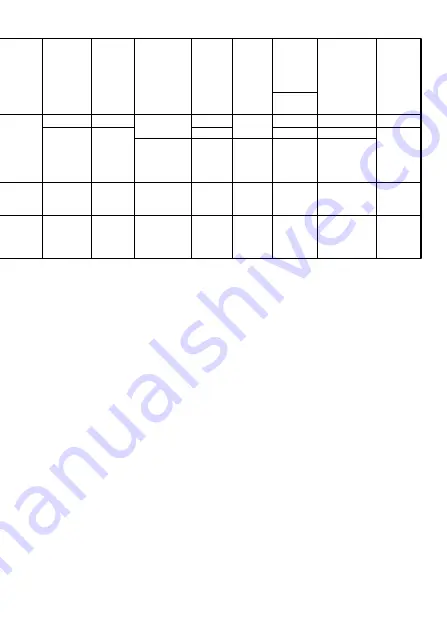
71
*3
Value at TYP 200VAC.
*4
Value at TYP 12VDC.
*5
"ERR." LED turns on when fuse is blown or external supply power is off.
*6
0.08A is shown on the rating plate of the module.
*7
0.15A is shown on the rating plate of the module.
Field
Wiring
Points/
Common
Surge
Suppression
Fuse
Rating
Error
display
External
Power
Supply
(TYP
DC24V)
Internal
Current
Consumption
No. of
Occupied
Points
Current
Terminal
8
Zener diode
5A
LED
0.020A
0.12A
16
37-pin
D-sub
connector
32
3.2A
0.008A
0.5A
32
Clamp diode
None
None
0.080A
0.5A
40-pin
connector
×2
32
Zener diode
3.2A
LED
*5
0.008A
0.93A
64
24-pin
connector
-
None
1.6A
LED
0.055A
0.18A
16/32
48/64
Содержание MELSEC-A A1SCPUC24-R2
Страница 2: ......
Страница 11: ...A 9 ...
Страница 12: ...A 10 ...
Страница 13: ...A 11 ...
Страница 14: ...A 12 ...
Страница 15: ...A 13 ...
Страница 16: ...A 14 ...
Страница 17: ...A 15 ...
Страница 105: ...79 MEMO ...
Страница 156: ...130 MEMO ...
Страница 159: ......