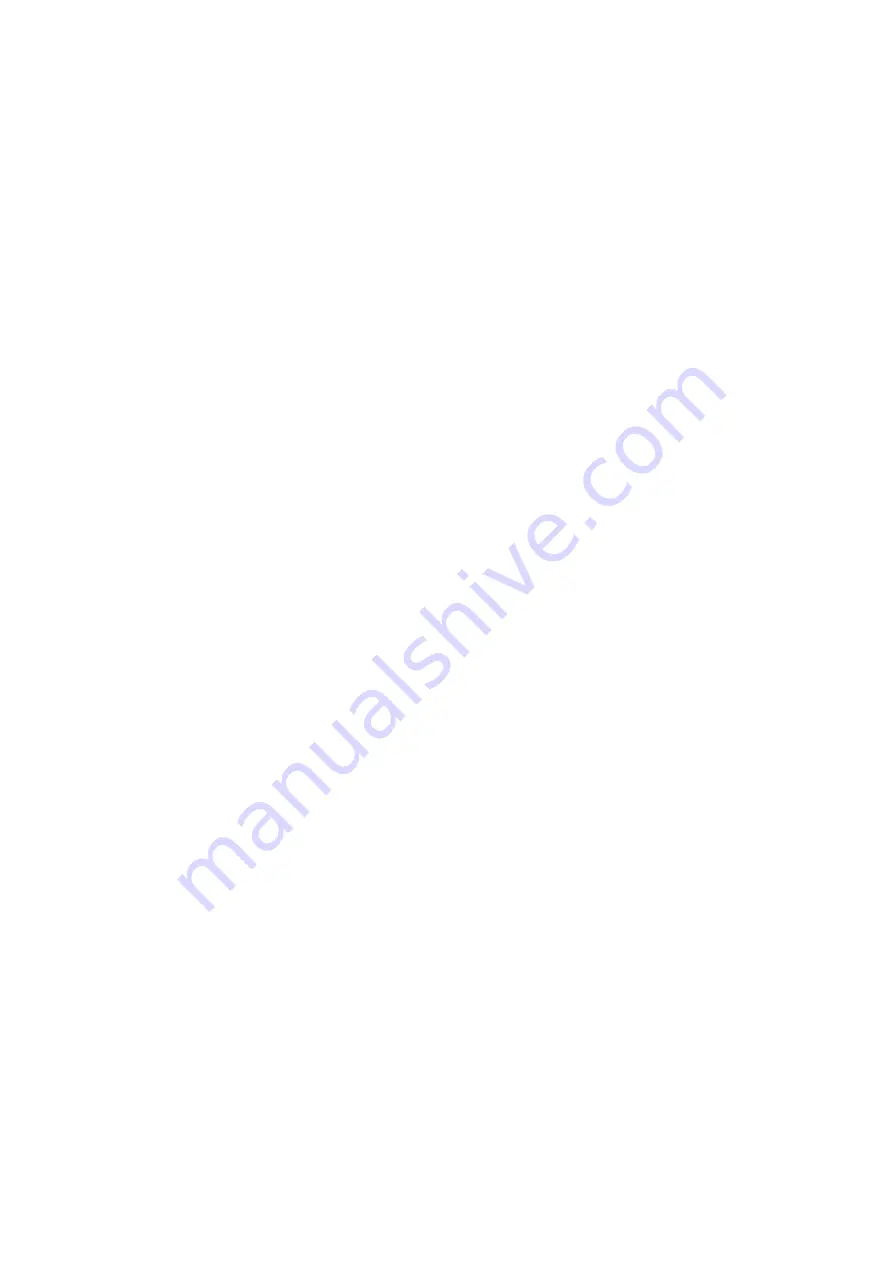
P a g e
13 | 61
2.1 Standard machine version
2.1.1 Lid and working group
The machine housing is divided into two standard parts; see Figure 1. They consist of a
movable lid (pos. 1-2) and a fixed working group (pos. 1-1). Both parts are made of stainless
steel (ČSN 17 240).
The working space is located inside the lid and working group.
The working group is divided by removable grids, refer to Figure 1 (pos. 1-71, 1-72). Above the
grids there is a working space in which the technological processes of washing of parts take
place. Under the grids there is a wash liquid tank with a filter, refer to Section 2.1.2.
The lid is suspended on two hinges, see Fig. 3 (position 3-1) allowing its complete closure. Both
of the hinges are secured with locking rings against being pulled out of the eyelets (pos. 3-92.1).
The operator controls the opening and closing of the lid manually. The lid is secured against
spontaneous opening by means of a lock, so-called front closure lever; see in Fig. 1 (pos. 101).
A handle is screwed to the lid to facilitate its handling (pos. 1-102). Damping gas struts are
installed between the lid and the working group to alleviate the weight of the lid, see in Fig. 2, 4
(pos. 2-102). The strut hinges are anchored to the pins welded to the wall of the working group
and of the lid.
Sealing between the working group and the lid is achieved using a flexible lid seal put over the
peripheral edge of the working group; see in Fig. 5 (pos. 3a-62).
2.1.2 Oil skimmer
When parts containing residual oil are washed, a floating oil film forms on the wash liquid
surface. It is removed mechanically using additional machine equipment, so called oil skimmer,
see in Fig. 2a. The unit consists of an oil skimming belt (position 2a-101) suspended vertically
on a drive roller (pos. 2a-7) driven by an electrical motor. A balance roller is suspended on the
lower end of the belt (pos. 2a-5). Droplets of oil are carried by the belt in between teflon blades
(pos. 2a-6). When wiped off the belt, the droplets flow through a trough into a pipe with screw
fitting (pos. 2a-4), into which an oil discharge valve is screwed (pos. 2a-51).
Torque from the transmission (pos. 2a-41, M1) is transmitted on the drive roller using a shaft
(pos. 2a-2) mounted in a bearing housing (pos. 2a-1). The drive shaft is inserted in the bushing
in the transmission and secured against shifting by a screw with a washer (pos. 2a-93.1 and 2a-
93.2). On the other side, it is secured by a locking ring (pos. 2a-91.1) inserted in the groove in
the shaft. The shaft passes through a shaft sealing ring (pos. 4e-61) preventing liquid
penetration into the inner parts of the bushing. The end of the shaft is provided with the drive
roller (pos. 2a-7).
The left side wall of the working group contains a cut-out to which the oil skimmer unit (pos. 2a-
3) is fixed by means of screws and nuts (pos. 2a-94.1÷2a-94.3). It is sealed by a rubber seal
(pos. 2a-62) to prevent leaking of wash liquid from the work space of the working group. The
flange with the transmission (pos. 2a-1) is mounted on the inside using four screws with
washers (pos. 2a-95.1 ÷ 2a-95.3).
The internal section of the oil skimmer unit is covered (pos. 2a-71).
2.1.3 Basket and its drive
Washing of parts proper takes place after they are inserted in the washing basket, see in Fig.
2b, 2c (pos. 2b-5). The basket is formed by a wire structure with a reinforced bottom. The centre
of the basket is formed by a tube slid on the so-called bearing pivot, see in Figure 2c (pos. 2c-
1). The upper part of the pivot passes through a plastic and metal washer (pos. 2c-91.1 and 92-
1): A cotter pin (pos. 2c-93.1) is inserted in a hole in the pivot and secured, holding the basket
on the housing.
The bearing pivot is inserted in the tube connected to the support by welding, see in Fig. 2c
(pos. 2c-1). A lid with the central tube pin is welded from the top. Attached to the tube are axial
Содержание ADS800
Страница 5: ...P a g e 5 61 Fig 1 Front view of the machine 1 102 1 101 1 2 1 71 1 72 1 1...
Страница 6: ...P a g e 6 61 Fig 2 Left view of the machine SQ1 HS1 2 102 2 101 RT1 ST1 T1 See Fig 2a See Fig 2b...
Страница 9: ...P a g e 9 61 Fig 2c detailed view of housing 2c 91 1 2c 3 2c 93 1 2c 2 2c 92 1 2b 4 2c 1...
Страница 10: ...P a g e 10 61 Fig 3 Rear view of the machine 3 1 3 91 1 See Fig 3a Name plate 3 2 3 102 3a 1...
Страница 12: ...P a g e 12 61 Fig 4 Right view of the machine 2 102 4 103 4 102 4 51 4 1 4 61 See Fig 7 4 101 4 91 1 4 91 2...
Страница 18: ...P a g e 18 61 Fig 5 Basic dimensions of 001 ADS SFM800...
Страница 32: ...P a g e 32 61...
Страница 58: ...P a g e 58 61 10 1 Description of electrical functions and a set of wiring diagrams separate annex...
Страница 61: ...P a g e 61 61 Annex 10 4 Machine operation records Date Completed works on the machine Name and signature...