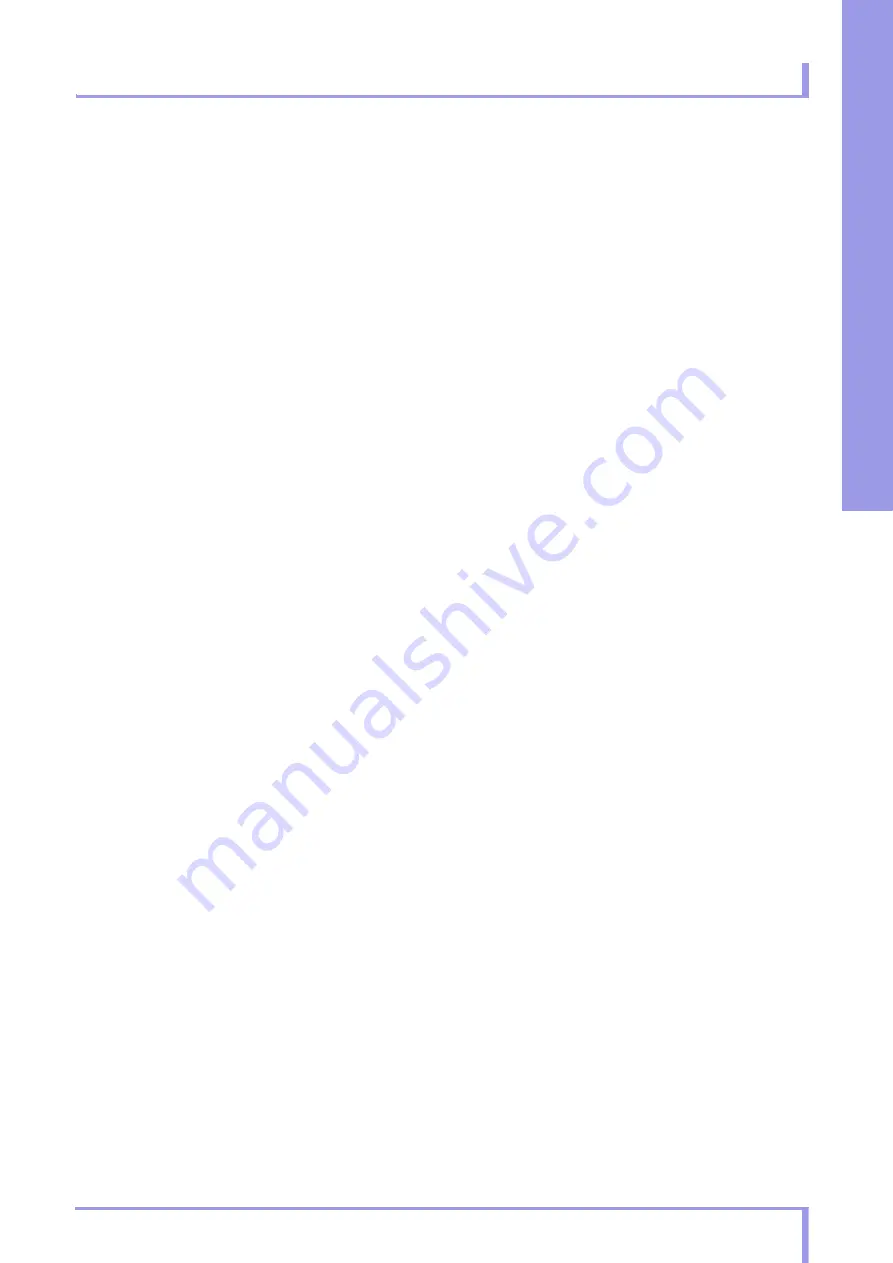
Bodyshell components
Body
135
Introduction of the New E-Class, Model Series 212 Sedan
b
All the components of the bodywork have been rede-
signed for model series 212.
The most important features considered in the devel-
opment of the bodyshell of the new E-Class include:
• Further improvements in the rigidity and strength
of the passenger cell
• Specifically developed deformation zones in the
front and rear end structures
• Ease of repair due to detachable front and rear end
assemblies with a simultaneous reduction in the
weight through the use of an extruded aluminum
section (at the front) and high-strength steel (at the
rear)
• Good installation conditions for drive assemblies
and the front axle thanks to the bolted frame-type
integral support
• The use of MIG soldering means that MAG weld
seams can be dispensed with completely. This has
significantly improved the quality of manufacture
and resistance to corrosion
• The torsional stiffness of the bodyshell has been
increased by 31%
• The proportion of high-strength steel sheet in the
bodyshell has risen from 47% to 72% by weight,
with newly developed steel grades being
increasingly used
Sheet steel was selected as the material for the vast
majority of the bodyshell. The front fenders, the
engine hood and the trunk lid are made of aluminum.
The proportion of aluminum in the bodyshell is there-
fore 8% by weight.
As in model series 204, a high-strength steel frame-
type integral support holding the front axle, steering
and engine is bolted onto the front longitudinal
members.
The spare tire well is made of glass fiber matting-rein-
forced thermoplastics (GMT).
Front end
The front structure of model series 212 is a front end
assembly mounted on the vehicle, which consists of:
• An extruded aluminum section
• A single-part aluminum crash box connecting the
front longitudinal members
• A multi-piece framework of aluminum sheet for
holding the headlamps, the bumper, the washer
fluid reservoir and the engine hood catches, as well
as two supports made of fiber-reinforced plastic
The entire front end assembly is bolted to the front
end structure, as are the individual components of the
front end assembly to each other. If any parts are
damaged, this makes it possible to replace them inex-
pensively and with no welding required.
Passenger cell
The core of the body safety concept is the high-
strength passenger cell in the form of a safety cage.
Its high strength under the stresses of an accident
(frontal, side-on and rear-end collisions as well as roll-
overs) is primarily due to:
• The increased use of high-strength, modern high-
strength, ultra high-strength and heat-formed ultra
high-strength sheet steel and panels with
graduated wall thicknesses
• Components and structural zones susceptible to
heavy loads in accidents which incorporate
materials and sheet thicknesses designed to resist
these loads
• Optimized shapes and cross sections
– This printout will not be recorded by the update service. Status: 01 / 2009 –