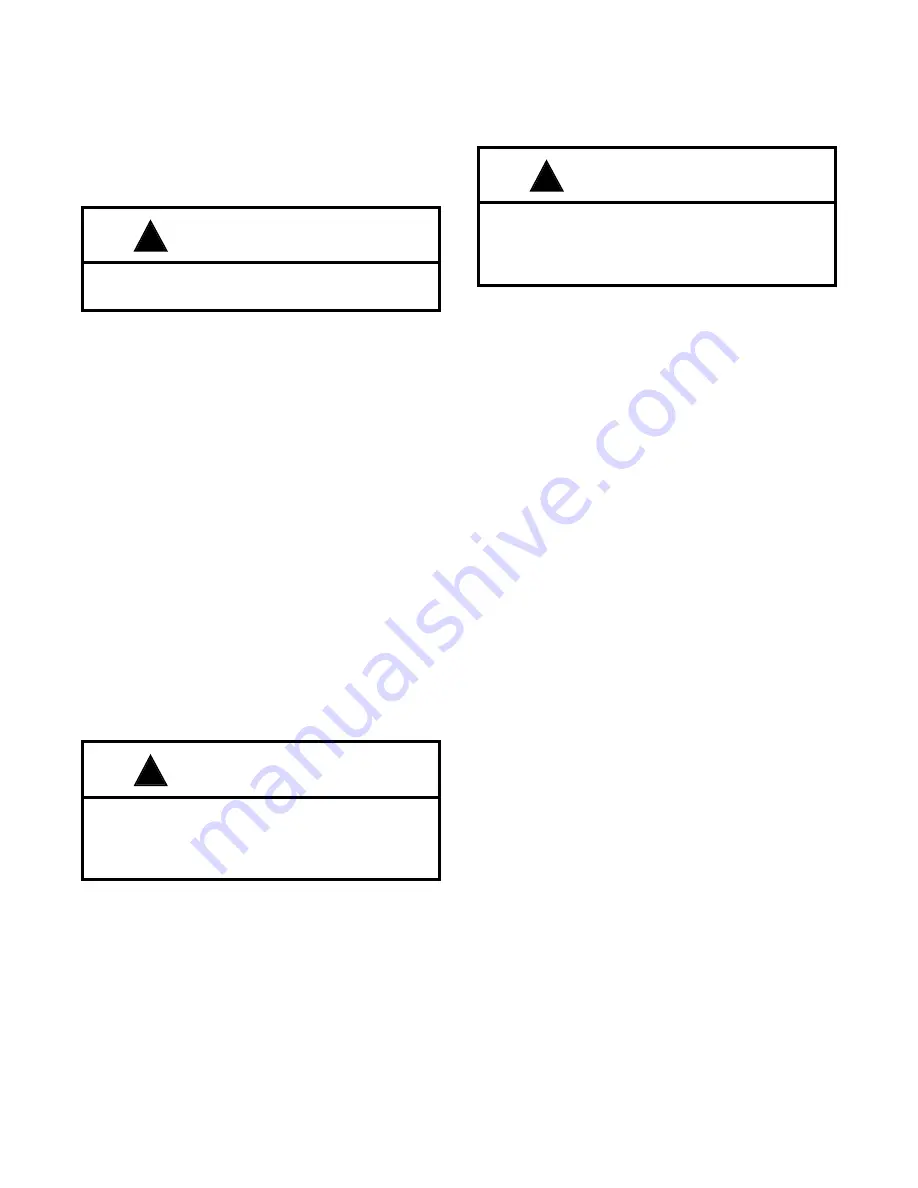
5. Determine slide position (i.e., before or after bottom
of stroke). This will determine the direction the fly-
wheel should be rotated.
6. Remove the bumping pin from the bumping pin
receptacle. Then insert the bumping pin into the
hole in the flywheel web.
WARNING
KEEP FINGERS CLEAR OF BUMPING HOLE IN THE
FLYWHEEL.
7. Rotate the flywheel until the bumping pin can be
inserted into the slotted portion of the clutch end-
driven disc. Then manually pull on the bumping pin
to rotate the flywheel in the direction determined in
Step 5 and let the pin strike against the striking lug
on the clutch. Repeat this step several times to
release the slide.
TOTAL BEARING CLEARANCE
Total bearing clearance is the total accumulation of
clearances in the main, connection, and ball box bear-
ings of the press. Check total bearing clearance every
six (6) months or more frequently if the press is operat-
ed in excess of 50 hours per week.
TO CHECK TOTAL BEARING CLEARANCE:
EQUIPMENT REQUIRED:
•
Base Mounted Dial Indicator (calibrated 0.001” or
0.01 mm)
•
Hydraulic Jack
1. Remove dies or tooling from the press.
WARNING
MAKE CERTAIN THAT THE FLYWHEEL IS COM-
PLETELY STOPPED AND THAT THE POWER HAS
BEEN DISCONNECTED FROM THE DRIVE MOTOR
BEFORE REMOVING DIES.
2. Clean the slide face and the top surface of the bed
(or bolster).
3. Place the POWER, OFF-ON-BAR Selector Switch
in the ON position.
4. Turn ON the air supply to the press.
5. Start the main drive motor and lubrication pump
motor and make certain that oil is dripping from the
gibs.
6. Place the Stroking Selector Switch in the INCH
position. Then position the slide at Bottom Dead
Center (BDC) of the stroke.
WARNING
MAKE CERTAIN THAT ALL PERSONS AVOID ANY
PINCHING POINTS ASSOCIATED WITH THE OPER-
ATION OF THE PRESS AND/OR ITS AUXILIARY
EQUIPMENT.
7. Stop the main drive motor and place the Stroking
Selector Switch in the OFF position. Make certain
that the flywheel has stopped turning completely.
Attach a WARNING sign to the press controls to
warn other personnel that the press is currently
being serviced.
8. Exhaust all air pressure from the counterbalance
cylinder.
9. Place a hydraulic jack between the slide face and
the bed (or bolster). Position the jack on the bed
so that it is centered beneath the slide connection
screw.
NOTE: To prevent damage to the slide and/or bed,
place flat steel plates between the jack and
the slide and between the jack and the bed.
10. Energize the hydraulic jack and apply enough
pressure to support the slide assembly and crank-
shaft.
NOTE: Applied jack pressure should never
exceed 5 percent of press rated tonnage.
11. Place a dial indicator between the slide and the
bed (or bolster) directly beneath the connection
screw. Set the indicator dial to “0” reading.
12. Release jack pressure.
13. The reading on the indicator dial now is the total
bearing clearance (lift).
14. Apply and release jack pressure several times
until consistent readings are obtained.
15. The nominal total bearing clearance for Model 101
OBI/OBS Series presses is shown in the “Total
Bearing Clearance Chart,” below. If the total bear-
ing clearance exceeds, by more than 20 percent,
the maximum allowable clearance for new press-
es, check the individual bearing clearances.
16. If no further checks are necessary, remove the
hydraulic jacks and dial indicators from the press.
G - 3
!
!
!
Содержание IOI
Страница 1: ...Manual No 1010C MINSTER 8952 399 15 00 Service Manual OBI OBS SERIES PRESS MODEL...
Страница 2: ...Manual No 1010C MINSTER 8952 399 15 00 Service Manual OBI OBS SERIES PRESS MODEL...
Страница 9: ......
Страница 25: ......
Страница 51: ......
Страница 63: ......
Страница 85: ...I 8 COMMENTS CORRECTIVE STEPS TAKEN Inspected By Press approved for operation Press NOT approved for operation...
Страница 87: ...I 10 COMMENTS CORRECTIVE STEPS TAKEN Inspected By Press approved for operation Press NOT approved for operation...
Страница 89: ...I 12 COMMENTS CORRECTIVE STEPS TAKEN Inspected By Press approved for operation Press NOT approved for operation...
Страница 90: ...ADDITIONAL COMMENTS I 13...