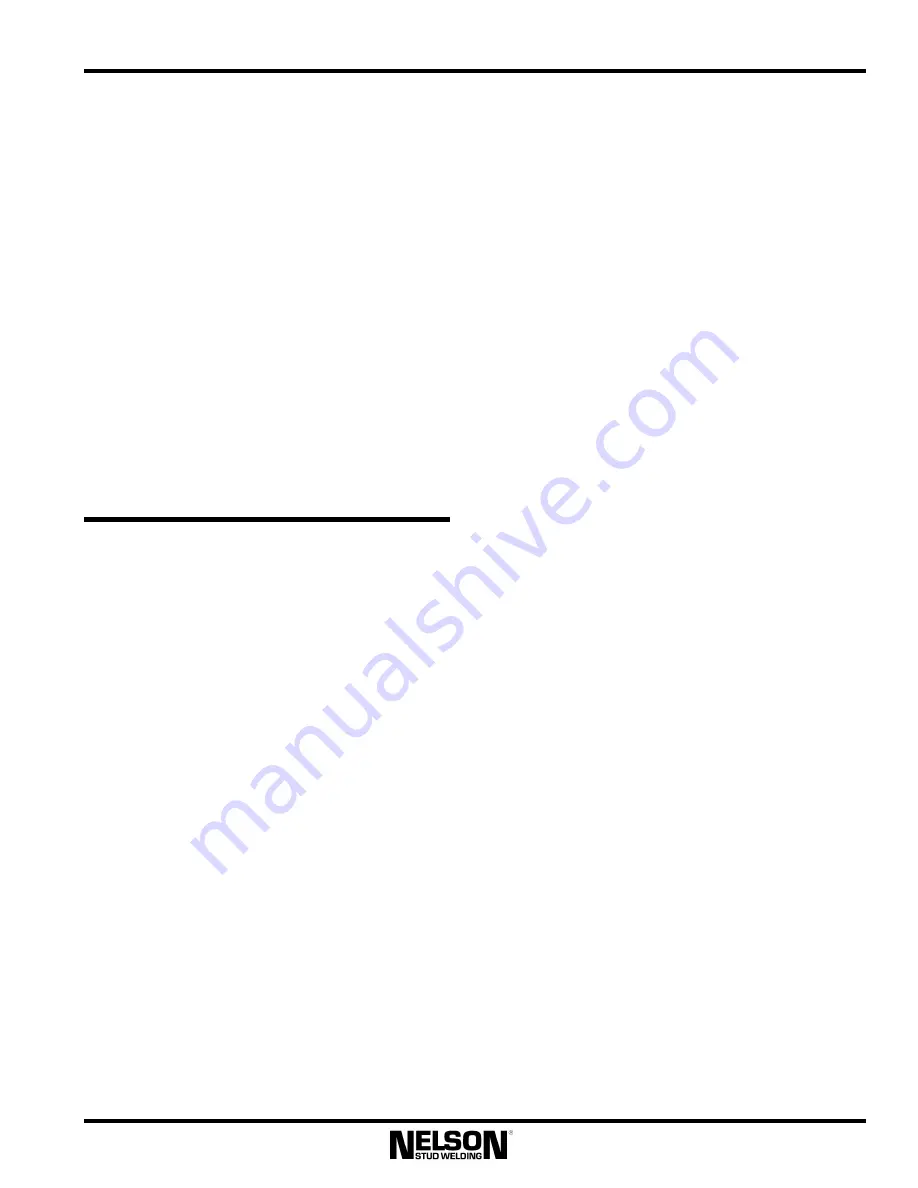
Nelweld Operations and Service Manual
- 15 -
The
Weld
Settings
table
specifies
the
recommended weld settings. It should be noted
that these settings are only
suggested
starting
points for obtaining a final set up which is then
verified
by visual inspection, after weld
measurement and physical testing. Other factors
such as grounding of the welding system, base
plate composition, ambient temperature, cable
connections, etc. can influence the weld settings.
Stud manufacturers are required to qualify their
studs’ weld base diameters by tests with currents
at plus or minus 10% from optimum (except in
the case of 7/8”and 1” diameters which are plus
or minus 5%), an indication of the variability that
can occur under actual welding conditions. This
quantification helps ensure that the settings listed
above are a good starting point for most welding
applications.
2.7 Stud Welding Practice
2.7.1 General Guidelines
In stud welding as in other welding and
fabricating methods, there are some general
guidelines to consider when determining the
basics of good practice. Among these are:
Weld Plate Thickness:
A plate thickness that is at
least 1/3 of the stud shank diameter will develop
the full steel tensile and shear capacity of the
stud. The weld base plate will, however, undergo
distortion and bending in many cases, leading to a
change in the stud diameter/plate thickness ratio,
when high loads are applied which are not
satisfactory in many cases.
Weld Plate Cleanliness:
The most applicable rule
is that the area where the stud is to be welded
(weld spot) should be as clean as possible to
eliminate welding problems. The spot where the
ground clamp(s) are to be fastened should also be
cleaned on both sides of the plate so a good
current path is established. Normally, a light rust
or light mill scale is not detrimental. Heavy mill
scale or heavy, flaky rust should be removed as
should any deleterious coating such as heavy oil,
paint, galvanizing, grease, moisture etc. While
zinc galvanizing is electrically conductive, studs
should not be welded to a galvanized plate. Zinc
is a weld contaminant and will cause brittle
welds. Weld and ground spots can be cleaned
very quickly by spot grinding with an abrasive
wheel, wire brush or wheel, drill bur, end mill, or
other similar device. It should be noted that solid
grinding wheels or abrasive discs do not remove
zinc plating very well, but usually just result in
the grinding disc or wheel filling with zinc and
then merely spreading the zinc plating around
making the weld spot look shiny and clean but
allowing enough zinc to remain in the weld area
to still cause welding problems. Use of open pore
abrasive disc or a grinding wheel is preferable
when removing galvanizing.
Galvanizing:
Galvanizing should be done after
the base plate has been stud welded. If
galvanizing is done prior to welding, the effects
of hydrogen embrittlement should be considered
when hot dip galvanizing is used. Hydrogen
embrittlement can have several points of origin
that can cause serious brittleness in the weld or in
the stud shank when studs are bent with a very
tight bend diameter.
Other causes are improper pickling of the finished
weld plate either by pickling too long or not
rinsing thoroughly after pickling, plating too long
or at too high a temperature. It can also occur
when the stud is very high strength in comparison
with the base plate material strength.
Edge Distance:
Studs welded near an edge should
be placed no closer to a free edge of a base plate
than the diameter of the stud plus 1/8” to the edge
of the stud base. This distance should preferably
be not less than 1” to 1-1/2 “ from a free edge or
edges. Special ferrules should be used in
situations where studs are welded closer than this
requirement or on the edge of a plate or bar.
Grounding/Arc Blow:
Edge distance (above) and
ground placement can influence weld quality due
to arc blow. That is, the welding arc is
electromagnetically deflected away from the
grounding point or toward the larger mass of the
base plate configuration being welded.
Содержание Nelweld 4000
Страница 58: ...Nelweld Operations and Service Manual 58 7 5 Declaration of Conformity...
Страница 59: ...Nelweld Operations and Service Manual 59 8 0 Diagrams and Parts Lists 8 1 Front Section Not shown...
Страница 61: ...Nelweld Operations and Service Manual 61 8 2 Base and Side Cabinet Section...
Страница 65: ...Nelweld Operations and Service Manual 65 8 4 Rear Cabinet Section...
Страница 67: ...Nelweld Operations and Service Manual 67 8 5 Wiring Diagram...