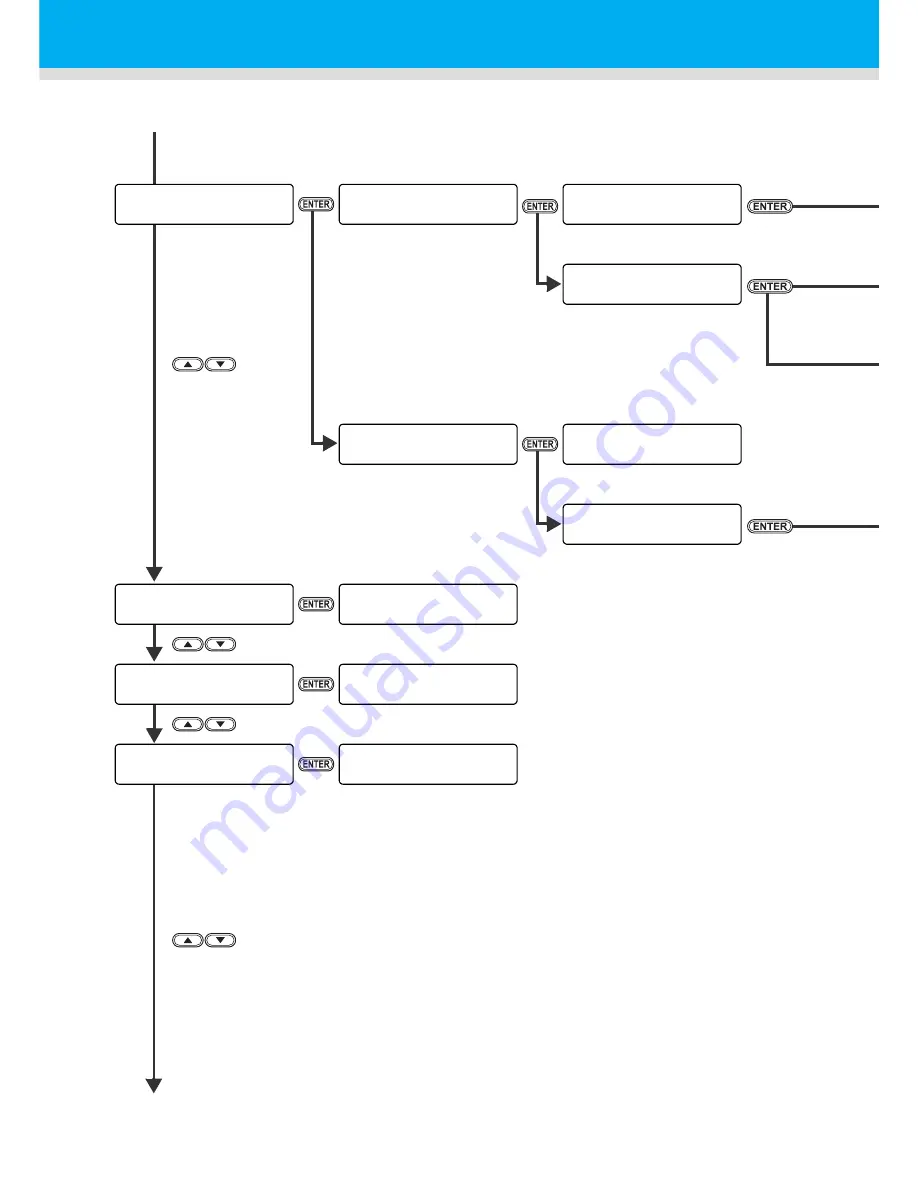
6-16
From P.6-14
HOST / 10 to 200%
S E T UP
F E ED S P E ED
[ EN T ]
F E ED S P E ED
=
HOS T
To P.6-18
S E T UP
V ACUUM
[ EN T ]
V ACUUM
: HOS T
HOST / WEAK / STANDARD /
STRONG
S E T UP
RE F RE SH
[ EN T ]
RE F RE SH
: HOS T
HOST / Lv.3 to Lv.0
S E T UP
UV MODE
[ EN T ]
UV MODE
: P A T T ERN
UV MODE
: HOS T
UV MODE
: MNUA L
UV MODE
: CON T RO L
UV MODE
UV C T R L ARE A : F U L L
UV MODE
UV C T R L ARE A : PR I N T
Содержание UJV500-160
Страница 1: ...MIMAKI ENGINEERING CO LTD URL http eng mimaki co jp D202486 15 Original instructions...
Страница 14: ...xiii...
Страница 76: ...2 42...
Страница 176: ...4 46...
Страница 226: ...6 30...
Страница 228: ...NH FW 1 6 MIMAKI ENGINEERING CO LTD 2015...