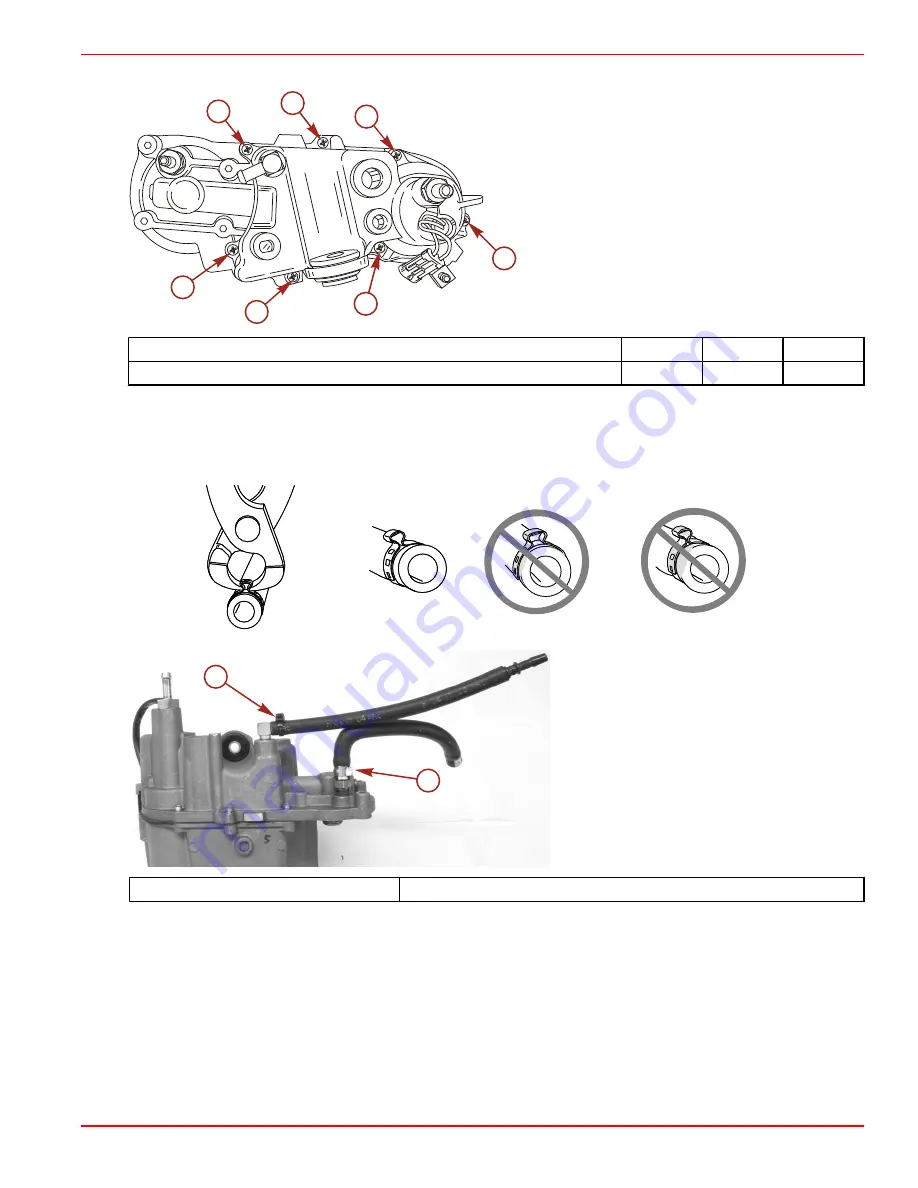
Direct Fuel Injection
90-8M0050731 MAY 2011
Page 3B-45
8. Install the VST cover onto the VST tank and secure with seven screws. Tighten the screws to the specified torque.
a -
Screw (7)
Description
Nm
lb‑in.
lb‑ft
Screw (8‑32 x 0.750) (7)
3.5
31
9. Install the vent hose and secure the hose with a cable tie.
10. Install a 18.3 mm hose clamp onto the lift pump hose.
11. Install the lift pump hose onto the VST cover. Secure the hose with a 18.3 mm hose clamp using a hose clamp tool.
IMPORTANT: Use tool 91‑803146T or Snap‑On equivalent YA3080 to crimp the full circle hose clamp. Using a different tool
could result in a crimp that is too loose or too tight. Do not use a screw type hose clamp as it may damage the hose.
3924
a -
Cable tie
b -
18.3 mm hose clamp
Hose Clamp Tool Kit
91‑803146A04
a
a
a
a
a
a
a
16050
a
b
32668
Содержание 200 OptiMax Jet Drive
Страница 5: ...Page iv ...
Страница 30: ...General Information Notes 90 8M0050731 MAY 2011 Page 1C 5 ...
Страница 43: ...General Information Notes Page 1C 18 90 8M0050731 MAY 2011 ...
Страница 84: ...Ignition Notes 90 8M0050731 MAY 2011 Page 2A 3 ...
Страница 89: ...Ignition Page 2A 8 90 8M0050731 MAY 2011 Electrical Plate Engine Harness 44731 1 2 3 4 5 6 ...
Страница 147: ...Charging and Starting System Notes Page 2B 36 90 8M0050731 MAY 2011 ...
Страница 153: ...Timing Synchronizing and Adjusting Notes Page 2C 6 90 8M0050731 MAY 2011 ...
Страница 156: ...Fuel Pump Notes 90 8M0050731 MAY 2011 Page 3A 3 ...
Страница 177: ...Direct Fuel Injection Page 3B 14 90 8M0050731 MAY 2011 Fuel Hose Components 4256 3 8 1 8 8 5 8 8 8 8 8 6 7 4 4 2 ...
Страница 179: ...Direct Fuel Injection Page 3B 16 90 8M0050731 MAY 2011 Air Hose Components 4257 1 1 2 3 6 4 5 7 8 9 ...
Страница 245: ...Direct Fuel Injection Notes Page 3B 82 90 8M0050731 MAY 2011 ...
Страница 248: ...Oil Injection Notes 90 8M0050731 MAY 2011 Page 3C 3 ...
Страница 261: ...Oil Injection Notes Page 3C 16 90 8M0050731 MAY 2011 ...
Страница 275: ...Powerhead Page 4A 10 90 8M0050731 MAY 2011 Exhaust Manifold and Exhaust Plate 7 44904 1 2 3 4 5 6 8 10 9 7 ...
Страница 277: ...Powerhead Page 4A 12 90 8M0050731 MAY 2011 Cylinder Head 14 44903 1 2 3 3 4 5 6 7 8 9 10 ...
Страница 283: ...Powerhead Page 4A 18 90 8M0050731 MAY 2011 Ref No Qty Description Torque Nm lb in lb ft 41 1 Hose 42 1 Worm gear clamp ...
Страница 326: ...Powerhead 90 8M0050731 MAY 2011 Page 4A 61 Starboard Side Oil Hose Routing 45579 ...
Страница 327: ...Powerhead Page 4A 62 90 8M0050731 MAY 2011 Port Side Oil Hose Routing 45580 ...
Страница 339: ...Powerhead Notes Page 4A 74 90 8M0050731 MAY 2011 ...
Страница 346: ...Cooling Notes 90 8M0050731 MAY 2011 Page 4B 7 ...
Страница 349: ...Cooling Notes Page 4B 10 90 8M0050731 MAY 2011 ...
Страница 367: ...Pump Unit Page 5A 18 90 8M0050731 MAY 2011 Ref No Qty Description Torque Nm lb in lb ft 41 1 Hose 42 1 Worm gear clamp ...