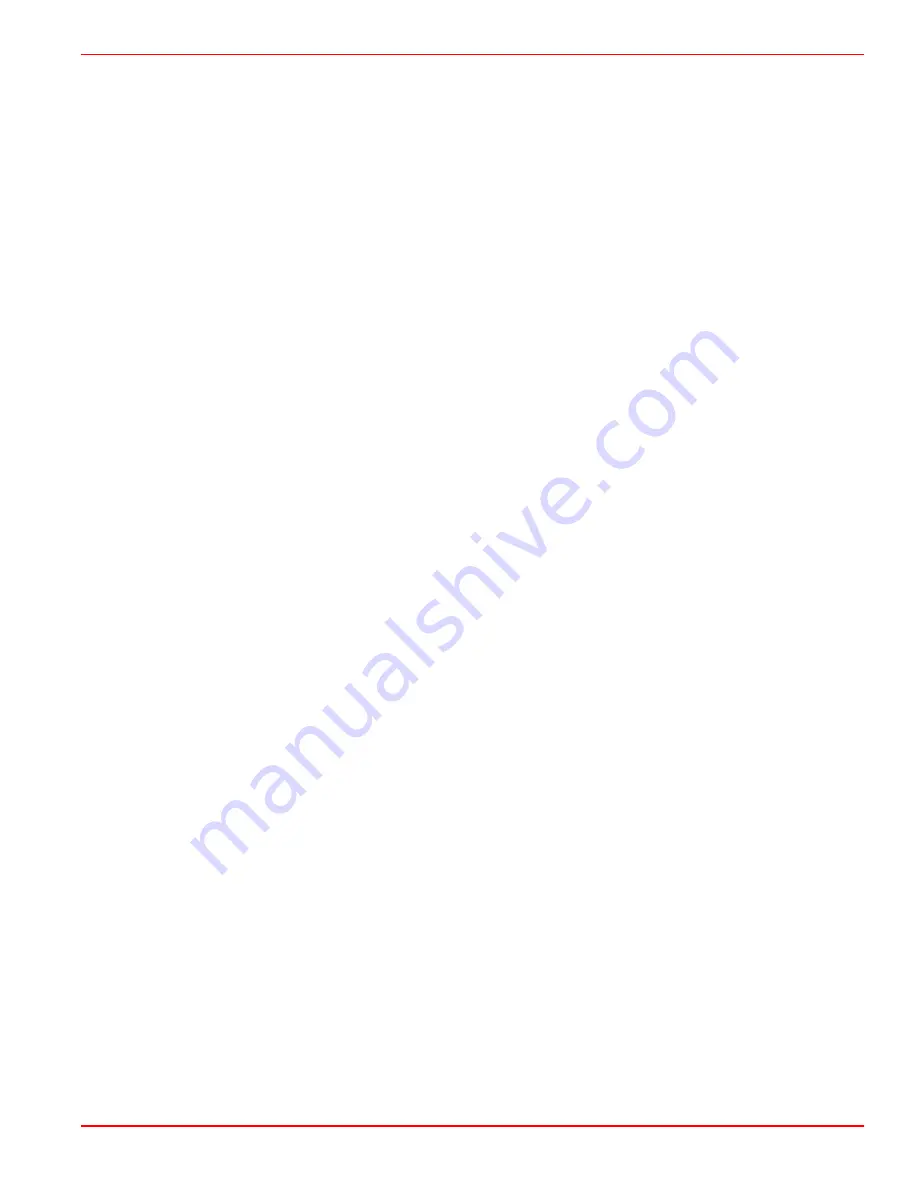
Jet Installation
90-8M0050731 MAY 2011
Page 1D-9
4. Fuel line should be installed free of stress and firmly secured to prevent vibration and/or chafing.
5. Sharp bends in fuel line should be avoided.
6. A flexible fuel line must be used to connect fuel line to engine fuel pump to absorb deflection when engine is running.
7. A primer bulb is not necessary with this application. If a primer bulb is used, it must be U.S. Coast Guard approved for inboard
engine installations.
8. The vapor separator must be vented to fuel tank. The vent hose must comply with U.S. Coast Guard/ABYC regulations.
Instrumentation
NOTE: Check the charging capability of the engine. The electrical load of the boat should not exceed this capacity.
We recommend the use of Mercury Precision or Quicksilver instrumentation and wiring harnesses. Refer to
Mercury Precision
Parts Accessories Guide
for selection.
If other than Mercury Precision or Quicksilver electrical accessories are to be used, it is good practice to use waterproof ignition
components (ignition switch, lanyard stop switch, etc.). A typical jet boat of this nature will see water splashed on these
components. Therefore, precautions must be taken to avoid ignition failure due to shorting out of ignition components.
A warning horn must be incorporated in the wiring harness (see wiring diagram) to alert the user of an overheat, low oil condition,
or oil pump failure.
IMPORTANT: If a warning horn system is not installed by the boat manufacturer, Mercury Marine will not honor any warranty
claims for engine damage as a result of overheating or lack of engine oil.
Route instrumentation wiring harness back to the engine, making sure that the harness does not rub or get pinched. If an extension
harness is required, be sure to secure connection properly. Fasten harnesses to the boat at least every 460 mm (18 in.) using
appropriate fasteners.
Remote Control and Cables
The remote control must provide the following required features:
•
Start in gear protection
•
Neutral RPM limit at 2000 RPM. This applies to dual lever remote controls as well as single lever remote controls.
•
High strength mechanism to accommodate loads transmitted to the remote control
•
Shift cable travel of 76 mm ± 3 mm (3 in. ± 1/8 in.)
•
Ability to use 40 series shift cable
The remote control must meet the above criteria as well as the design criteria outlined in the ABYC manual pertaining to Mini‑Jet
Boats (Standard P‑23).
Shift Cable
The shift cable to be used must meet the following criteria:
•
40 series shift cable
•
40 series bulkhead fitting at output end
•
Allow for a minimum of 76 mm (3 in.) of travel
•
A means of attaching and locking the cable to the shift cable bracket (provided)
•
Cable end at pump must allow for a 1/4 inch clevis pin and cotter pin (all provided) to connect cable to the reverse gate
•
Protected against water intrusion and/or corrosion as the cable end (at the pump) is submersed in water with the boat at rest
The shift cable end (at the pump) is submersed in water. It should be sealed against water intrusion, protected against corrosion,
and be able to withstand the shift loads imparted on it by the reverse gate.
Follow shift cable adjustment procedure for proper adjustment.
Throttle Cable
The throttle cable must have one end compatible with the control box. The other end must have Mercury style connectors.
Follow throttle cable adjustment procedures for proper adjustment.
Steering Helm and Cable
The steering helm must limit steering cable travel to 88.9 mm ± 2.5 mm (3‑1/2 in. ± 1/8 in.).
Steering Cable
The steering cable to be used must meet the following criteria:
•
60 series steering cable
•
60 series bulkhead fitting at output end
Содержание 200 OptiMax Jet Drive
Страница 5: ...Page iv ...
Страница 30: ...General Information Notes 90 8M0050731 MAY 2011 Page 1C 5 ...
Страница 43: ...General Information Notes Page 1C 18 90 8M0050731 MAY 2011 ...
Страница 84: ...Ignition Notes 90 8M0050731 MAY 2011 Page 2A 3 ...
Страница 89: ...Ignition Page 2A 8 90 8M0050731 MAY 2011 Electrical Plate Engine Harness 44731 1 2 3 4 5 6 ...
Страница 147: ...Charging and Starting System Notes Page 2B 36 90 8M0050731 MAY 2011 ...
Страница 153: ...Timing Synchronizing and Adjusting Notes Page 2C 6 90 8M0050731 MAY 2011 ...
Страница 156: ...Fuel Pump Notes 90 8M0050731 MAY 2011 Page 3A 3 ...
Страница 177: ...Direct Fuel Injection Page 3B 14 90 8M0050731 MAY 2011 Fuel Hose Components 4256 3 8 1 8 8 5 8 8 8 8 8 6 7 4 4 2 ...
Страница 179: ...Direct Fuel Injection Page 3B 16 90 8M0050731 MAY 2011 Air Hose Components 4257 1 1 2 3 6 4 5 7 8 9 ...
Страница 245: ...Direct Fuel Injection Notes Page 3B 82 90 8M0050731 MAY 2011 ...
Страница 248: ...Oil Injection Notes 90 8M0050731 MAY 2011 Page 3C 3 ...
Страница 261: ...Oil Injection Notes Page 3C 16 90 8M0050731 MAY 2011 ...
Страница 275: ...Powerhead Page 4A 10 90 8M0050731 MAY 2011 Exhaust Manifold and Exhaust Plate 7 44904 1 2 3 4 5 6 8 10 9 7 ...
Страница 277: ...Powerhead Page 4A 12 90 8M0050731 MAY 2011 Cylinder Head 14 44903 1 2 3 3 4 5 6 7 8 9 10 ...
Страница 283: ...Powerhead Page 4A 18 90 8M0050731 MAY 2011 Ref No Qty Description Torque Nm lb in lb ft 41 1 Hose 42 1 Worm gear clamp ...
Страница 326: ...Powerhead 90 8M0050731 MAY 2011 Page 4A 61 Starboard Side Oil Hose Routing 45579 ...
Страница 327: ...Powerhead Page 4A 62 90 8M0050731 MAY 2011 Port Side Oil Hose Routing 45580 ...
Страница 339: ...Powerhead Notes Page 4A 74 90 8M0050731 MAY 2011 ...
Страница 346: ...Cooling Notes 90 8M0050731 MAY 2011 Page 4B 7 ...
Страница 349: ...Cooling Notes Page 4B 10 90 8M0050731 MAY 2011 ...
Страница 367: ...Pump Unit Page 5A 18 90 8M0050731 MAY 2011 Ref No Qty Description Torque Nm lb in lb ft 41 1 Hose 42 1 Worm gear clamp ...