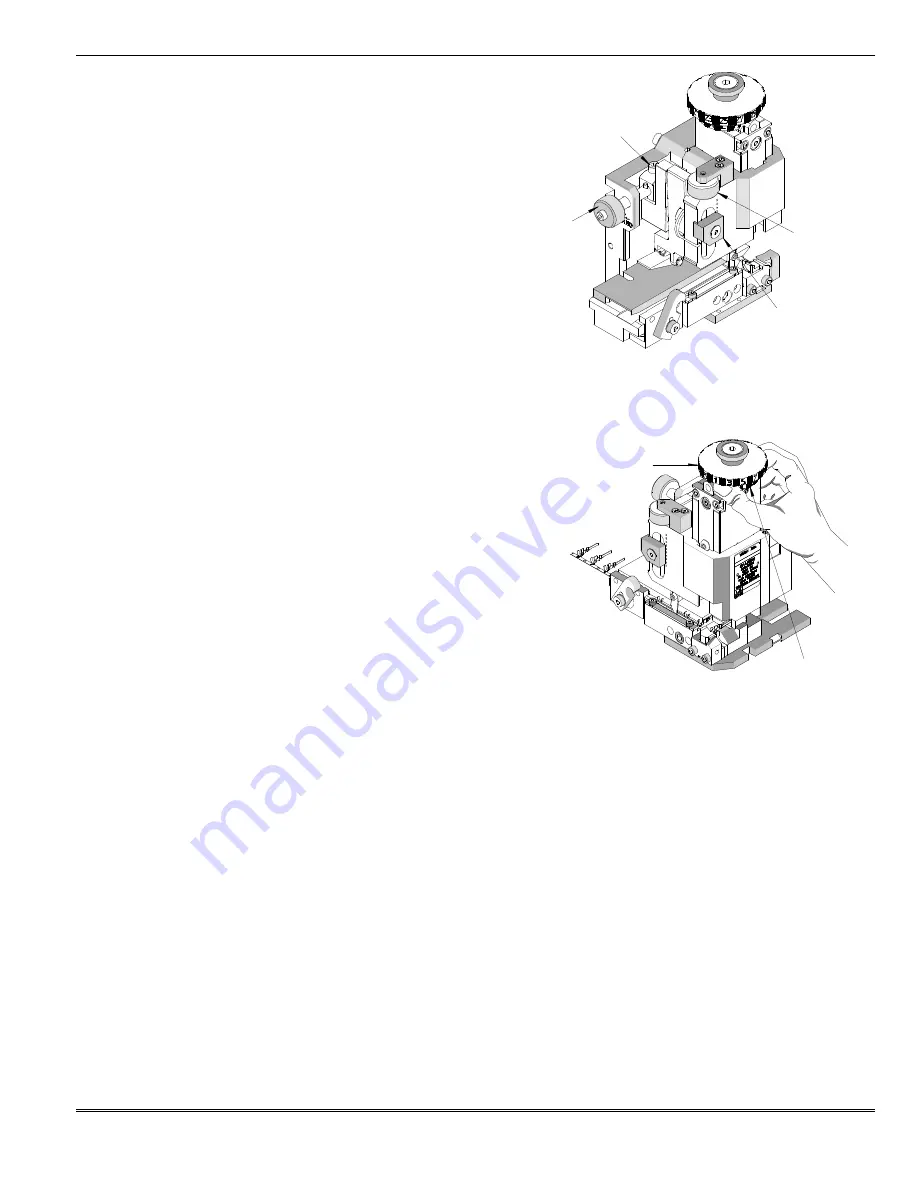
FineAdjust Applicator
Doc. No: TM-638004900
Release Date: 09-04-03
UNCONTROLLED COPY
Page 15 of 50
Revision: G
Revision Date: 01-15-13
PIVOT CLAMP
M5 FHCS
FORWARD
FEED
STROKE
ADJ. KNOB
M5 SHCS
FEED LOCK
BACK
STROKE
ADJ. KNOB
Figure 2-10
Figure 2-11
INSULATION
CAM (TOP)
CONDUCTOR
CAM (BOTTOM)
Forward Feed Adjustments
1.
The forward feed position must locate the terminal that is
being crimped exactly over the anvils.
2.
Disconnect the power from the press. Remove the
machine guards if necessary.
3.
Make sure there is a terminal over the anvils and the feed
finger is fully forward (closest to the anvils).
4.
Loosen the M5 SHCS.
5.
Turn the forward feed adjusting knob to position the
terminal. To decrease the feed position, turn the forward
feed adjusting knob clockwise. To increase the feed
position turn the forward feed adjusting knob
counterclockwise. See Figure 2-10.
6.
When adjusting to decrease the feed position, it is
necessary to pull the terminal strip backwards until it is against the feed finger. When increasing the feed position, the feed
finger will push the terminal farther over the anvils.
7.
After properly adjusting the forward feed position of the terminal, tighten the M5 SHCS with a 4mm hex wrench.
Back Stroke Feed Adjustments
1.
To properly feed the terminal strip, the back feed stroke should have
enough over-travel to pick up the next terminal. Too much over
travel may, in some cases, cause a double-feed.
2.
Disconnect the power from the press. Remove the machine guards if
necessary.
3.
To achieve the correct backstroke location, adjust the position of the
hinge bushing. First, use a 3mm hex wrench to loosen the M5 FHCS
holding the pivot clamp. Turning the backstroke adjustment knob
(which is located above the hinge bushing) clockwise will raise the
hinge bushing and will increase the backstroke. Turning the knob
counter clockwise (CCW) will lower the hinge bushing and will
decrease the feed backstroke. When adjustment is complete, tighten
the pivot clamp securely. See Figure 2-10.
4.
Since back feed stroke adjustment may not be visibly obvious, the terminal feed should be cycled (by hand, if possible) to
observe the changes.
5.
Back feed stroke adjustments may affect the entire feed linkage; re-adjustment of the forward feed stroke could be
necessary. See Forward Feed Adjustments.
Conductor Crimp Punch Adjustments
1.
With the guards intact, place a stripped length of suitable wire into the terminal and terminate the wire under power.
2.
Inspect the quality of conductor crimp and measure the crimp height. See Appendix A.3 Conductor Crimp Height
Measurement.
3.
If adjustments are necessary, turn off and disconnect the power supply from the press. Remove the machine guards.
4.
The desired crimp height can be achieved by rotating the conductor-adjusting cam. See Figure 2-11. Each increment
represents approximately 0.015mm (.0006") for a total adjustment of 1.80mm (.071"). The "A" setting is the loosest crimp
height and the "N" setting is the tightest. If you find that the crimp height is not acceptable, you can rotate the adjusting cam
until the desired crimp height is obtained. See Section 2.1, Shut Height. No shimming of the applicator is required.
5.
Replace the machine guards and repeat the previous steps until the desired crimp height is obtained. See Appendix A.3,
Conductor Crimp Height Measurement.
6.
Perform a pull test on conductor crimp to verify the mechanical integrity of the crimp. See Appendix A.5, Pull Force Test.