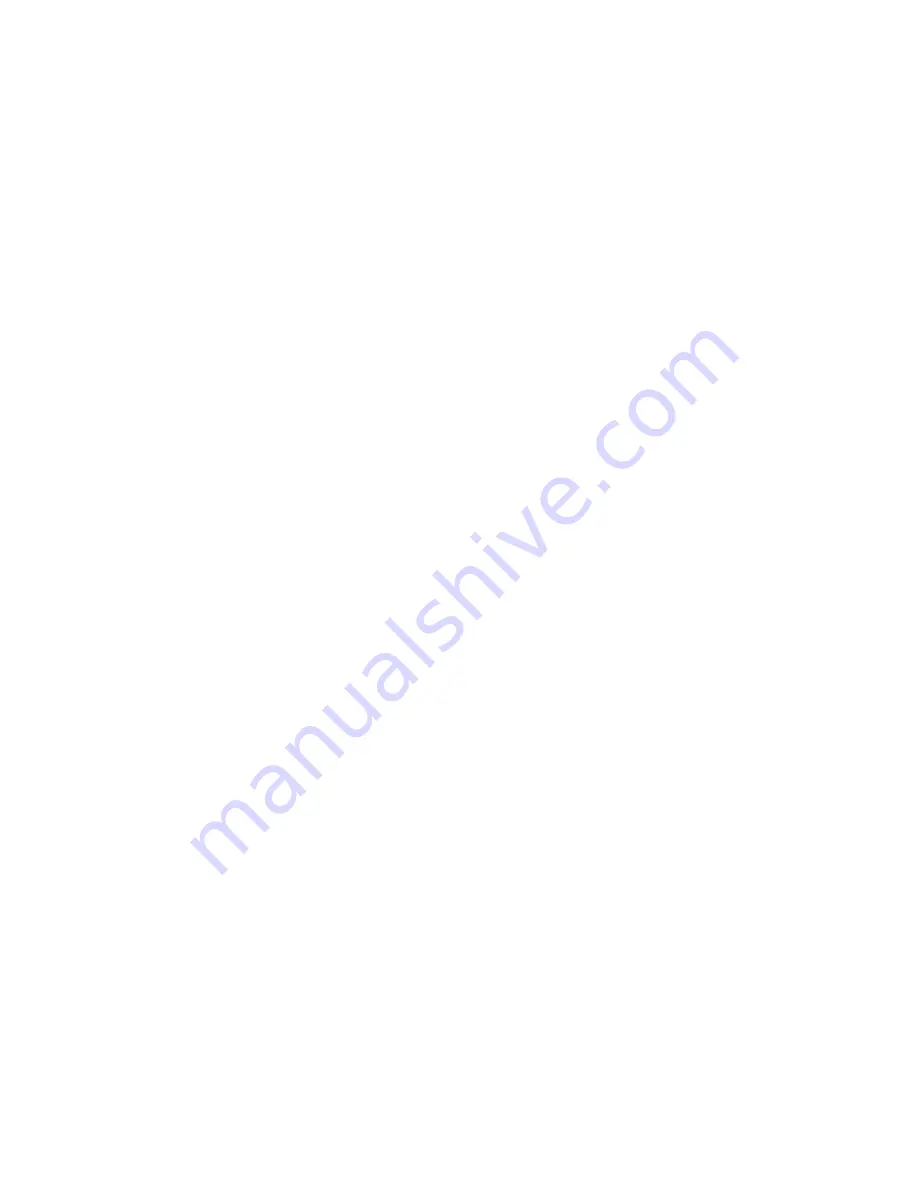
4.00
LUBRICATION REQUIREMENTS: POWER TRAIN AND PLUNGERS
4.1
Lubrication Capacity Requirements
The MSI Well Service Pump is a dry sump, i.e., it is not intended to contain a volume of lubricating oil. A
separate lubrication oil reservoir is required with a 50 gallon minimum capacity; it should be installed below
the plunger pump power end. It is recommended that a separate reservoir be used for each well service pump
on units with multiple well service pumps. Separate reservoirs prevent contaminants in one system from
affecting both lubrication systems and well service pumps. While the MSI Well Service Pump greatly reduces
the contamination, it is still prudent for the user to take all precautions to ensure long equipment life by
keeping lubrication systems separate and clean. Fill the reservoir with 45 gallons of the proper lubricating oil
listed in
Section 4.8
. A valve installed at the lowest point in the tank is recommended to allow for
accumulated water to be removed.
The MSI Well Service Pump is not equipped with an internal lubrication pump. The packager must add a
lubrication pump to one of the PTOs of the prime mover. The lubrication oil pump should be rated for 20
GPM and 300 PSI and be capable of pumping 90 wt oil. One lubrication pump must be dedicated to each well
service pump.
When designing the system, it is important to locate the lubrication oil pump on a PTO on the drive train that is
engaged whenever the prime mover (i.e. diesel engine) is running and not on a PTO that rotates only when the
transmission is in gear. A properly designed system will allow for oil circulation through the MSI Well
Service Pump prior to rotating the pump drive shaft and after the pump drive shaft rotation has been stopped
when the transmission has been returned to neutral. This is recommended so that the oil will warm up prior to
putting the pump into gear. The warmed oil will flow with less resistance and will better lubricate the moving
parts. Additionally, this will allow the oil to cool the pump after the plunger pump rotation has been stopped.
It is important to mount the lubrication pump as low as possible so that the pump does not cavitate as a result
of having to lift the fluid from the reservoir. If at all possible, the pump should be mounted below the outlet of
the reservoir.
A pressure gauge shall be placed as close to the top lubrication inlet port as possible to monitor lubrication
pressure. Pressure at this location must always be kept above 40 PSI, and flow rate to the plunger pump is
recommended to be at least 12 gpm at the inlet for a quintuplex, and at least 8 gpm for a triplex. Connect the
lubrication oil inlet line to the lower lubrication inlet port on either side of the well service pump; plug the
unused lubrication pipe ports with 1/2" NPT pipe plugs. Do not exceed 450 PSI lubrication pressure at the
MSI Well Service Pump power end lubrication inlet. (This pressure limitation does not apply to the fluid end
plunger lubrication system.)
Содержание QI-1000
Страница 7: ...1 20 Drawings Pump Assembly Overall Dimensions All Plunger Sizes TI 600 TRIPLEX...
Страница 8: ...QI 1000 QUINTUPLEX...
Страница 9: ...1 30 Dual Pump Assembly Overall Dimensions 1 30 1 600 HP Dual Pump Assembly Overall Dimensions...
Страница 10: ...1 30 2 1000 HP Dual Pump Assembly Overall Dimensions...
Страница 11: ...1 50 Drawings Gear Reducer Installation Positions 1 50 1 Gear Reducer Position Left Hand...
Страница 12: ...1 50 2 Gear Reducer Position Right Hand...
Страница 22: ...4 6 Lubrication Attachment Points See images below showing lubrication inlet and outlet locations...
Страница 36: ......
Страница 39: ...5 50 Power Frame Crank Rotation NOTE Crank Rotation can either be clockwise or counterclockwise...
Страница 43: ...Fluid End Assembly 3 25 4 50 continued...