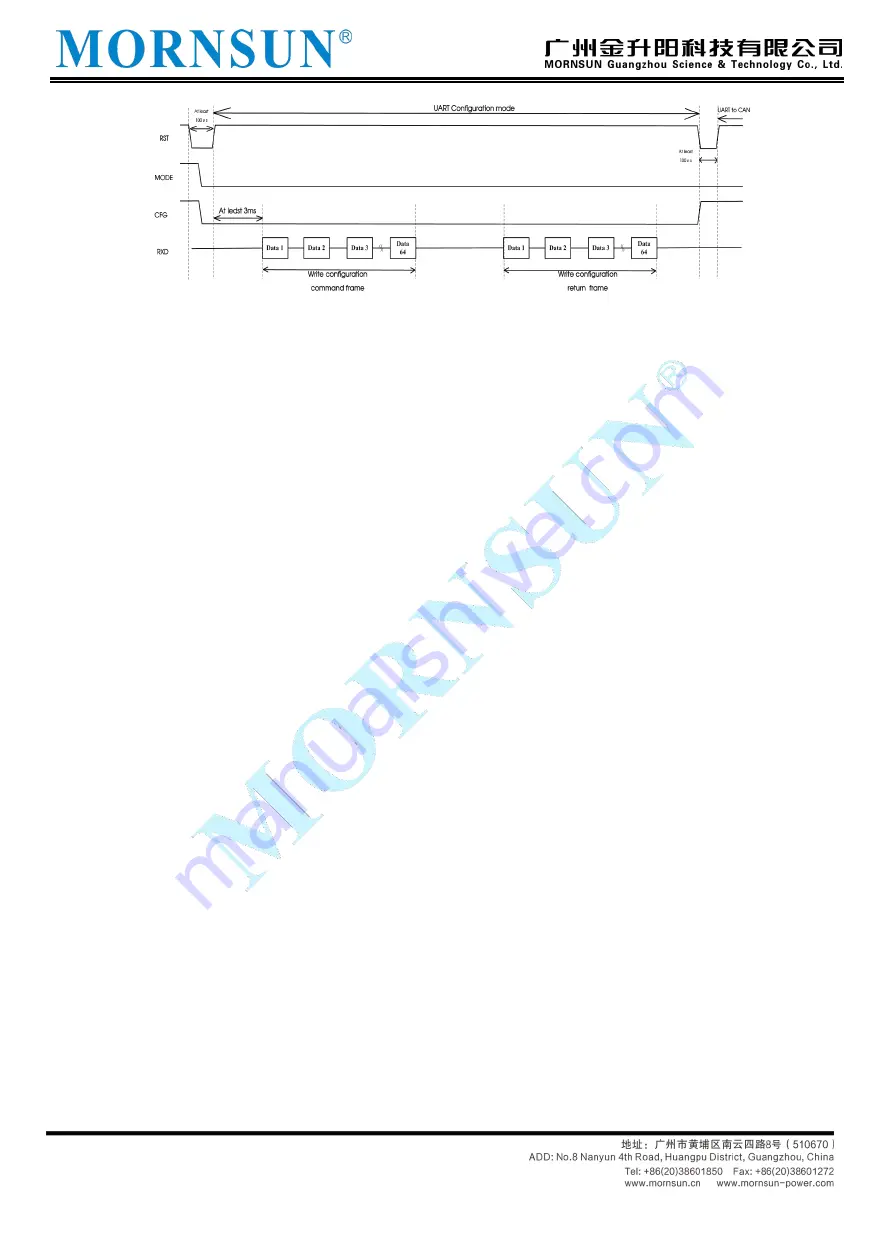
第 55 页 共 60 页
Figure 4.1 Timing diagram of configuration command written by UART
2.With SIP configuration
When the user uses the SPI interface of MCU to connect with TD5(3)USPCAN, the product parameters
can be configured through the SPI interface. Refer to Figure 2.3 and Figure 2.4 for the hardware connection
diagram.
The configuration method is as follows:
(1) CFG is set low, MODE is set high, RST is controlled to reset, wait for at least 3ms, and the product enters
SPI configuration mode;
(2) The CTL0 and CTL1 pins are set high to control TD5(3)USPCAN to enter the SPI master write state and
wait for at least 50us;
(3) Set SSEL low, MCU sends a write configuration command frame, then set SSEL high, wait for at least
150ms, or detect that the INT pin is low;
(4) CTL0 is set high, CTL1 is set low, and TD5(3)USPCAN is controlled to enter SPI master read state, waiting
for at least 50us;
(5) Set SSEL low, the master sends 5 bytes of invalid data, receives the product write configuration
response frame, and then sets SSEL high;
(6) Confirm the MCU write configuration response frame content, and judge whether the configuration is
successful;
(7) After configuration, CFG pin is set high, RST is reset, wait for at least 3ms, and the product enters SPI-
to- CAN mode. The timing diagram of writing configuration commands through SPI is shown in Figure 4.2. This
timing diagram is also suitable for reading configuration commands, verifying product identification and
other operations. It only needs to change the SPI reading and writing data and the waiting time after writing
configuration commands.