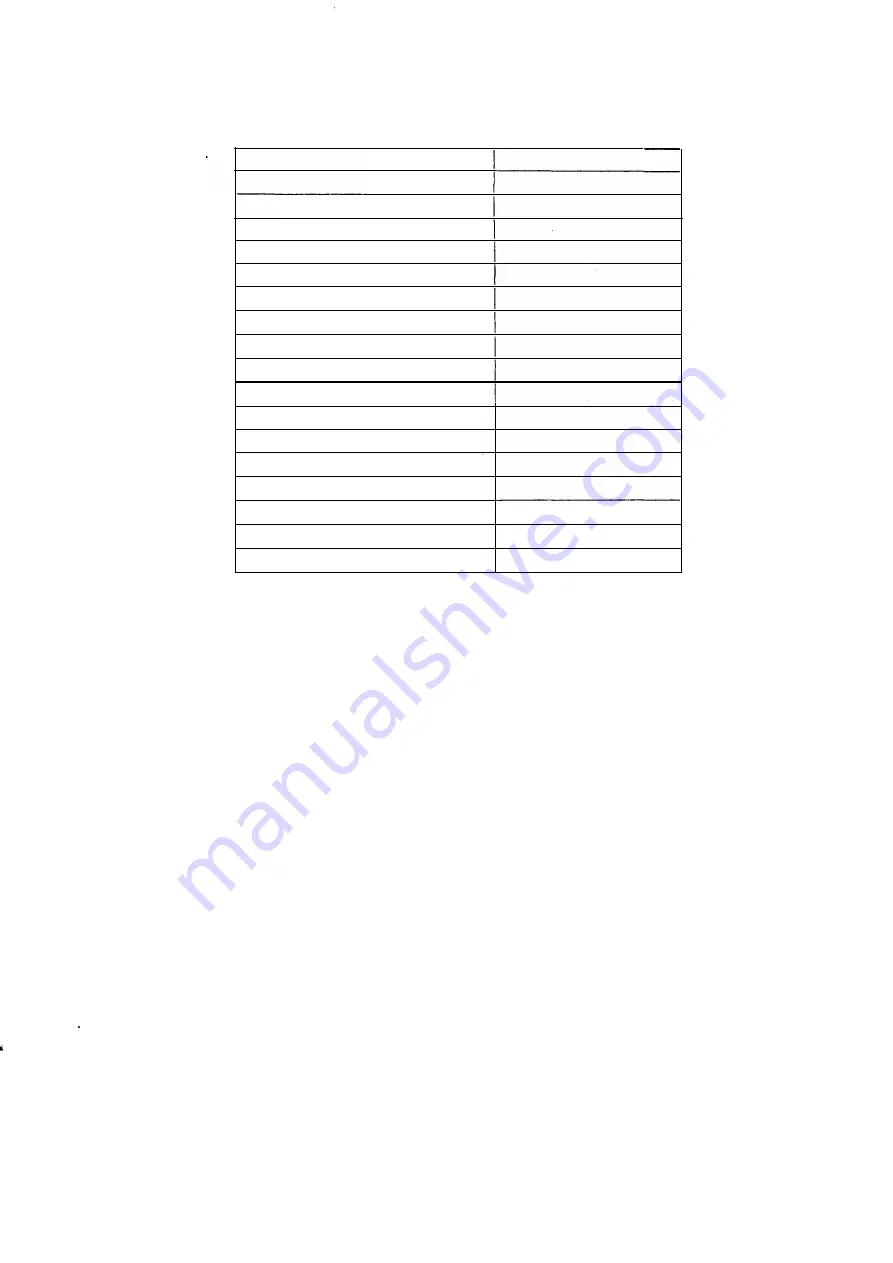
TIGHTENING TORQUE
Important bolts and nuts
Unit: kg,m (lb-ft)
Item
Torque
Cylinder head bolts
12.0 ± 0.5 (86.8 ± 3.6)
Main bearing cap bolts
8.5 ± 0.5 (61.5 ± 3.6)
Connecting rod cap bolts
5.5±0.5 (39.8 ± 3.6)
Rocker shaft bracket bolts
1.5 ± 0.5 (10.8 ± 3.6)
Front plate bolts
1.0 ± 0.5 ( (7.2 ± 3.6)
Timing gear case bolts
1.0 ± 0.5
(7.2 ± 3.6)
Camshaft thrust plate bolts
1.8 ± 0.5 (13.0 ± 3.6)
Idler thrust plate bolt
3.5 ± 0.5 (25.3 ± 3.6)
Crankshaft pulley nut
40.0
:t
0.5 (289.3 ± 3.6)
Rear plate bolts
3.5 ± 0.5 (25.3 ± 3.6)
Rear oil seal bolts
0.4
(2.9)
Flywheel bolts
8.5 ± 0.5 (61.5 ± 3.6)
Oil pan bolts
0.7
(5 .1)
Oil pan drain plug
10.0±0.5 (72.3 ± 3.6)
Nozzle holder retaining nuts
5.0 ± 0.5 (36.2 ± 3.6)
Injection pump delivery valve holders
3.0 ± 0.5 (21.7 ± 3.6)
Governor round nut
2.5
± 0.5 (18.1 ± 3.6)