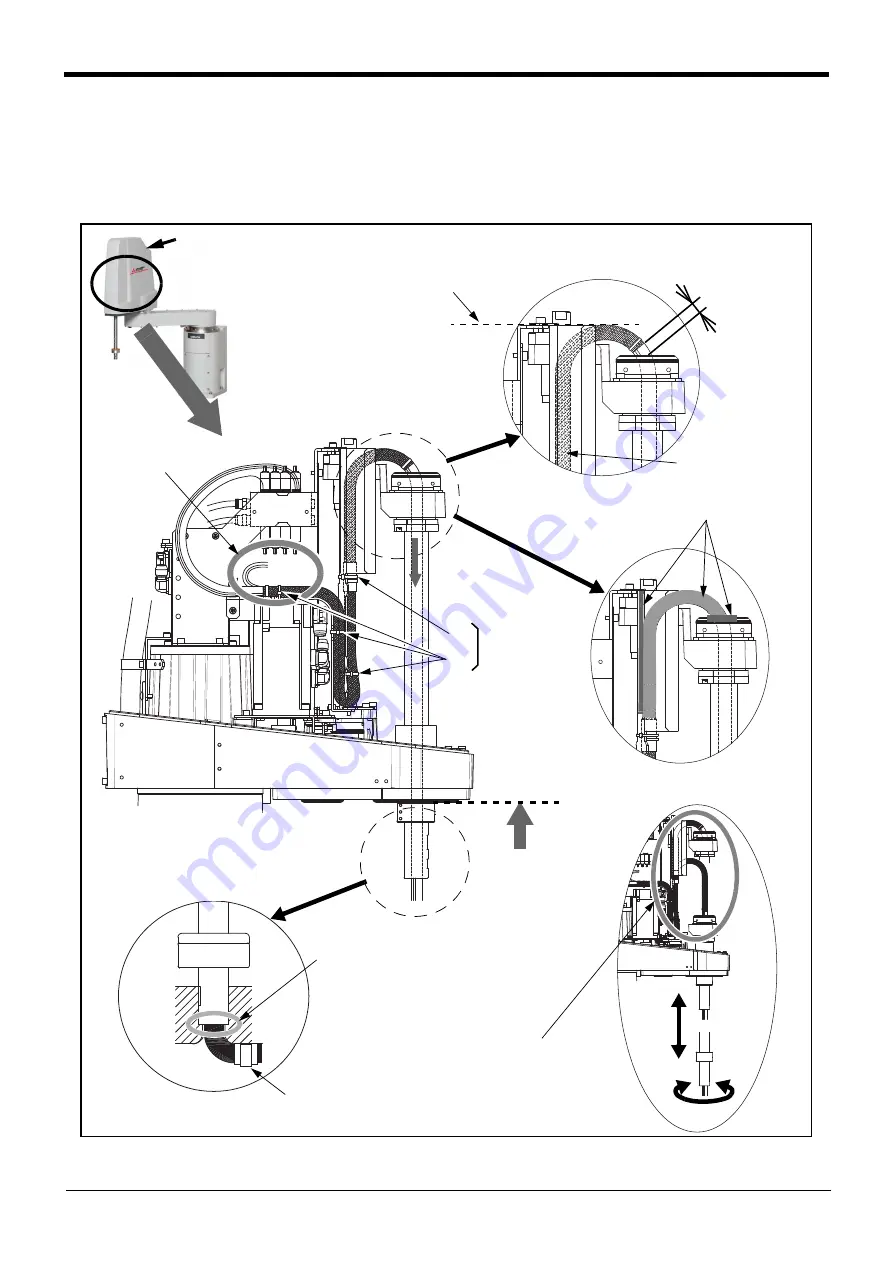
3-87
Hand internal wiring and piping set (RH-3FRH/6FRH/12FRH/20FRH series)
3Installing the option devices
(3) RH-6FRH series
Refer to
Page 84, "(1) Installation procedure"
and install cables and air hoses correctly. The numbers in
are correspond to the same numbers in
Turn the controller’s power OFF before this operation. Refer to
Page 101, "5.3.2 Installing/removing the cover"
for removing/ installing the cover.
Fig.3-20 : Installing the hand internal wiring and piping set (RH-6FRH series)
Connect inside the No.
2 arm cover U
No.2 arm cover U
(c)
Match up the peak of the air
hose and cable with the top
end of the fixing plate
Expanding sleeve
Approx. 10mm
Silicone grease application places
(a)
(b)
Top end of the
J3 axis operat
-
ing range
Perform the operation of the
J3 and J4 axes, and check
that no interference occurs.
J3 axis
J4 axis
Seal the outlet with the liquid gasket.
(Only for clean/oil mist specification)
Fixing air hoses and
cables inside a hand.