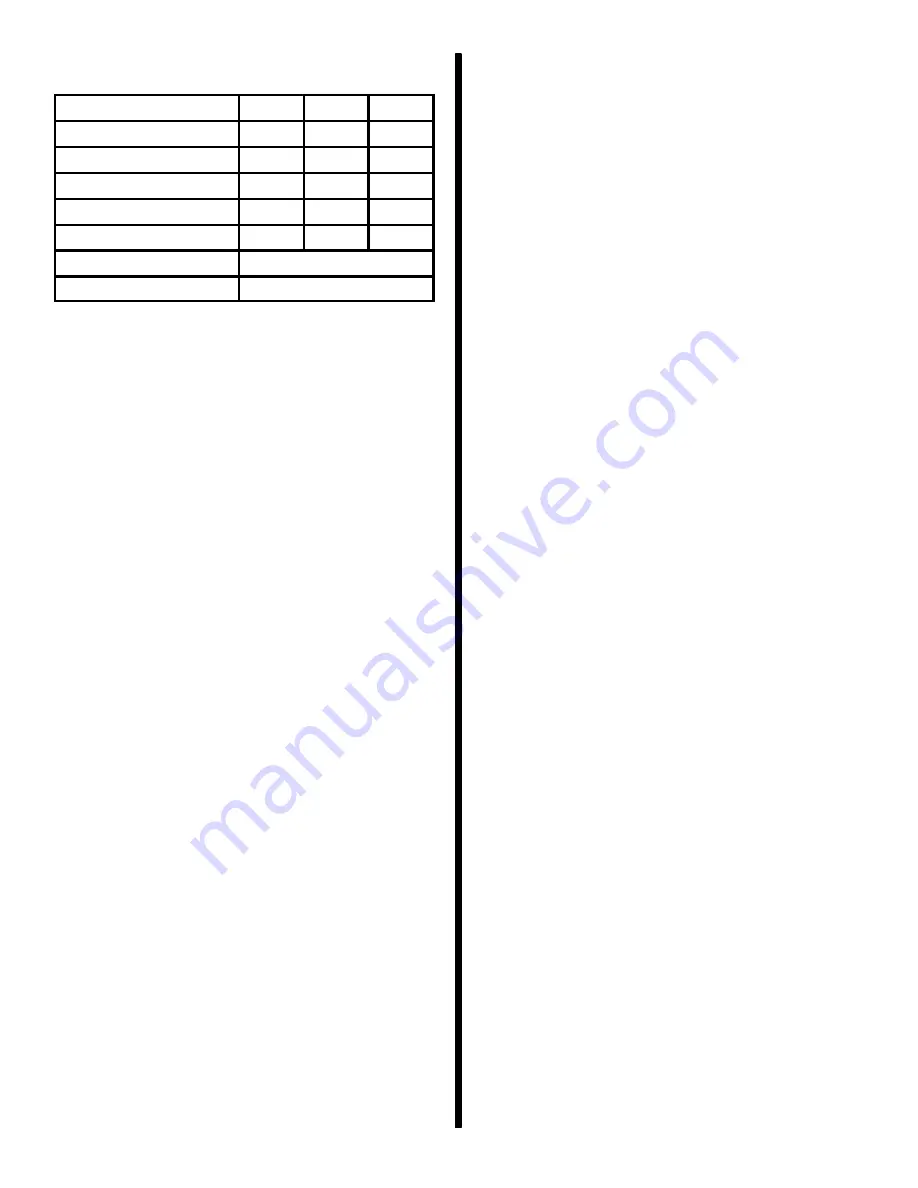
4C - 20 - CHARGING SYSTEM
90-816462 2-695
Torque Specifications
Fastener Location
Lb In.
Lb. Ft.
N·m
Housing Screws
55
6.5
Pulley Nut
42
58
Front Bearing Screws
Alternator Mount
35
48
Adjustment Bolt
16
28
All Other Fasteners
Tighten Securely
V-Belt Tension (Note)
Depress 1/2 In. (13mm)
NOTE: Depress belt with thumb at midway point be-
tween circulating pump pulley and alternator.
Description
The alternator has a rotor, which is supported in two
end frames by ball bearings, and is driven by a pulley
at approximately twice engine speed. The rotor con-
tains a field winding that is enclosed between two
multiple-finger pole pieces. The ends of the field
winding are connected to two brushes (mounted in
the rear end frame) which make continuous sliding (or
slipping) contact with the slip rings. The current (flow-
ing through the field winding) creates a magnetic field
that causes the adjacent fingers of the pole pieces to
become alternate north and south magnetic poles.
A 3-phase stator is mounted directly over the rotor
pole pieces and between two end frames. It consists
of three windings wound 120 degrees electrically
out-of-phase on the inside of a laminated core. The
windings are all connected together on one end, while
the other ends are connected to a full-wave rectifier
bridge.
The rectifier bridge contains six rectifiers which are
arranged so that current flows from ground, through
the stator and to the output terminal, but not in the op-
posite direction.
When current is supplied to the rotor field winding,
and the rotor is turned, the movement of the magnetic
fields created induces an alternating current into the
stator windings. The rectifier bridge then changes this
alternating current to direct current which appears at
the output terminal. A diode trio also is connected to
the stator windings to supply current to the regulator
and the rotor field during operation.
Voltage output of the alternator is controlled by regu-
lating the current supplied to the rotor field. This is ac-
complished by a transistorized voltage regulator that
senses the voltage at the battery and regulates the
field current to maintain alternator voltage within pre-
scribed limits for properly charging the battery. Cur-
rent output of the alternator does not require regula-
tion, as maximum current output is self-limited by the
design of the alternator. As long as the voltage is reg-
ulated within the prescribed limits, the alternator can-
not produce excessive current. A cut-out relay in the
voltage regulator also is not required, as the rectifier
diodes (which allow current to flow in one direction
only) prevent the battery from discharging back
through the stator.
Due to the lack of residual magnetism in the rotor pole
pieces, a small amount of current must be supplied to
the rotor field to initially start the alternator charging.
This is accomplished by means of an excitation circuit
in the regulator which is connected to the ignition
switch. Once the alternator begins to produce output,
field current is supplied solely by the diode trio, as ex-
plained, preceding.
The alternator also is equipped with a fan (mounted
on the rotor shaft) which induces air flow through the
alternator to remove the heat created by the rectifiers
and stator. A capacitor protects the rectifier system
from high voltages and suppresses radio noise.
Precautions
The following precautions MUST BE observed when
working on the alternator system. Failure to observe
these precautions may result in serious damage to
the alternator or alternator system.
1. DO NOT attempt to polarize the alternator.
2. DO NOT short across or ground any of the termi-
nals on the alternator, except as specifically in-
structed in the “Troubleshooting Tests.”
3. NEVER disconnect the alternator output lead or
battery cables when the alternator is being driven
by the engine.
4. NEVER disconnect regulator lead from alternator
regulator terminal when the alternator is being
driven by the engine.
5. ALWAYS remove negative (–) battery cable from
battery before working on alternator system.
6. When installing battery, BE SURE to connect the
positive (+) battery cable to the positive (+) bat-
tery terminal and the negative (–) (grounded) bat-
tery cable to negative (–) battery terminal.
7. If a charger or booster battery is to be used, BE
SURE to connect it in parallel with existing battery
(positive to positive; negative to negative).
Содержание 13
Страница 1: ...13 Printed in U S A 90 816462 2 695 1995 Brunswick Corporation GM 4 Cylinder MARINE ENGINES ...
Страница 2: ...90 816462 2 695 0 ...
Страница 7: ...1 A IMPORTANT INFORMATION GENERAL INFORMATION 72000 ...
Страница 15: ...1 B 50617 IMPORTANT INFORMATION MAINTENANCE ...
Страница 36: ...1 C IMPORTANT INFORMATION TROUBLESHOOTING ...
Страница 74: ...2 A 50633 REMOVAL AND INSTALLATION 4 CYL ALPHA ONE DRIVE ...
Страница 88: ...3 A 26790 ENGINE 181 CID 3 0L 4 CYLINDER GM ENGINE ...
Страница 137: ...4 A 72079 ELECTRICAL SYSTEMS STARTING SYSTEM ...
Страница 170: ...4 B 71855 ELECTRICAL SYSTEMS IGNITION SYSTEM ...
Страница 197: ...ELECTRICAL SYSTEMS CHARGING SYSTEM 4 C 72078 ...
Страница 237: ...4 D 72747 ELECTRICAL SYSTEMS INSTRUMENTATION ...
Страница 250: ...4 E 72938 ELECTRICAL SYSTEMS WIRING DIAGRAMS ...
Страница 264: ...5 A FUEL SYSTEM FUEL PUMP ...
Страница 271: ...5 B 72681 FUEL SYSTEM MERCARB 2 BARREL CARBURETOR ...
Страница 300: ...6 A 50628 COOLING SYSTEM SEAWATER COOLED MODELS ...
Страница 309: ...6 B 73665 COOLING SYSTEM CLOSED COOLING MODELS ...
Страница 325: ...C 6 EXHAUST SYSTEM MANIFOLD ...
Страница 331: ...7 A 71317 POWER STEERING PUMP ...