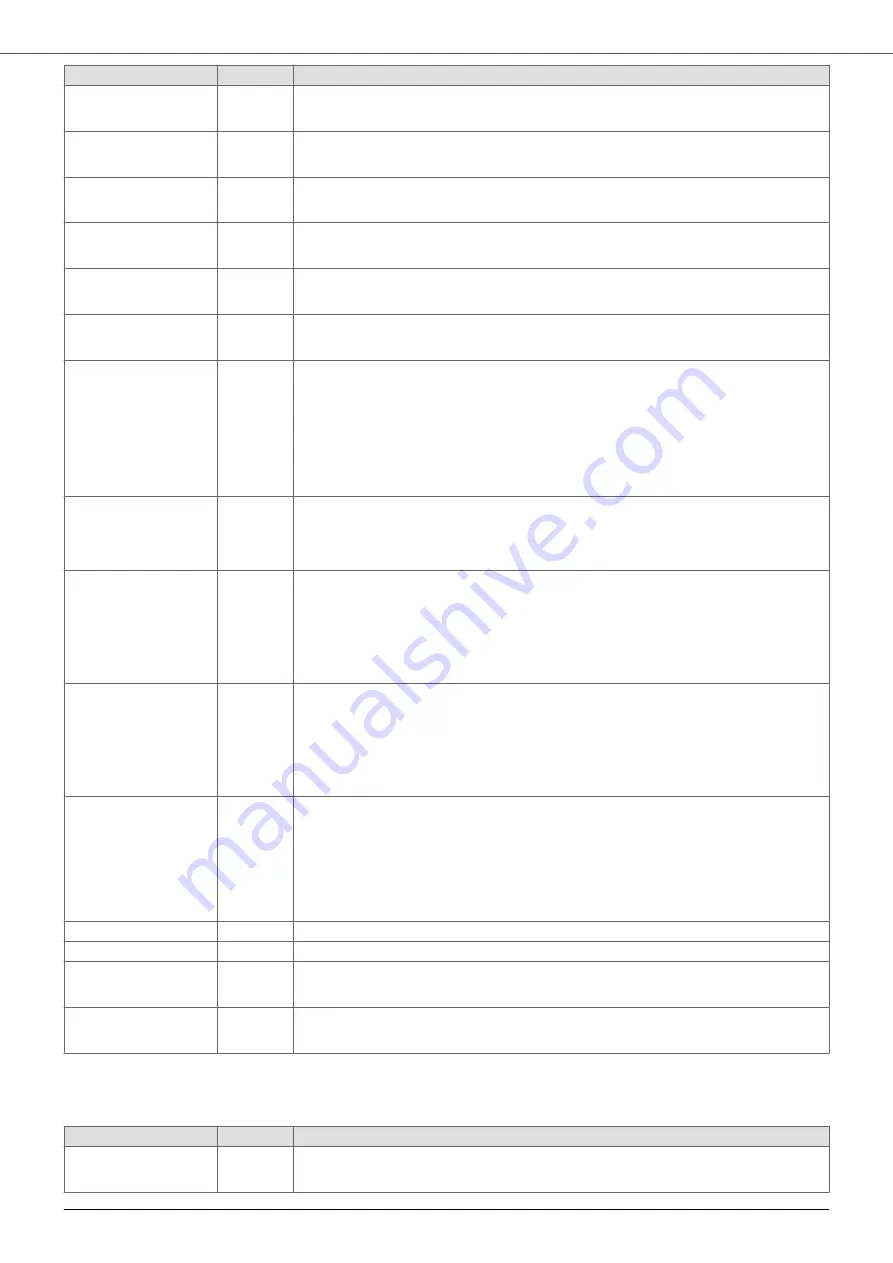
Parameter
Default
Description
Full scale sensor
p = XXX.X [bar]
16
Full scale of the sensor.
Min value sensor
p = XXX.X [bar]
0
Minimum sensor value.
Offset input1
XX.X [%]
20%
Zero correction for analog input 1 (4-20 mA).
(20 mA x 20% = 4 mA).
Offset input2
XX.X [%]
20%
Zero correction for analog input 2 (4-20 mA).
(20 mA x 20% = 4 mA).
Offset input3
XX.X [%]
20%
0%
Zero correction for analog input 3.
0-10 V : 10V x 0% = 0 V
Offset input4
XX.X [%]
0%
Zero correction for analog input 4.
0-10 V : 10V x 0% = 0 V
AN1, AN2 function
XXXXXXXX
Inde-
pendent
Operating logic of analog inputs AN1, AN2:
• Independent. The active sensor is relative to analog input 1, while the sensor connected to analog
input 2 serves as an auxiliary in case of failure of the sensor or of analog input 1.
• Selectable. The active sensor may be selected via digital input 3.
• Difference 1-2. The digital difference in absolute value is performed between the measurements of
analog input 1 and analog input 2.
• Higher value. The maximum value between the measurements of the two sensors is considered.
• Lower value. The minimum value between the measurements of the two sensors is considered.
Digital input1
N.O./N.C.
N.O.
If N.O.(Normally Open) is selected, the device will continue to operate the motor if digital input 1 is
open. Conversely, it will stop the motor if digital input 1 is closed.
If N.C. (Normally Closed) is selected, the device will continue to operate the motor if digital input 1 is
closed. Conversely, it will stop the motor if digital input 1 is open.
Digital input2
N.O./N.C.
N.O.
If N.O.(Normally Open) is selected, the device will continue to operate the motor if digital input 2 is
open. Conversely, it will stop the motor if digital input 2 is closed.
If N.C. (Normally Closed) is selected, the device will continue to operate the motor if digital input 2 is
closed. Conversely, it will stop the motor if digital input 2 is open.
Digital input 2 is also used to select set value 1 or set value 2 in the control mode Constant value 2
set or to select working frequency 1 or 2 in the control mode Fix speed 2 values.
Digital input3
N.O./N.C.
N.O.
If N.O.(Normally Open) is selected, the device will continue to operate the motor if digital input 3 is
open. Conversely, it will stop the motor if digital input 3 is closed.
If N.C. (Normally Closed) is selected, the device will continue to operate the motor if digital input 3 is
closed. Conversely, it will stop the motor if digital input 3 is open.
Digital input 3 is also used to select sensor 1 or sensor 2 when the parameter AN1, AN2 function is
set to Selectable.
Digital input4
N.O./N.C.
N.O.
If N.O.(Normally Open) is selected, the device will continue to operate the motor if digital input 4 is
open. Conversely, it will stop the motor if digital input 4 is closed.
If N.C.(Normally Closed) is selected, the device will continue to operate the motor if digital input 4 is
closed. Conversely, it will stop the motor if digital input 4 is open.
Digital input 4 is also used to select the main or auxiliary control mode in case they are different.
Digital input 4 also serves as alarm reset.
Man reset In Dig1
OFF
Enabling or disabling the manual reset of the digital input.
Man reset In Dig2
OFF
Enabling or disabling the manual reset of the digital input.
Dig. input 2/3 delay
t = XX [s]
1
Delay of digital inputs 2 and 3.
Digital inputs 1 and 4 have a fixed delay of 1 second.
Change password1
Press ENT
By pressing the ENT key it is possible to change the installer level password (level 1) (default 001).
9.10. Connectivity parameters
Parameter
Default
Description
MODBUS address
XXX
1
MODBUS address from 1 to 247
MIDA
38
Содержание MIDA 203
Страница 1: ...MIDA Installation use and maintenance manual V 6 0 24 04 2022 EN ...
Страница 17: ...On board motor installation for size 1 devices 63 63 73 73 5 5 65 65 60 4 5 U V W P E 1 2 3 4 MIDA 17 ...
Страница 55: ......
Страница 56: ......