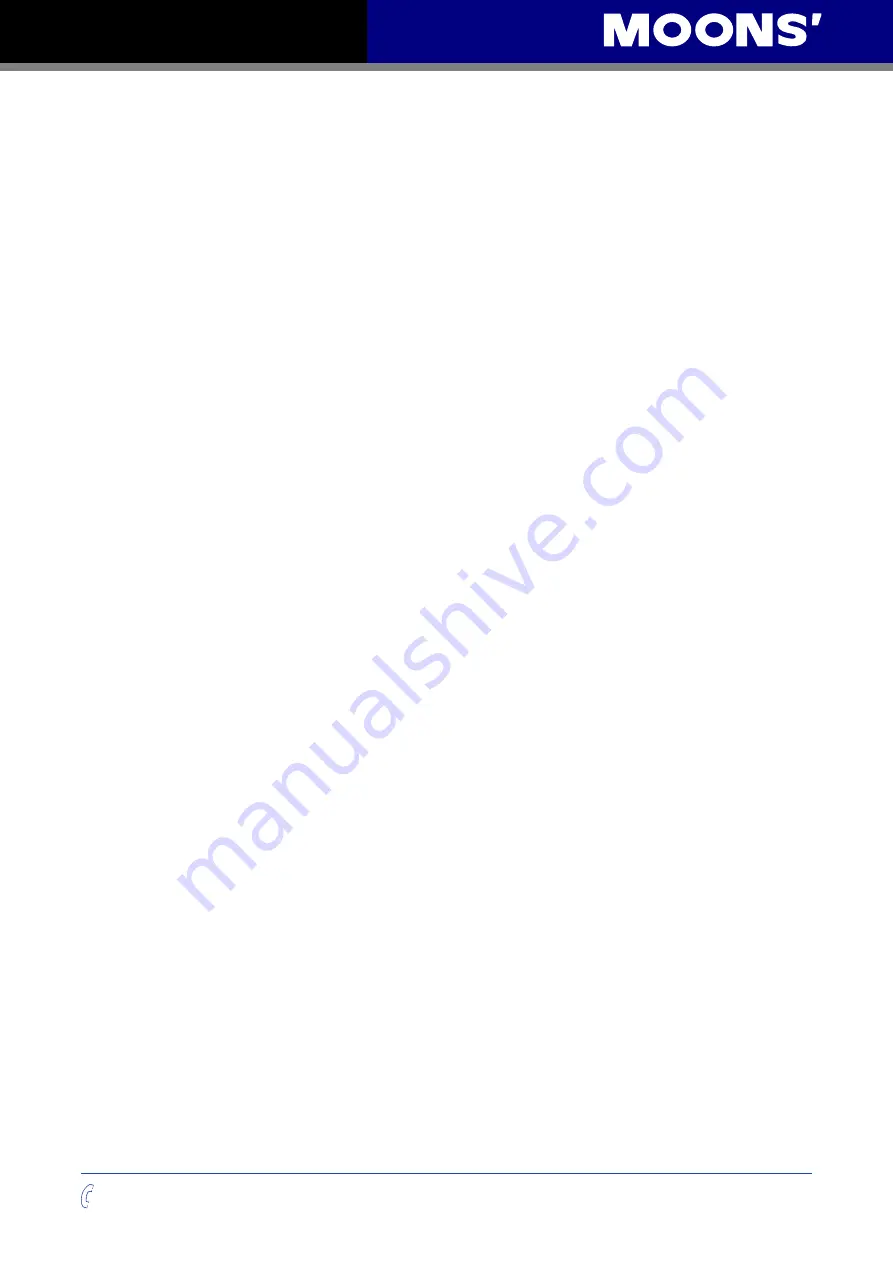
37
Rev. 1.0
0012072012
TSM24P User Manual
+86-400-820-9661
Sample Continuously:
after the
Start
button is clicked, the move will be repeated and the results
displayed until the
Stop
button is clicked. During continuous sampling the tuning gains can be
changed at any time and will be updated automatically. This enables more dynamic adjustment of
the gains for speeding up the tuning process.
5.6.2 Performing a Move
Once the move settings are correct the mechanism to be moved shold also be checked to ensure
it is ready to move. It is especially important to make sure the direction is set correctly. In some
cases it is wise to select
alternate
to avoid running the mechanism into a hard stop. Select the
Sample Once
button. Click the
Start
button and observe the results.
If problems occurred during the move an Alarm indicating a Fault or Warning may be displayed
and need to be cleared. The drive may be left disabled until the Alarm is cleared and the Enable
button is clicked.
Note: Clicking the Alarm Reset button and then the Enable button will clear a fault and
enable the drive.
Now the motion parameters will need to be adjusted to achieve the desired move profile. The
move can be repeated by clicking the
Start
button. If the drive continues to fault it is possible the
maximum current or position error parameters are being exceeded. These can be set in the
Drive
Configuration
tab.
The current setting can be checked by selecting
Current
in one of the Plot lists and clicking
Start
again to see what current is being required of the drive during a move. The current profile of the
move will be displayed and may give a clue as to why a fault is occurring.
5.6.3 Adjusting the Gain (KP) and Deri Gain (KD) parameters
Adjust the KP and KD parameters and observe the results. Increasing the KP may improve the
positioning performance, but it may also cause the system to be more unstable. To counter this
the KD can be increased. The KD parameter is important: too little gain will cause the system
to oscillate; too much gain may cause the system to squeal from a high frequency oscillation. If
a very springy coupler is used between the motor and load, the KD parameter may need to be
reduced until the system is stable or the
Notch Filter
may need to be used to reduce the system
gain at the sensitive frequency where it oscillates.
5.6.4 The Deri Filter (KE) parameter
With a large inertial load, the KP and KD gain parameters may need to be set high to get good
response. The filter may then need to be decreased in value (lower frequency) to prevent ringing
or decrease the derivative noise.
5.6.5 Filter parameter (again)
Sometimes it may also be necessary to adjust the output filter when gain values increase. The
filter frequency may then need to be decreased in value to prevent ringing or oscillation.
5.6.6 Verify the Drive Current
The amount of drive current can be verified at any time during the tuning process to make sure the
current supplied to the motor is not being limited by the drive. If too much current is being required
changes may be made to the move profile. Select
Current
in one of the
Plot
selection lists and
repeat the move, from this the current can be evaluated.
5.6.7 Finishing up
After verifying the drive current, the
Notch Filter
may be the only setting still needing adjusting.
See section 5.8 on “Setting the Notch Filter”.