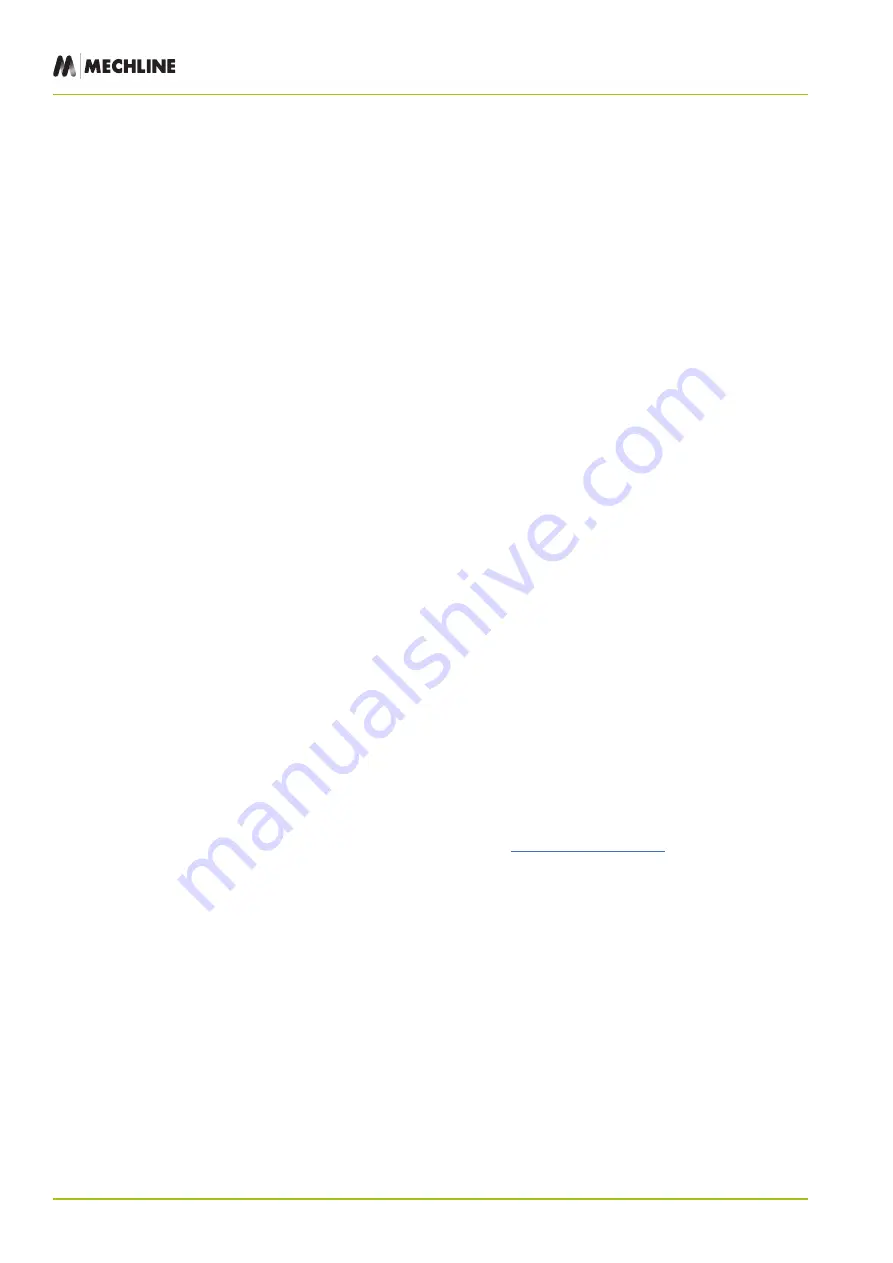
Air & Surface Steriliser System
REVISION: 04/2020 | page 14 of 16 INSTALLATION & OPERATING MANUAL
The US OSHA [Occupational Safety Health Act] website cites several ACGIH (American Conference of Governmental
Industrial Hygienists) guidelines for ozone in the workplace:
• 0.2ppm for no more than 2 hours exposure
• 0.1ppm for 8 hours per day exposure doing light work
• 0.08ppm for 8 hours per day exposure doing moderate work
‘Fresh Air’ – Ozone level 0.013ppm
After a Thunderstorm – Ozone levels measured between 0.3 and 0.05ppm
HyGenikx units – Sized for appropriate areas – Ozone levels 0.03ppm [Max 0.04ppm].
[Kiel Laboratories Germany. ISO Sensory / Odour Test. ISO Audited].
HyGenikx units, will create ozone enriched areas, less concentrated than after a thunderstorm.
There has never been a known proven health issue from any HyGenikx UV devices that produces trace ozone.
Other devices that use a ceramic disc and electrical charge system [Corona discharge] known as Ozone Generators
can produce massive amounts of ozone also produce nitrous oxide another greenhouse gas. HyGenikx is not an
ozone generator and the UV catalytic reaction does not produce these gases. Ozone produced by UV is often
referred to as ‘Clean Ozone’.
9.4.10 How do you install a unit?
Units must always be vertically installed with the logo and cable at the top of the unit. The bottom of the unit
should be at a minimum height of 1.8m AFFL. Air is circulated throughout the area via thermal convection and
incorrect installation will reduce performance. Please follow enclosed instructions. Refer to Chapters 5 and 6.
9.4.11 Where do you install a unit?
Locating the unit close to extraction systems or open windows will vastly reduce performance as sanitising air will
be prevented from circulating correctly. Always be conscious of movement of air throughout the room. Location
close to incoming ventilation (air input) will assist air from the unit in circulating throughout the environment.
Avoid installing directly within a cooking zone where levels of heat and grease are elevated.
In areas of lower air circulation, installing the unit as close as is practical to the strong odour, or contamination
source, is recommended (i.e. next to food storage in cold store, above preparation areas in kitchen, next to urinals
or toilets in a washroom or above locker areas in changing room). Air from the unit will disperse throughout, but
this allows the key areas to be treated first.
9.4.12 Why are there different unit variations and lamp options?
One size does not fit all. We supply several product variations to ensure the best results in each environment and
area size (a washroom presents a very different challenge to a cold store). Anything in a food environment must be
“food safe” so units for these areas have a specialist food safe sheath for the lamp.
Different units are set up for different environments and their anticipated bacteria levels and outputs vary.
It is important to understand that units need to be suitably sized to ensure correct operation.
If you are unsure
how to size the HyGenikx unit please refer to chapter 8, or email
9.4.13 What do the numbers and codes refer to on the unit?
For the food service models the numbers represent the square meterage the unit is set up for, (length x width -
height is not included in this calculation as the sanitising air will fall to ground level where the highest
contamination is present).
“W” or “T” is simply a colour choice option our White or Titanium finish to best suit your personal preference.
“F” indicates a product suitable for a food safe environment as the lamp is sheathed (shatterproof).
“S” is a standard general use product suitable for most areas, including washrooms and changing rooms.
Standard lamps are not shatterproof.
“R” is refuse, a higher output variation for areas with strong odours. “R” versions should not be used in areas of
general occupation.
“O” is a model for use in constantly occupied areas such as offices with low ventilation and air movement.
9.4.14 How often do the battery and lamp need to be changed?
Lamp and battery should be replaced every 12 months. The unit has a reminder system built-in with a flashing
indicator followed by an audible alarm to ensure this does not get missed. Please refer to Chapter 7 for full lamp
and battery replacement instructions.