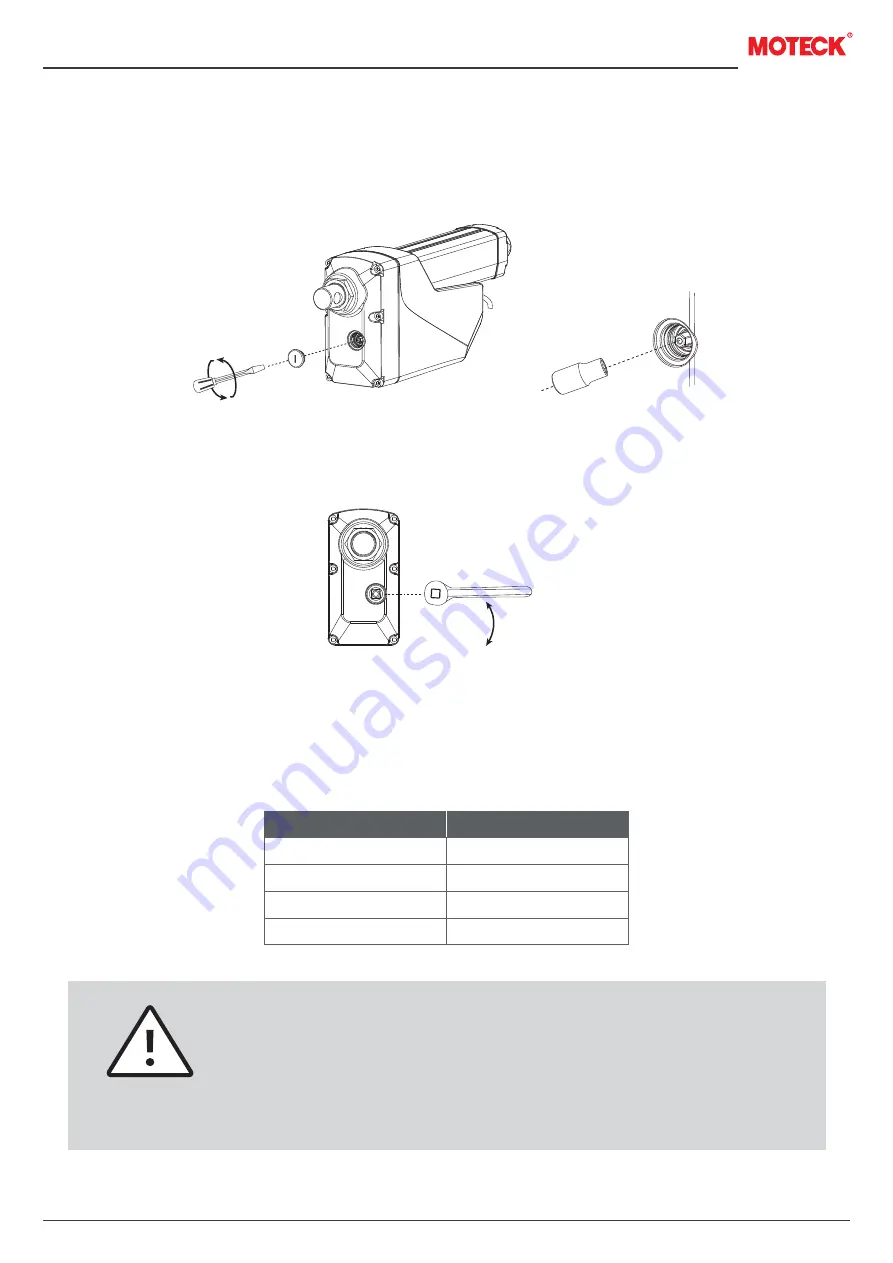
3.4.5
Installation and operation of hand crank
(1) When installing the actuator, please make sure that there is enough space between the rear connector and any
objects behind it so that the hand crank can be operated.
(2) Please use a flat-head screwdriver to remove the cover and connect with a 6mm hexagon socket.
(3) Use a wrench to operate as a hand crank.
(4) Under the maximum load of the actuator, the maximum torque required to drive the extension tube with the
hand crank is about 1.4Nm.
(5) The distance traveled by the actuator per rotation of the hand crank is related to the gear ratio options of the
actuator. Please refer to the table below.
www.moteck.com
8
3.4.3
Force and orientation
(1) The actuator can be installed in any orientation and can withstand push and pull loads.
(2) When installing the actuator, make ensure that the force of the load acts on the central axis of the extension tube
and rear connector.
(3) Use only solid and sized mounting pins. The mounting pins must be strong enough to support the load and
prevent it from falling off after installation.
(4) The mounting pins must be parallel to each other on the same plane, as shown in the sketch below.
(5) If the actuator is used on the equipment to rotate with the mounting pin as the axis, it must be ensured the
housing and other mechanical parts will not interfere and damage the actuator and equipment in the full range
of movement.
3.4.4
Cables and anti-pull lid
Before the actuator is shipped, the power cord and signal cable have been plugged in and the anti-pull lid has been
installed. Only the CAN Bus version (control option J00) needs to remove this lid and unplug the power cord when
manually changing the address through hardware (see 4.2.2.2). But please note that when installing the actuator,
you must ensure that there is enough space to remove the anti-pull lid with tools.
Gear type
10
15
20
30
mm /rev
1.349
0.804
0.609
0.379
●
Before using the hand crank, be sure to turn off the actuator power. Do not
apply torque exceeding 1.7Nm on the hand crank.
●
Do not move the extension tube to both ends of the stroke, otherwise the
actuator might be damaged.
●
Do not use any type of automatic drill or power tools to drive the manual
crank.