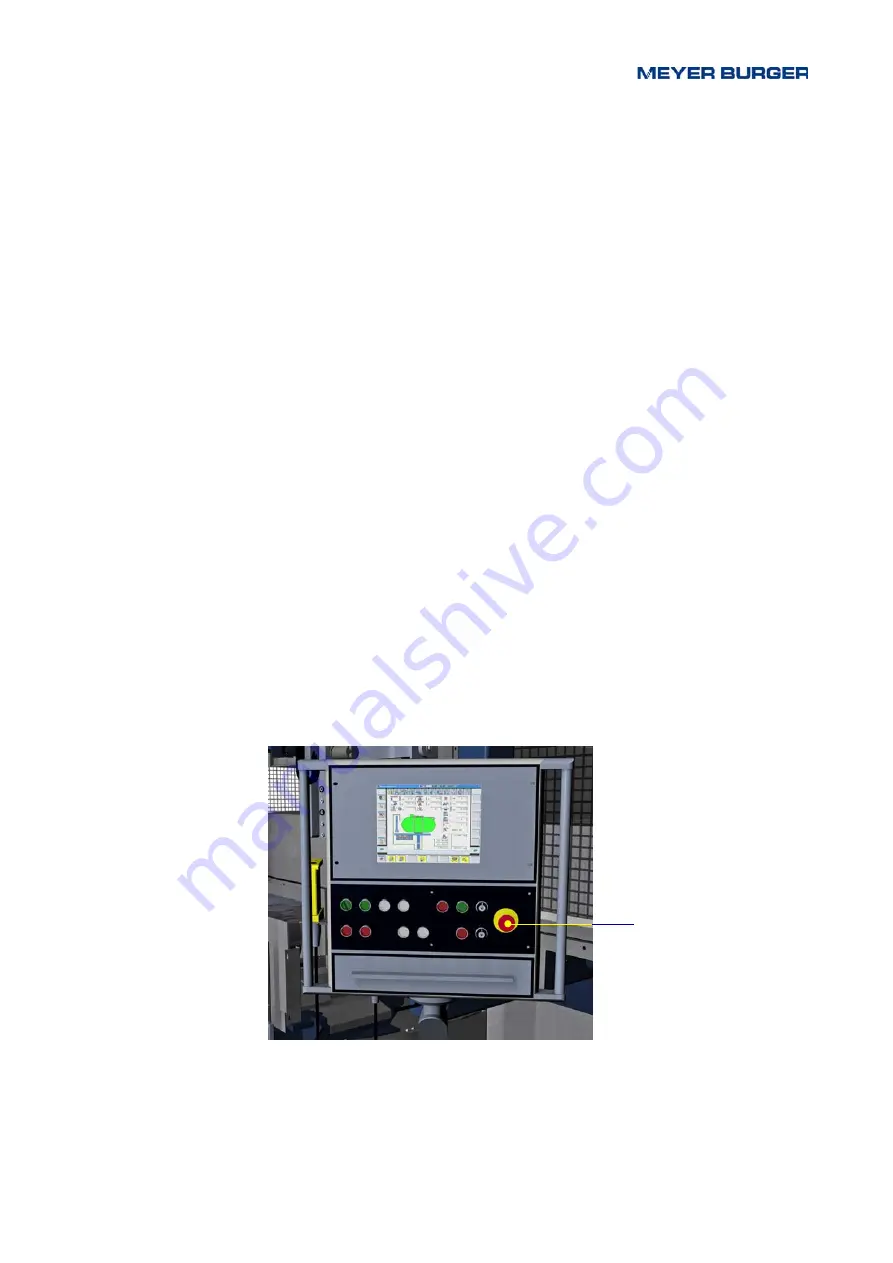
10002683-en-00
23
3.8.5
Standstill monitoring
The movement of both wheels is monitored by the standstill monitoring system.
The locks on the cover and front window are not released until the wheels
have come to a standstill.
3.8.6
Safety clutch
The slide drive of the X-axis is equipped with a safety clutch. In a collision the motor
is decoupled from the safety clutch, i.e. the safety clutch is disengaged.
What to do after disengagement of the safety clutch in accordance with Chap. 13.4
3.8.7
Band break monitoring
If a band breaks, an EMERGENCY SWITCH-OFF is initiated.
3.8.8
Emergency stop
After the emergency stop button has been pressed:
■
the control system remains switched on
■
the fault messages remain stored
■
the release of the regulators is interrupted
■
the axes are switched off
■
the drive motor is switched off
■
band tension remains as it was
■
the hydraulic system is switched off
■
the wheels are decelerated in a controlled manner
(brake on clamping side wheel is switched on after 20 sec.)
■
the coolant supply and return pumps are switched off
Fig. 3-4
Emergency stop button
Legend
1
Emergency stop button
1
Содержание BS 820
Страница 1: ...10002683 en 00 Band Saw BS 820 Manual...
Страница 28: ...28 10002683 en 00 BS 820 Product data 4 3 Layout Fig 4 1 Layout 6503 6356 3755 max 3782...
Страница 51: ...10002683 en 00 51 7 7 Setup...
Страница 60: ...60 10002683 en 00 BS 820 Setup...
Страница 64: ...64 10002683 en 00 BS 820 Cutting...
Страница 78: ...78 10002683 en 00 BS 820 Packing and transport...
Страница 86: ...86 10002683 en 00 BS 820 Repair Service...