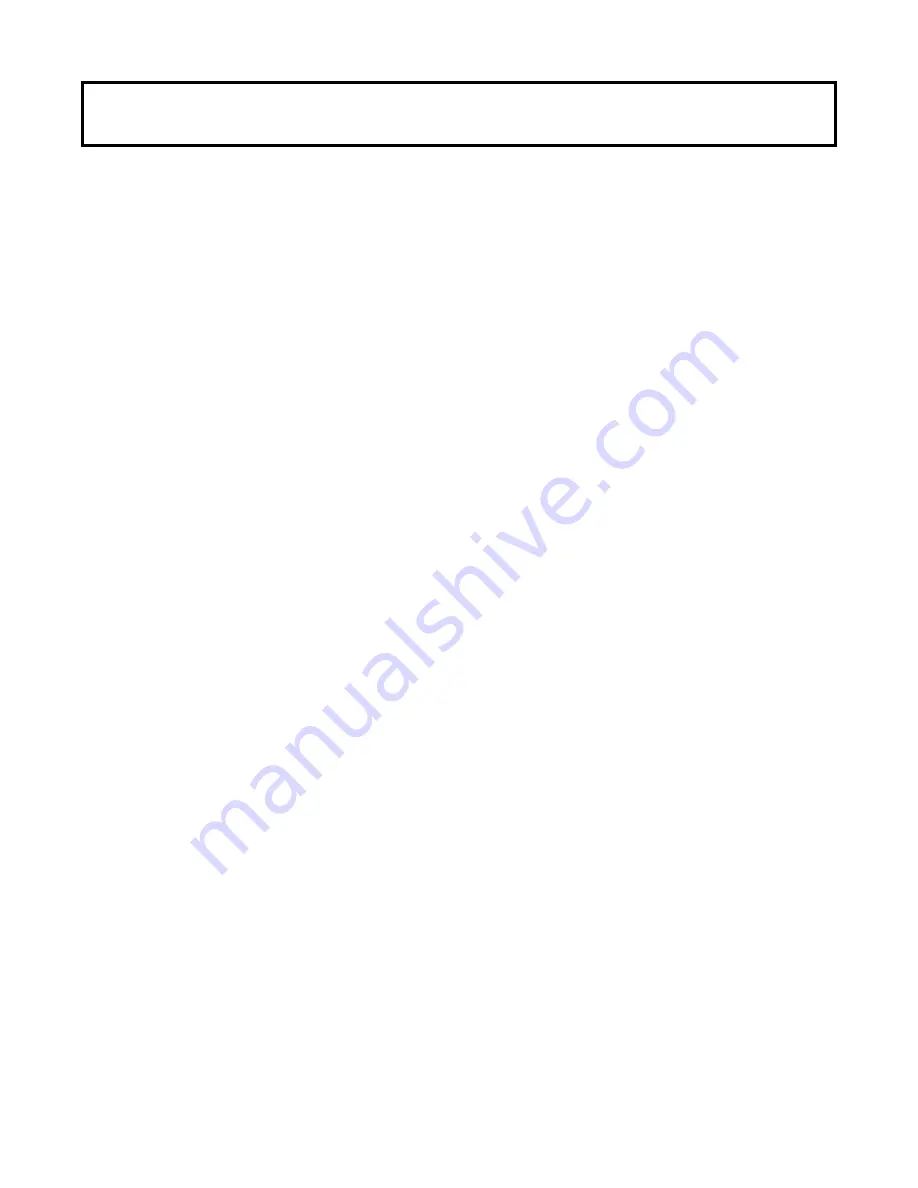
In order that the most efficient and intelligent use
can be made of mechanical power presses, it is
important that press users fully understand the
operation of each machine; that they have dies of the
proper size correctly installed, and that they install point-
of-operation safeguarding complying with the applica-
ble codes, standards, and laws for their particular area.
The tonnage, size, and operating characteristics of
all available presses should be known so that a
press closely matching requirements of the die can
be selected. MINSTER presses are built in a wide
range of tonnages, widths, drives, stroke lengths and
speeds. Each of these factors should be considered
when planning the installation of a die. Failure to do so
could result in overload of the press or its drive train.
The die designer can be most helpful by supplying
capacity requirements for a die. This amount should
be stamped on the die set at a position that can be eas-
ily seen. If such information has not been furnished,
several types of calculators, charts, tables and pub-
lished technical data are available to help determine
capacity requirements for a particular die. Be conserva-
tive when calculating tonnages for complex dies so that
a press of ample capacity will be used for the job. Then,
after dies are installed, confirm calculations by checking
actual press loading. Care should also be taken to avoid
off-center loading.
It is important that press users understand the dif-
ference between geared and non-geared presses,
and that they know the type of work most suitable
for each. They should also be aware that it is possible
to overload the press drive by installing dies requiring
work to be performed far above bottom of stroke. This
situation can occur even though the load requirements
of the workpiece fall within the rated capacity of press
frame members. Reference to the applicable Tonnage
Chart should be helpful.
Detailed information concerning the selection and
application of mechanical presses is not within the
scope of this manual. However, some of the salient
points of press construction and mechanics are includ-
ed as a guide for those who may be interested.
TONNAGE
The most basic of all press load measurements is
tonnage. It is the force exerted by the press against the
workpiece and is usually measured in tons. Although
this is one of the most basic measurements, it is prob-
ably one of the least understood.
The amount of direct tonnage that a mechanical
press is able to exert is at minimum near mid-
stroke; however, it increases progressively from
that point to its maximum rating at a specified point
near bottom of stroke. The reason for this is that the
crankshaft lever arm becomes effectively shorter as the
stroke progresses downward. Actually, this action
could be compared to moving the fulcrum point of a
lever gradually closer to the load. Additional informa-
tion regarding this concept is given on page H-3.
It can be established then, that in a mechanical press,
the drive is designed to deliver full rated tonnage only
at, or below, a specified point above bottom of stroke.
Of course, because of the mechanics involved, the
drive could deliver greater force below the specified
point except for other limiting factors such as frame and
bearing stress.
Frame parts are built to sustain the full rated tonnage
capacity of the press no matter what the position of the
press stroke. The parts are capable of withstanding full
rated tonnage without deflecting beyond standards
which are consistent with good engineering practice,
provided the load is evenly spread over the center two-
thirds of the right-to-left bolster dimension.
Some press users spend an amount of time calculating
press loads and then unintentionally overload the press
by adjusting the slide too low. Dies that bottom on the
material can cause severe overloads if set too low,
especially when large areas of the material are con-
tacted. An increase in material thickness after the dies
are set can also cause tremendous loads to be
imposed on the machine.
It is also possible to induce shock loads into a press
that will exceed calculated blanking forces. This situa-
tion may occur when slide force is suddenly released,
the result of breakthrough when blanking thick or high
carbon steel. A torsional twist is applied to the crank-
shaft as pressure is applied to the stamping. Suddenly,
as the material shears, the load is released and a
rebound occurs in the crankshaft, main gear, pinion,
drive keys, connection and other press parts. Use of
short stroke presses with shutheight set for minimum
punch penetration will help to ease this condition.
Extra care should be exercised in setting coining,
embossing or forming dies since these dies are of the
closed type and do not provide relief for flow or dis-
placement of excess material. Also, if wrinkles should
start to develop with draw dies, the cause should be
checked and corrected. Never attempt to iron wrinkles
H - 2
PRESS APPLICATION
Содержание IOI
Страница 1: ...Manual No 1010C MINSTER 8952 399 15 00 Service Manual OBI OBS SERIES PRESS MODEL...
Страница 2: ...Manual No 1010C MINSTER 8952 399 15 00 Service Manual OBI OBS SERIES PRESS MODEL...
Страница 9: ......
Страница 25: ......
Страница 51: ......
Страница 63: ......
Страница 85: ...I 8 COMMENTS CORRECTIVE STEPS TAKEN Inspected By Press approved for operation Press NOT approved for operation...
Страница 87: ...I 10 COMMENTS CORRECTIVE STEPS TAKEN Inspected By Press approved for operation Press NOT approved for operation...
Страница 89: ...I 12 COMMENTS CORRECTIVE STEPS TAKEN Inspected By Press approved for operation Press NOT approved for operation...
Страница 90: ...ADDITIONAL COMMENTS I 13...