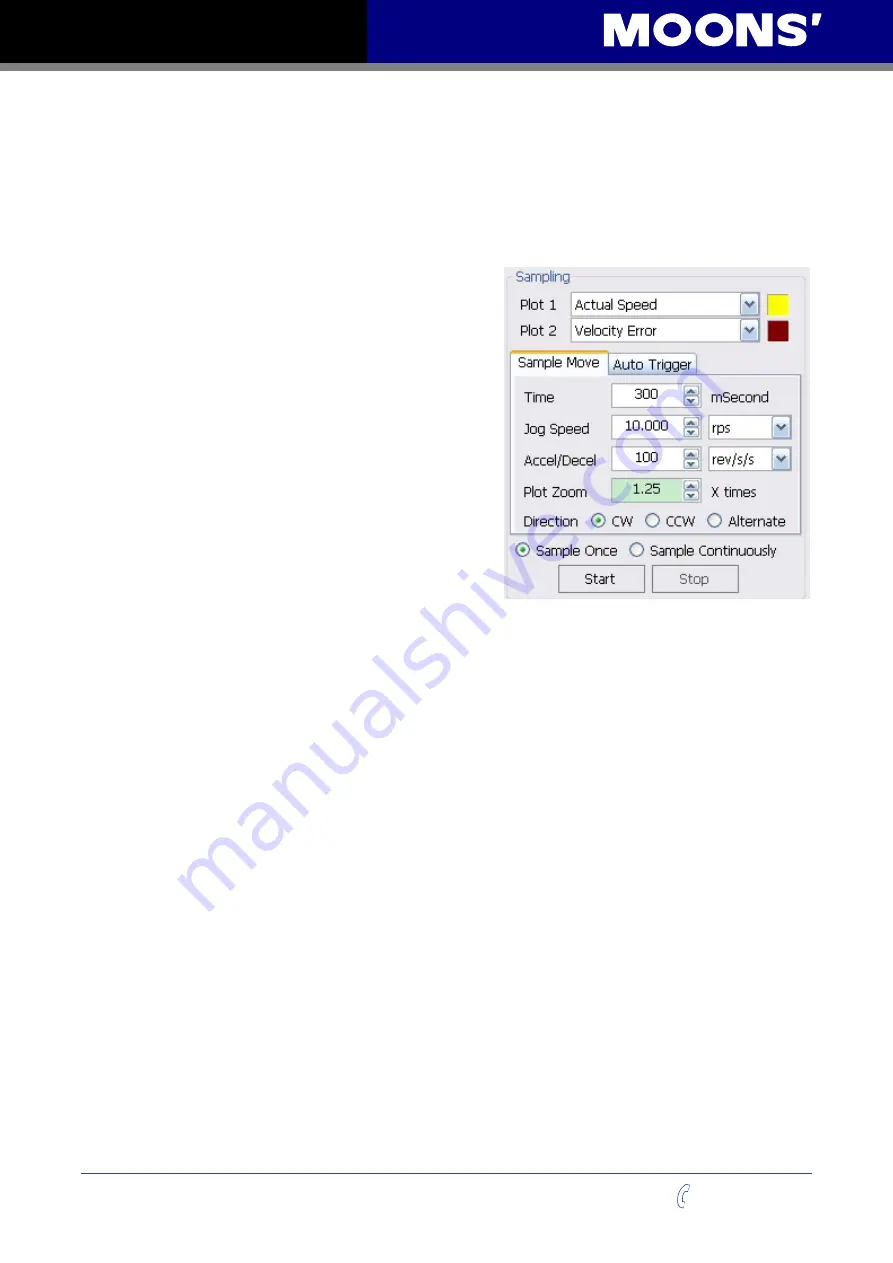
32
Rev. 1.0
0012072012
TSM24P User Manual
+86-400-820-9661
5.5 Tuning the Velocity Loop
5.5.1 Entering a Sample Move
Start by selecting the
V Loop
tab in the
Control Loop
dialog section. This will cause the
Sampling
to perform moves that are based on
Time
and operates the drive in the
Speed Only
Velocity mode.
Now parameters may be entered for a
Velocity
based move.
Plot 1 & Plot 2:
two different values can be selected
for viewing in the scope window, in this case
Actual
Speed
and
Velocity Error
are selected. These are
typical values for Velocity tuning.
Sample Move:
move profile values are entered in
the
Sample Move
section. This example sets a move
Time
of 200ms at a
Jog
Speed
of 20 rev/sec and an
Accel/Decel
rate of 300 rev/s/s. In the window to the
right of the
Sampling
data entry section the
Desired
Profile
will be displayed. This provides a visual
reference of what the expected move will look like.
Plot Zoom:
the length of the plot values that are
displayed can be set from 1 to 5 times the profile
length.
Dir:
the direction of the move can be set to
cw
,
ccw
or
alternate
. These directions refer to the motor shaft
as viewed from the front of the motor.
Alternate
toggles the direction after each move. Start with a
known direction before switching to toggle.
Sample Once:
after the
Start
button is clicked, a single move is performed, the motor stops, and
the results will be displayed.
Sample Continuously:
after the
Start
button is clicked, the move will be repeated and the results
displayed until the
Stop
button is clicked. During continuous sampling the tuning gains can be
changed at any time and will be updated automatically. This enables more dynamic adjustment of
the gains for speeding up the tuning process.
5.5.2 Performing a Move
Once the move settings are correct the mechanism to be moved shold also be checked to ensure
it is ready to move. It is especially important to make sure the direction is set correctly. In some
cases it is wise to select
alternate
to avoid running the mechanism into a hard stop. Select the
Sample Once
button. Click the
Start
button and observe the results.
If problems occurred during the move an Alarm indicating a Fault or Warning may be displayed
and need to be cleared. The drive may be left disabled until the Alarm is cleared and the Enable
button is clicked.
Note: Clicking the Alarm Reset button and then the Enable button will clear a fault and
enable the drive.
Now the motion parameters will need to be adjusted to achieve the desired move profile. The
move can be repeated by clicking the
Start
button. If the drive continues to fault it is possible the
maximum current or position error parameters are being exceeded. These can be set in the
Drive
Configuration
tab.
The current setting can be checked by selecting
Current
in one of the Plot lists and clicking
Start
again to see what current is being required of the drive during a move. The current profile of the
move will be displayed and may give a clue as to why a fault is occurring.