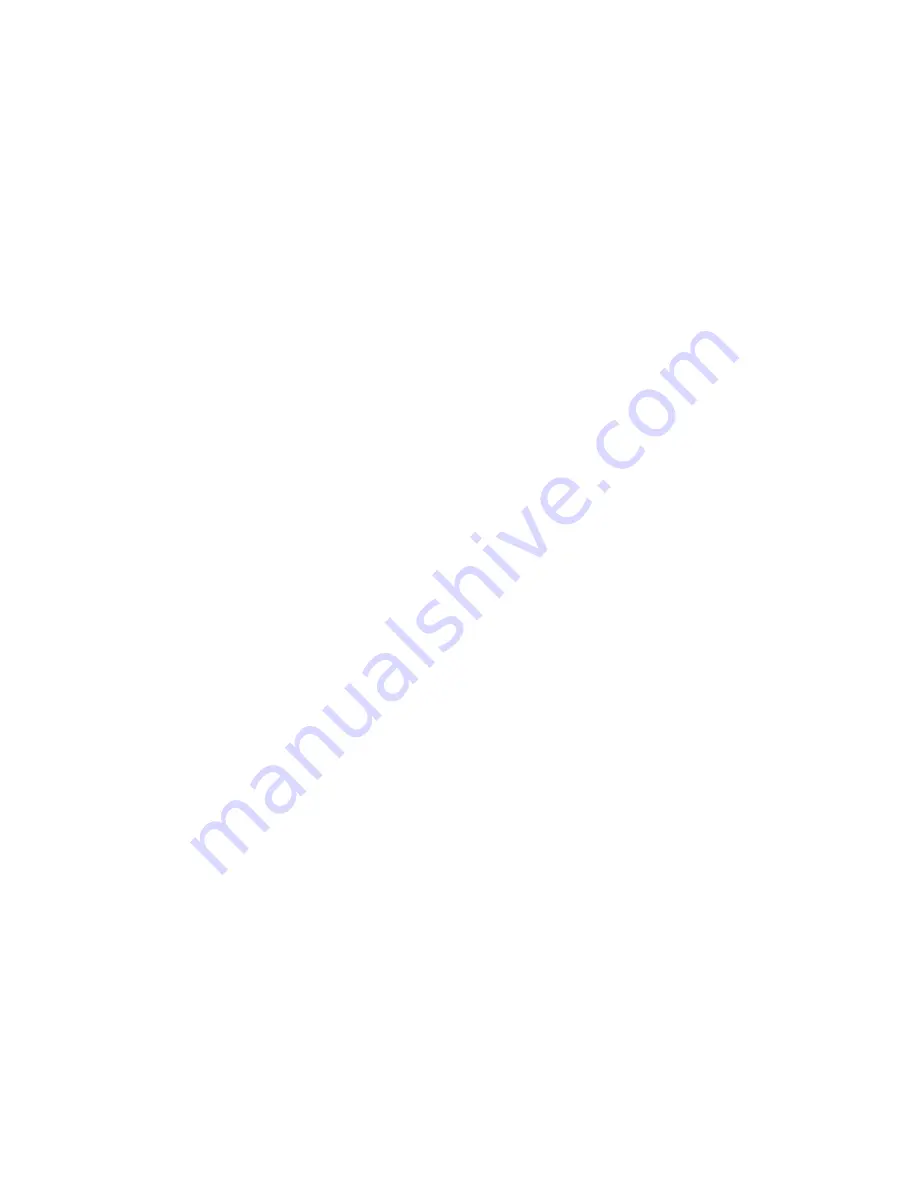
6.50
Removing the Valves and Seats
a)
Using the MSI 2” hex cover wrench (MSI Wrench FEC0024) and a 10 lb. hammer, remove the
suction covers and discharge covers from the fluid cylinder.
b)
Turn the suction valve stop until it stops approximately 90 degrees and remove the valve stops
from the fluid cylinder along with the valve springs underneath them.
c)
Remove the valve from the Fluid End. Follow the valve manufacturer’s recommendation of
removing the insert from the valve.
d)
Remove the discharge valve springs and discharge valves from the fluid cylinder.
e)
Using an MSI seat puller assembly (FEC0113,-114), remove each of the discharge valve seats
and suction valve seats.
f)
The tapered valve seat bore in the fluid cylinder must be thoroughly cleaned and lightly hand
polished with 220 to 240 grit Emery cloth prior to installing new valve seats.
g)
Always install a new o-ring seal when reinstalling a valve seat. Do not use any grease, sealer,
etc.-the valve seat must be installed dry. Upon installing the valve seat hand tight, install the
valve in the seat and using a heavy steel bar with Teflon or wood pad, hammer the valve seat
into the taper.
h)
When reinstalling the valves, do not mix one manufacturer’s valve with another manufacturer’s
valve seat. Likewise, do not mix one manufacturer’s valve insert with another’s valve.
i)
When reinstalling the suction valve stop, make certain it is turned perpendicular to the plunger
and securely seated in the groove in the cylinder.
j)
Before reinstalling the discharge and suction covers, remove the seals from each, clean the
covers thoroughly, and install new seals in the same direction that the old ones came off. Each
cover bore in the fluid cylinder must be cleaned thoroughly and lightly hand polished with 220
to 240 grit Emery cloth prior to cover installation.
k)
Upon installing the threaded suction and discharge covers with a coating of oil or very light
grease, tighten them securely with the 2” hex cover wrench and a 10 lb. hammer.
6.60
Removing Discharge Flanges
a)
Using a 1 5/8” wrench, remove the four 1” nuts from each of the two discharge flanges.
b)
Remove each discharge flange from the fluid cylinder. Remove the fluid seals from both the
inlet side and outlet side of each discharge flange. Closely inspect each discharge flange for
internal erosion and corrosion. Inspect the discharge flange threads for wear and damage. The
discharge flange seal surfaces should be thoroughly cleaned and lightly hand polished with a
220 and 240 grit Emery cloth prior to reinstallation.
c)
Inspect the fluid cylinder discharge flange bores for erosion and corrosion. Thoroughly clean
and lightly hand polish each bore with a 220 to 240-grit Emery cloth prior to reinstalling the
discharge flanges.
d)
Using a new fluid seals and a coating of light oil. Install seals into Fluid End bores lip end first.
Carefully install the Discharge Connection so as not to damage the seal. Reinstall the four 1”
hex nuts on each flange and evenly tighten them to the proper torque (Appendix 10.20).
6.70
Removing the Suction Manifold
a)
Using a 1-1/8” wrench, remove the ¾” cap screws which secure the suction manifold to the
fluid cylinder, and drop the suction manifold away from the fluid cylinder.
Содержание QI-1000
Страница 7: ...1 20 Drawings Pump Assembly Overall Dimensions All Plunger Sizes TI 600 TRIPLEX...
Страница 8: ...QI 1000 QUINTUPLEX...
Страница 9: ...1 30 Dual Pump Assembly Overall Dimensions 1 30 1 600 HP Dual Pump Assembly Overall Dimensions...
Страница 10: ...1 30 2 1000 HP Dual Pump Assembly Overall Dimensions...
Страница 11: ...1 50 Drawings Gear Reducer Installation Positions 1 50 1 Gear Reducer Position Left Hand...
Страница 12: ...1 50 2 Gear Reducer Position Right Hand...
Страница 22: ...4 6 Lubrication Attachment Points See images below showing lubrication inlet and outlet locations...
Страница 36: ......
Страница 39: ...5 50 Power Frame Crank Rotation NOTE Crank Rotation can either be clockwise or counterclockwise...
Страница 43: ...Fluid End Assembly 3 25 4 50 continued...