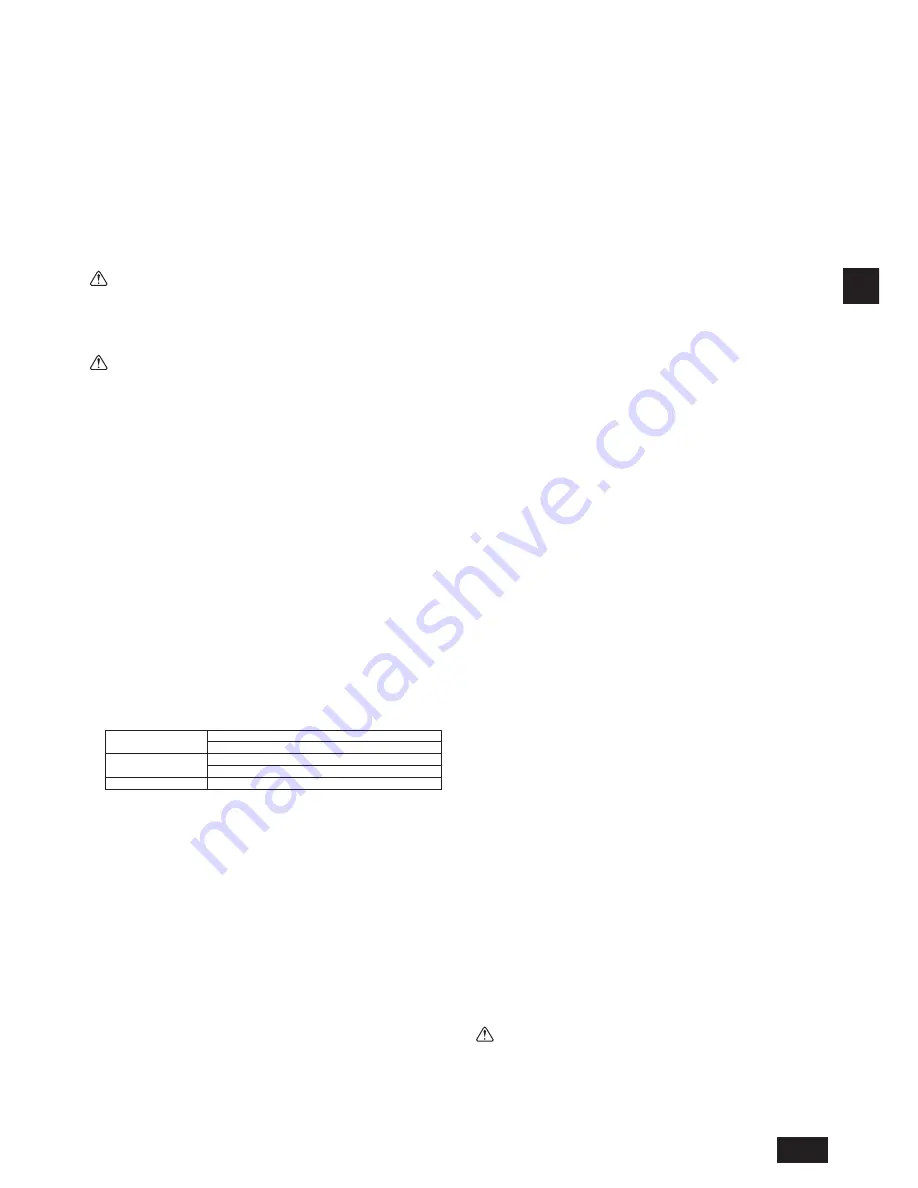
GB
15
4.2. Refrigerant piping work
After connecting the refrigerant pipes of all indoor and outdoor units with the
outdoor units’ stop valves remained fully closed, evacuate vacuum from the
outdoor units’ stop valve service ports.
After completing the above, open the outdoor units’ stop valves. This connects
the refrigerant circuit (between outdoor and BC controller) completely.
How to handle stop valves is described on each outdoor unit.
Notes:
•
After pipe connection, be sure to check that there is no gas leakage, using
a leak detector or soap-and-water solution.
•
Before brazing the refrigerant piping,
always wrap the piping on the main
body, and the thermal insulation piping, with damp cloths to prevent heat
shrinkage and burning the thermal insulation tubing.
Take care to ensure
that the flame does not come into contact with the main body itself.
•
Do not use leak-detection additives.
Warning:
Do not mix anything other than the specified refrigerant (R410A) into the
refrigerating cycle when installing or moving. Mixing air may cause the
refrigerating cycle to reach abnormally high temperature, resulting in burst
pipes.
Caution:
Cut the tip of the outdoor unit piping, remove the gas, and then remove the
brazed cap.
[Fig. 4.2.1] (P.5)
Ⓐ
Cut here
Ⓑ
Remove brazed cap
4.3. Insulating refrigerant pipes
Be sure to add insulation work to refrigerant piping by covering high-pressure
pipe and low-pressure pipe separately with enough thickness heat-resistant
polyethylene, so that no gap is observed in the joint between indoor unit and
insulating material, and insulating materials themselves. When insulation work is
insufficient, there is a possibility of condensation drip, etc. Pay special attention
to insulation work in the ceiling plenum.
[Fig. 4.3.1] (P.5)
Ⓐ
Insulating material for pipes (not supplied)
Ⓑ
Bind here using band or tape.
Ⓒ
Do not leave any opening.
Ⓓ
Lap margin: more than 40 mm
Ⓔ
Insulating material (not supplied)
Ⓕ
Unit side insulating material
Ⓖ
Minimum 30 mm
•
Insulation materials for the pipes to be added on site must meet the following
specifications:
Outdoor unit
-BC controller
High-pressure pipe: 10 mm or more
Low-pressure pipe: 20 mm or more
BC controller
-indoor unit
Pipe size 6.35 to 25.4 mm: 10 mm or more
Pipe size 28.58 to 41.28 mm: 15 mm or more
Temperature resistance 100°C or above
•
Installation of pipes in a high-temperature high-humidity environment, such as
the top floor of a building, may require the use of insulation materials thicker
than the ones specified in the chart above.
• When certain specifications presented by the client must be met, ensure that
they also meet the specifications on the chart above.
•
The brazed connections must be covered with the insulations, its cutting
surface upward and fastened with the bands.
•
Insulate the pipe that protrudes from the BC controller if the pipe is not going
to be connected to other pipes.
[Fig. 4.3.2] (P.5)
Ⓐ
Insulating material (not supplied)
Ⓑ
Bind here using band or tape.
4.4. Drain piping work
1. Drain piping work
• Tilt the drain pan so that the water will flow toward the drain socket.
[Fig. 4.4.1] (P.5)
①
Unscrew the two screws that are holding the side panel on the right
side of the control box.
②
Tilt the drain pan.
③
Screw down the screws with the drain pan tilted.
•
Ensure that the drain piping is downward (pitch of more than 1/100) to the
outdoor (discharge) side. Do not provide any trap or irregularity on the way.
•
Ensure that any cross-wise drain piping is less than 20 m (excluding the
difference of elevation). If the drain piping is long, provide metal braces to
prevent it from waving. Never provide any air vent pipe. Otherwise drain may
be ejected.
•
Use a hard vinyl chloride pipe VP-25 (with an external diameter of 32 mm) for
drain piping.
•
Ensure that collected pipes are 10 cm lower than the unit body’s drain port.
•
Do not provide any odor trap at the drain discharge port.
•
Put the end of the drain piping in a position where no odor is generated.
•
Do not put the end of the drain piping in any drain where ionic gases are
generated.
[Fig. 4.4.2] (P.6)
○
Correct piping
×
Wrong piping
Ⓐ
Insulation (9 mm or more)
Ⓑ
Downward slope (1/100 or more)
Ⓒ
Support metal
Ⓚ
Air bleeder
Ⓛ
Raised
Ⓜ
Odor trap
Grouped piping
Ⓓ
O.D. ø32 PVC TUBE
Ⓔ
Make it as large as possible. About 10 cm.
Ⓕ
Indoor unit
Ⓖ
Make the piping size large for grouped piping.
Ⓗ
Downward slope (1/100 or more)
Ⓘ
O.D. ø38 PVC TUBE for grouped piping. (9 mm or more insulation)
Ⓙ
BC controller
1. Insert the drain hose (accessory) into the drain port (insertion margin: 32
mm). (The drain hose must not be bent more than 45° to prevent the hose
from breaking or clogging.)
(Attach the hose with glue, and fix it with the band (small, supplied).)
2. Attach the drain pipe (O.D. ø32 PVC TUBE PV-25, not supplied).
(Attach the pipe with glue, and fix it with the band (small, supplied).)
3. Perform insulation work on the drain pipe (O.D. ø32 PVC TUBE PV-25) and
on the socket (including elbow).
4. Check the drainage.
5.
Attach the insulating material, and fix it with the band (large, supplied) to
insulate the drain port.
[Fig. 4.4.3] (P.6)
Ⓐ
BC controller
Ⓑ
Tie band (supplied)
Ⓒ
Visible part
Ⓓ
Insertion margin
Ⓔ
Drain hose (supplied)
Ⓕ
Drain pipe (O.D. ø32 PVC TUBE, not supplied)
Ⓖ
Insulating material (not supplied)
Ⓗ
Tie band (supplied)
2. Discharge test
After completing drain piping work, open the BC controller panel, and test drain
discharge using a small amount of water. Also, check to see that there is no
water leakage from the connections.
3. Insulating drain pipes
Provide sufficient insulation to the drain pipes just as for refrigerant pipes.
Caution:
Be sure to provide drain piping with heat insulation in order to prevent
excess condensation. Without drain piping, water may leak from the unit
causing damage to your property.