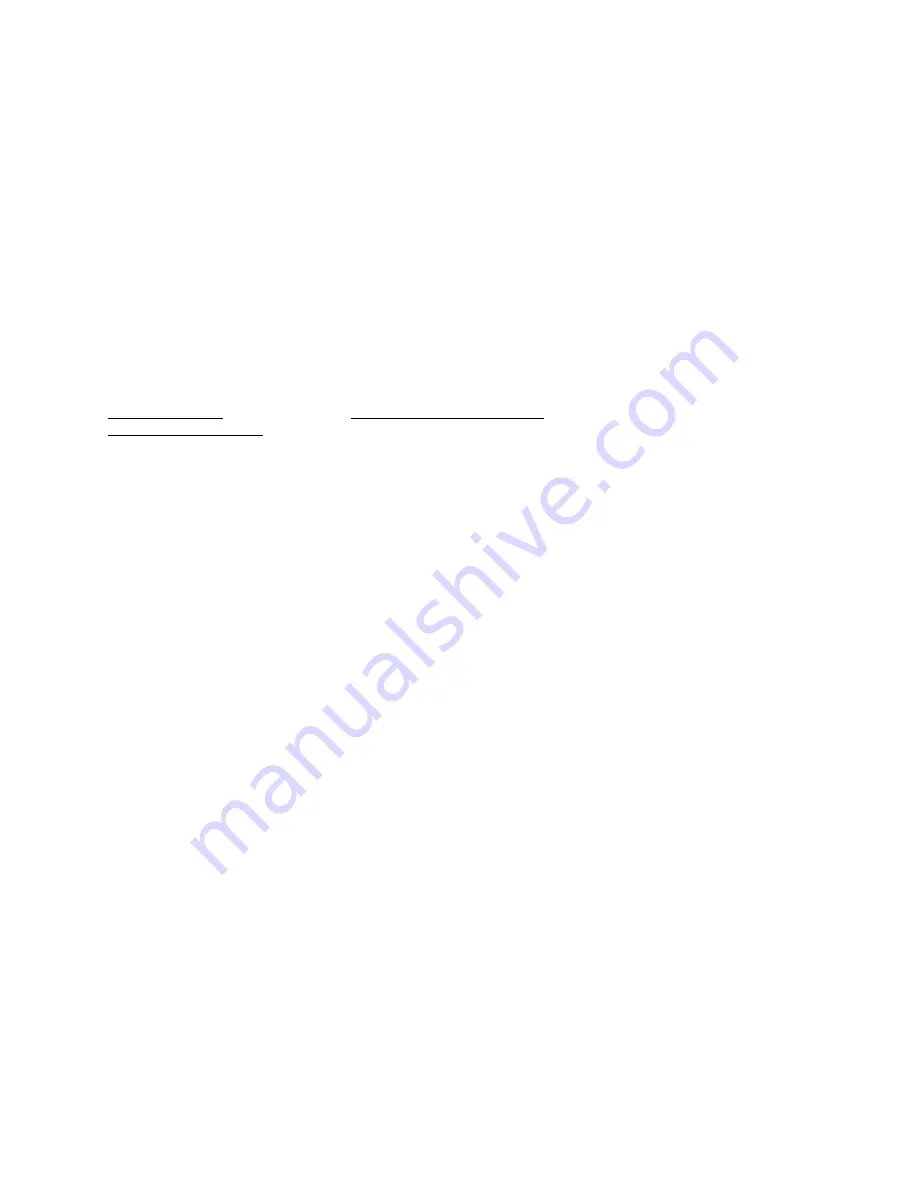
Page 6 of 25
motor leads must be reversed to cure the condition. Turn the controller circuit breaker and isolation switch off and verify that
incoming power on the load side of the controller isolation switch has been disconnected. Then reverse any two of the motor
leads. If there are multiples sets of motor leads, i.e. Part Winding start or Wye-Delta start, then both sets of leads must be
reversed. Be certain to change the same set of wires at the two contactors. Then turn the controller isolation switch and circuit
breaker back on and check for correct rotation of the motor and then follow the procedure below to correct the Phase Reversal
alarm.
If the motor is turning the correct direction but there is a Phase Reversal alarm then this can be corrected as follows. Press the
Config button on the front of the OID. Press the Config (2) button again to access the User Preferences Setup screens. Press the
Up arrow key once. The OID should then read “223 User Preferences – Reversed Phase”. Press the Change/Enter button. The
system will then ask for a password. Enter 1111 and then press enter. Press the Up or Down arrow key to change the setting in
the lower left hand corner of the screen from “No” to “Yes” then press the Change/Enter button. After a few seconds the “Phase
Reversal” LED will reset. Also, press the Silence\ Reset button for approx. 3 seconds to silence the audible alarm.
INPUT/OUTPUT STATUS INDICATOR LIGHTS
Light Emitting Diodes (L.E.D.) lights have been installed on the microprocessor module to indicate the status of each input and
output terminal. Status indication for the standard functions is given below:
Terminal Number
L.E.D. (light) "ON" Indication
(Microprocessor Func #)
(Out 02)
Circuit Breaker Shunt Trip
(Out 03)
Start Contactor relay (if applicable)
(Out 04)
Run Contactor relay
(Out 05)
Start signal to Soft Start (Model MP700 only)
(Out 06)
Power to Soft Start (Model MP700 only)
(In 01)
Emergency Start lever activated
(In 02)
Start Pushbutton
(In 03)
Stop Pushbutton
(In 04)
Start Contactor closed
(In 05)
Run Contactor closed
(In 06)
Transfer Switch position (if applicable)
(In 07)
Transfer Switch ready to transfer (if applicable)
(In 08)
Transfer Switch Emergency Iso Switch Open (if applicable)
a.
AUTOMATIC STARTING TESTS:
1.
Place control in
"Auto"
position.
2.
Bleed off pressure in system until pressure drops below the low set point.
3.
Pump should start automatically and continue to run after pressure rises above the high set point, if arranged for
"Manual"
stop. If arranged for
"Automatic"
stop, pump will continue to run for time set on Auto Stop Timer and
then stop.
4.
Press the
"Stop"
push button to stop the pump.
5.
Repeat tests for each demand switch such as deluge valve (if enabled), remote start, etc.
b.
PERIODIC WEEKLY START TEST:
1.
Pressure must be up and all other demand switches de-activated.
2.
When the current day and time of day matches the settings in System Config screens 107 and 108, the solenoid drain
valve will energize (if enabled and supplied, see screen #108) and the pump will start. It will continue to run for the
amount of time set and then stop automatically.
c.
SETTING PROGRAM WEEKLY TEST TIME:
System Config screen 109 through 112.
d.
REMOTE START SWITCH CIRCUITS:
Field wiring terminals are provided on the controller so that optional remote
start switches such as Remote Pushbutton Stations, Deluge Valve Switch, Fire Alarm Switches, etc., may be used to start the
pump. Two (2) sets of terminals are provided. Terminals #112 and #31 are used for remote manual start push buttons (close
to start). Terminals #111 and #31 are used for remote Deluge Valve Switch or other remote automatic start switches (open to
Содержание MP430 Series
Страница 5: ......
Страница 6: ......
Страница 7: ......
Страница 8: ......
Страница 10: ...Page 2 of 25 THIS PAGE IS BLANK...