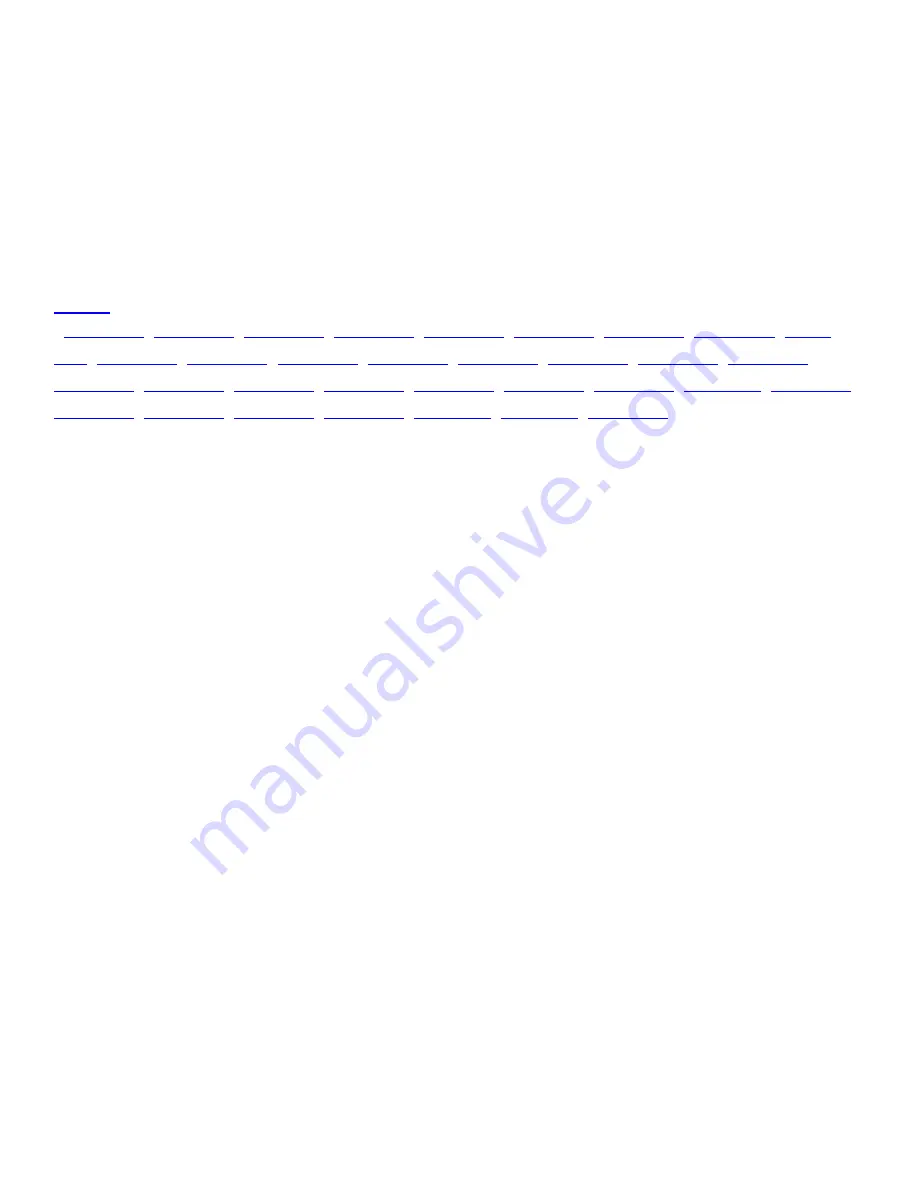
Mouser Electronics
Authorized Distributor
Click to View Pricing, Inventory, Delivery & Lifecycle Information:
Molex
:
63800-0115
63800-0313
63800-0119
63800-0127
63800-0330
63800-0345
63800-0116
63800-0120
63800-
0121
63800-0124
63800-0129
63800-0140
63800-0141
63800-0142
63800-0310
63800-0311
63800-0312
63800-0314
63800-0316
63800-0331
63800-0332
63800-0348
63800-4309
63800-4946
11-18-4238
63800-0302
63800-0117
63800-0118
63800-0143
63800-0122
11-32-5346
11-41-0127
63800-0126