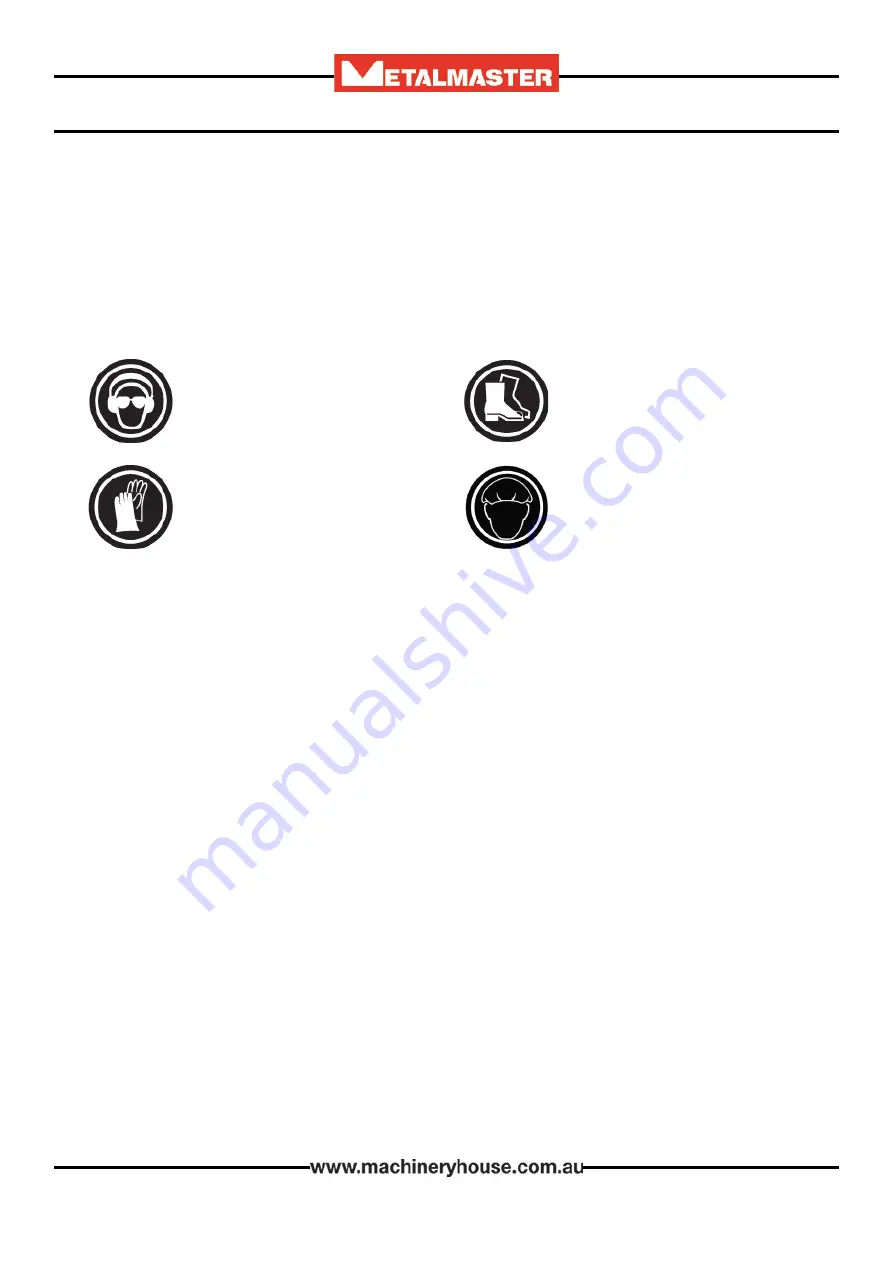
6
OPERATING MANUAL
SAFETY CHECKS BEFORE OPERATING
q
Locate and ensure you are familiar with all machine operations and controls.
q
Take notice of any warning labels on the machine and do not remove them.
q
Ensure all guards are fitted, secure and functional.
q
Ensure working parts are well lubricated and the jaws and fingers free of rust and dirt.
q
Check workspaces and walkways to ensure no slip/trip hazards are present
q
Be aware of other people in the area. Ensure the area is clear before using equipment.
SAFETY CHECKS WHEN OPERATING
q
Operate the machine only if all protective devices and guarding are mounted and effective.
q
Remove the pan brake fingers that are in the way. Use only the pan brake fingers required to
make the bend.
q
Check that the material to be bent is the correct thickness.
q
Ensure the pan brake fingers that are not removed for an operation are securely seated and
firmly tightened before the machine is used.
q
Ensure your fingers and limbs are clear before operating the pan brake.
q
Lower finger clamps to work. Do not drop.
q
Check workpiece is secure.
q
Keep clear of moving counterweight (where fitted).
POTENTIAL HAZARDS AND INJURIES
q
Sharp edges and burrs.
q
Squash/crush and pinch points.
q
Impact from counterweight.
2.1 SAFETY REQUIREMENTS
Safety glasses must be worn at
all times in work areas. Earmuffs
should be worn if the work area is
noisy.
Sturdy footwear must be worn at
all times in work areas.
Gloves must be worn when han-
dling the material..
Long and loose hair must be con-
tained with a net or under a hat
2. IMPORTANT INFORMATION
The purpose of the safety section of this manual is to inform operators and maintenance
personnel of the precautions to be taken while operating or servicing the machine.
The following are a few basic guidelines to follow, but as with any type of machinery good judg-
ment and a safe attitude should be applied at all times.