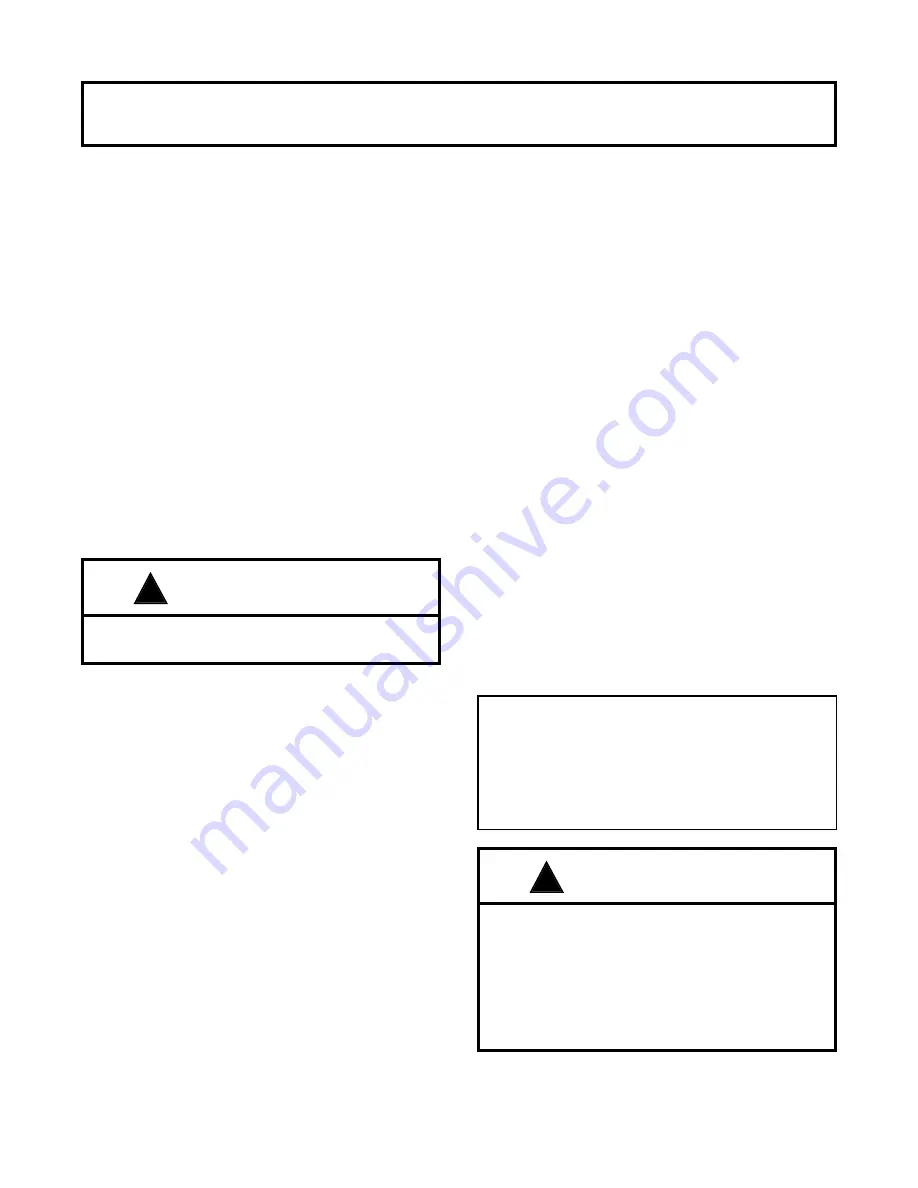
SYSTEM DESCRIPTION
Minster Model 101 OBI/OBS Series presses are
equipped with a recirculating oil lubrication system that
is mounted at the base of the press frame. Its basic
pumping unit consists of a fixed displacement gear
pump which provides lubricant to various lube points on
the press. The pump is driven by a 1/15 horsepower
electric motor through a flexible coupling.
NOTE: Refer to the Lube Schematic (furnished) for spe-
cific information pertaining to the lube system.
SERVICE AND MAINTENANCE
Because of its completely automatic operation, period-
ic checks of the lube system are often either forgotten
or ignored. Such neglect could cause eventual bearing
failure and costly equipment downtime. Maintenance
personnel should make certain that the oil filter is
replaced and the reservoir is cleaned at regular inter-
vals. All lubrication lines, hoses, fittings, valves and
safety switches should be checked on a regular basis to
make certain that they are in good operating condition.
WARNING
DO NOT CYCLE A NEW PRESS UNTIL IT HAS BEEN
PROPERLY LUBRICATED AND TESTED.
Components that comprise the lube portion of the
Model 101 OBI/OBS Series presses recirculating pres-
sure lubrication system are described and illustrated in
this “Press Lubrication” section of the manual. Also
included is service related information such as instruc-
tions for draining and refilling the oil reservoir, recom-
mended procedures for replacing the oil filter, a list of
lubrication areas, types of lubricants to be used and fre-
quency of resupply. Operating and maintenance per-
sonnel should carefully read this section. It is important
that they understand the lubrication system so that it
may be operated correctly and serviced, as necessary,
for continued, efficient operation.
In addition to those functions that relate to normal, daily
operation of the lubrication system, a list of subsystem
check points — items that should be inspected period-
ically — are included in the “Press Inspection Check
List & Maintenance Record” in Section H. Lubrication
system components are included in the comprehensive
press inspection check list so that they may be conve-
niently checked at the same time regularly scheduled
press maintenance checks are performed.
RESERVOIR CAPACITY
Never attempt to operate the press without first check-
ing the lube reservoir to make certain it is filled to the
proper level with an approved lubricant. (See “Filling
And Maintaining Lube Reservoir Oil Level” and “Initial
Lubrication” sections of this manual.)
The lube system oil reservoir capacity for Model 101
OBI/OBS Series press sizes is 1.5 gallons (5.67 liters).
Actual capacity may vary slightly. The semi-transpar-
ent, fiberglass oil reservoir provides a convenient
means for checking lubricant level. The reservoir
should be filled to 1.50” (38 mm) from the top of the
reservoir with an approved lubricant meeting the spec-
ifications of Minster Lubricant No. 1. (See “General
Lubrication Specifications For MINSTER Presses,”
Manual No. 507, for approved lubricants and recom-
mended suppliers.)
FILLING AND MAINTAINING
LUBE RESERVOIR OIL LEVEL
To fill the Model 101 OBI/OBS Series press lube reser-
voir, first turn OFF electrical power to the press. Then
open the filler cap on the top of the lube unit reservoir
(See Figure 1D, page D-3) and pour in Lubricant No. 1,
as necessary, until the oil level is approximately 1.50”
(38 mm) from the top of the reservoir. DO NOT OVER
FILL. Close the filler cap after the oil is at the recom-
mended level.
IMPORTANT: PRE-FILTERING THE LUBE OIL
Oil should always be filtered before being put into
use. New oil is not necessarily clean. Therefore,
when filling the lube reservoir, install a 10 micron oil
filter in the supply line to filter the oil before it enters
the reservoir.
WARNING
USE ONLY LUBRICANTS MEETING THE SPECIFI-
CATIONS OF MINSTER LUBRICANT NO. 1. NEVER
MIX DIFFERENT GRADES OF OIL OR ADD EVEN A
SMALL AMOUNT OF NON-APPROVED LUBRI-
CANT. FAILURE TO OBSERVE THIS PRECAUTION
COULD RESULT IN SEVERE DAMAGE TO THE
PRESS AND/OR IMPROPER OPERATION OF THE
CONTROL VALVES.
D - 2
PRESS LUBRICATION
!
!
Содержание IOI
Страница 1: ...Manual No 1010C MINSTER 8952 399 15 00 Service Manual OBI OBS SERIES PRESS MODEL...
Страница 2: ...Manual No 1010C MINSTER 8952 399 15 00 Service Manual OBI OBS SERIES PRESS MODEL...
Страница 9: ......
Страница 25: ......
Страница 51: ......
Страница 63: ......
Страница 85: ...I 8 COMMENTS CORRECTIVE STEPS TAKEN Inspected By Press approved for operation Press NOT approved for operation...
Страница 87: ...I 10 COMMENTS CORRECTIVE STEPS TAKEN Inspected By Press approved for operation Press NOT approved for operation...
Страница 89: ...I 12 COMMENTS CORRECTIVE STEPS TAKEN Inspected By Press approved for operation Press NOT approved for operation...
Страница 90: ...ADDITIONAL COMMENTS I 13...