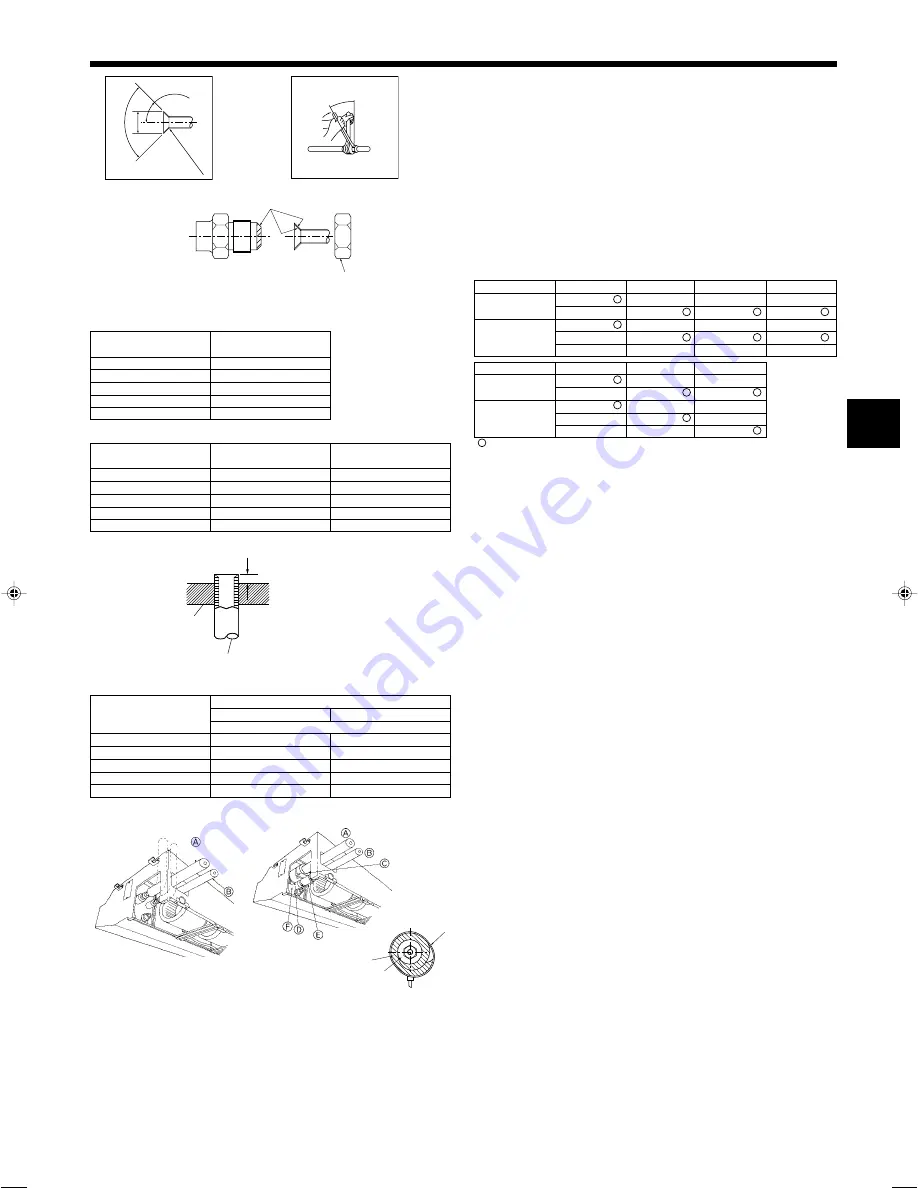
5
A
Die
B
Copper pipe
A
A
B
Fig. 4-2
Copper pipe O.D.
A (mm)
(mm)
Flare tool for R-22·R407C
Flare tool for R410A
Clutch type
ø6.35 (1/4")
0 - 0.5
1.0 - 1.5
ø9.52 (3/8")
0 - 0.5
1.0 - 1.5
ø12.7 (1/2")
0 - 0.5
1.0 - 1.5
ø15.88 (5/8")
0 - 0.5
1.0 - 1.5
ø19.05 (3/4")
0 - 0.5
1.0 - 1.5
Installing procedures
1. Slide the supplied pipe cover
2
over the gas tubing until it is pressed against the
sheet metal inside the unit.
2. Slide the provided pipe cover
3
over the liquid tubing until it is pressed against
the sheet metal inside the unit.
3. Tighten the pipe covers
2
and
3
at the both ends (15 - 20 mm) with the supplied
bands
4
.
• After connecting the refrigerant piping to the indoor unit, be sure to test the pipe
connections for gas leakage with nitrogen gas. (Check that there is no refrigerant
leakage from the refrigerant piping to the indoor unit.)
Conduct the airtightness test before connecting the outdoor unit stop valve and the
refrigerant pipe.
If the test is conducted after the valve and pipe are connected, gas, which is used
for checking the airtightness, will leak from the stop valve and flow into the outdoor
unit, resulting in abnormal operation.
G
C
DE
A
Gas tubing (with insulation)
E
Pipe cover
3
B
Liquid tubing (with insulation)
F
Press the pipe cover against the sheet metal.
C
Band
6
G
Refrigerant tubing heat insulating material
D
Pipe cover
2
Fig. 4-3
4.2. Indoor unit (Fig. 4-1)
• When commercially available copper pipes are used, wrap liquid and gas pipes
with commercially available insulation materials (heat-resistant to 100 °C or more,
thickness of 12 mm or more).
• The indoor parts of the drain pipe should be wrapped with polyethylene foam insu-
lation materials (specific gravity of 0.03, thickness of 9 mm or more).
• Apply thin layer of refrigerant oil to pipe and joint seating surface before tightening
flare nut.
• Use two wrenches to tighten piping connections.
• Use leak detector or soapy water to check for gas leaks after connections are com-
pleted.
• Use refrigerant piping insulation provided to insulate indoor unit connections. Insu-
late carefully following shown below.
• Use correct flare nuts meeting the pipe size of the outdoor unit.
Available pipe size
RP35, 50
RP60
RP71
RP100, 125, 140
Liquid side
ø6.35
ø6.35
–
–
ø9.52
ø9.52
ø9.52
ø9.52
ø12.7
–
–
–
Gas side
ø15.88
ø15.88
ø15.88
ø15.88
–
–
–
ø19.05
P25
P35, 50, 60, 71 P100, 125, 140
Liquid side
ø6.35
–
–
–
ø9.52
ø9.52
ø12.7
–
–
Gas side
–
ø15.88
–
–
–
ø19.05
: Factory flare nut attachment to the heat-exchanger.
4. Installing the refrigerant piping
90
°
±
0.5
°
ø
A
R0.4~R0.8
A
45
°±
2
°
B
Apply refrigerating machine oil over the entire flare seat surface.
Be sure to only use the flare nuts
that came with the unit.
A
Flare cutting dimensions
Copper pipe O.D.
Flare dimensions
(mm)
øA dimensions (mm)
ø6.35
8.6 - 9.0
ø9.52
12.6 - 13.0
ø12.7
15.8 - 16.2
ø15.88
19.0 - 19.4
ø19.05
22.9 - 23.3
B
Flare nut tightening torque
Copper pipe O.D.
Tightening torque
Tightening angle
(mm)
(N·m)
(Guideline)
ø6.35
14 - 18
60˚ - 90˚
ø9.52
35 - 42
60˚ - 90˚
ø12.7
50 - 58
30˚ - 60˚
ø15.88
75 - 80
30˚ - 60˚
ø19.05
100 - 140
20˚ - 35˚
Fig. 4-1