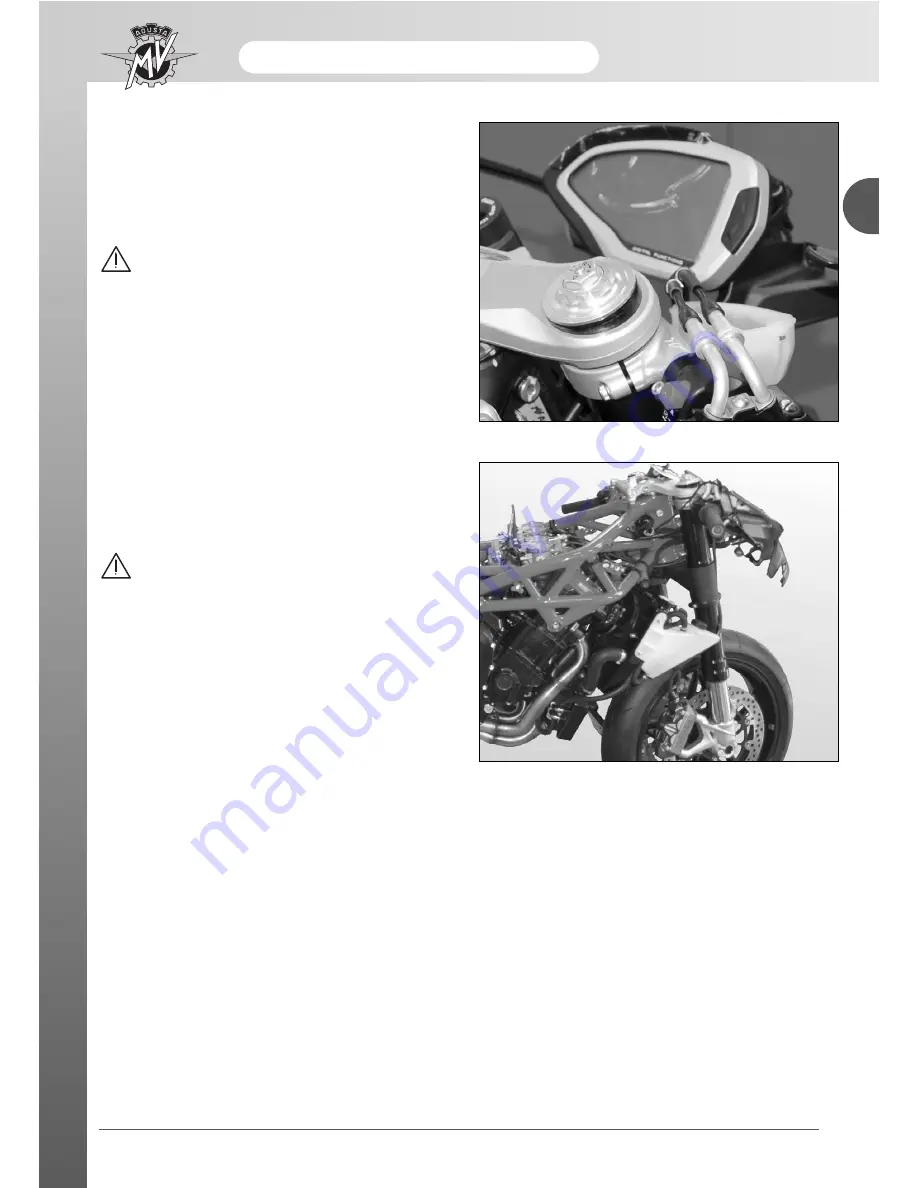
Maintenance
- 45 -
B
Maintenance
Before completing the operation, clean and wash accu-
rately with alcohol the three components of the fluid
chamber cover and blow to dry them.
Clean the edge of the fluid chamber with a clean cloth.
Close the fluid chamber with the two relative screws.
Imperfect cleaning of these parts could
cause the discharge of small quantities of
brake fluid during riding. Brake fluid has
strong corrosive properties.
Check eventual leaks and blow-bys of brake and clutch
fluid on the unions and tubing.
If any breakages are seen, substitute the damaged
parts as described in chapter H “Brakes”.
Brake fluid leakages are dangerous and
immediately discolour painted surfaces.
Before riding, check the tubes and joints of
the brakes for damage and signs of leaks.
Содержание F4 1000 S
Страница 1: ......
Страница 3: ...Motorcycle workshop manual MV AGUSTA F4 1000...
Страница 6: ......
Страница 7: ...1 General description A SECTION A Revision 0...
Страница 16: ...10 General description A...
Страница 17: ...B 1 Maintenance SECTION B Revision 1...
Страница 49: ...Maintenance 33 B Maintenance FUEL PUMP ASSEMBLY...
Страница 99: ...Maintenance 83 B Turn the holding device counter clockwise Remove the bulb Disconnect the connector...
Страница 107: ...1 Bodywork C SECTION C Revision 0...
Страница 114: ...8 Bodywork C TAIL UNIT...
Страница 117: ...C Bodywork 11 Remove the side fairing toward the outside taking care of the rear pin anchored in the support brackets...
Страница 118: ...12 Bodywork C FUEL TANK...
Страница 126: ...AIR INTAKE SYSTEM 20 Bodywork C...
Страница 131: ...HEAT SHIELD Bodywork 25 C...
Страница 134: ...28 Bodywork C MUDGUARD CENTRAL SPOILER RADIATOR PROTECTION Right side Left side...
Страница 137: ...Air intake injection system 1 D SECTION D Revision 1...
Страница 156: ...20 Air intake injection system D...
Страница 157: ...Electrical system 1 E SECTION E Revision 1...
Страница 161: ...5 Electrical system E 5A 5C 5B ELECTRICAL DIAGRAM F4 1000...
Страница 204: ...48 Electrical system E...
Страница 205: ...1 F Suspension and wheels SECTION F Revision 0...
Страница 262: ...Suspension and wheels F 58 Utilising a press fit the bearings and the roller bearing units see figure...
Страница 285: ...Frame 1 G SECTION G Revision 1...
Страница 318: ...34 Frame G...
Страница 321: ...Frame 37 G Before proceeding with frame reassembly replace the previously removed electrical wiring and components...
Страница 324: ...40 Frame G...
Страница 347: ...H 1 Brakes SECTION H Revision 0...
Страница 372: ...26 Brakes H...
Страница 373: ...Cooling system SECTION L Revision 0 L 1...
Страница 401: ...Special tools 1 M SECTION M Revision 1...
Страница 404: ...Special tools M 4...
Страница 406: ...Special tools M 6...
Страница 408: ...Special tools M 8...
Страница 410: ...Special tools M 10...
Страница 412: ...Special tools M 12...
Страница 413: ...1 Tightening torques N SECTION N Revision 1...
Страница 414: ...2 Tightening torques N...
Страница 415: ...Tightening torques 3 N...
Страница 416: ...4 Tightening torques N...
Страница 417: ...Diagnostic 1 O SECTION O Revision 0...
Страница 423: ...Analytical index 1 P SECTION P Revision 1...
Страница 427: ......
Страница 428: ......