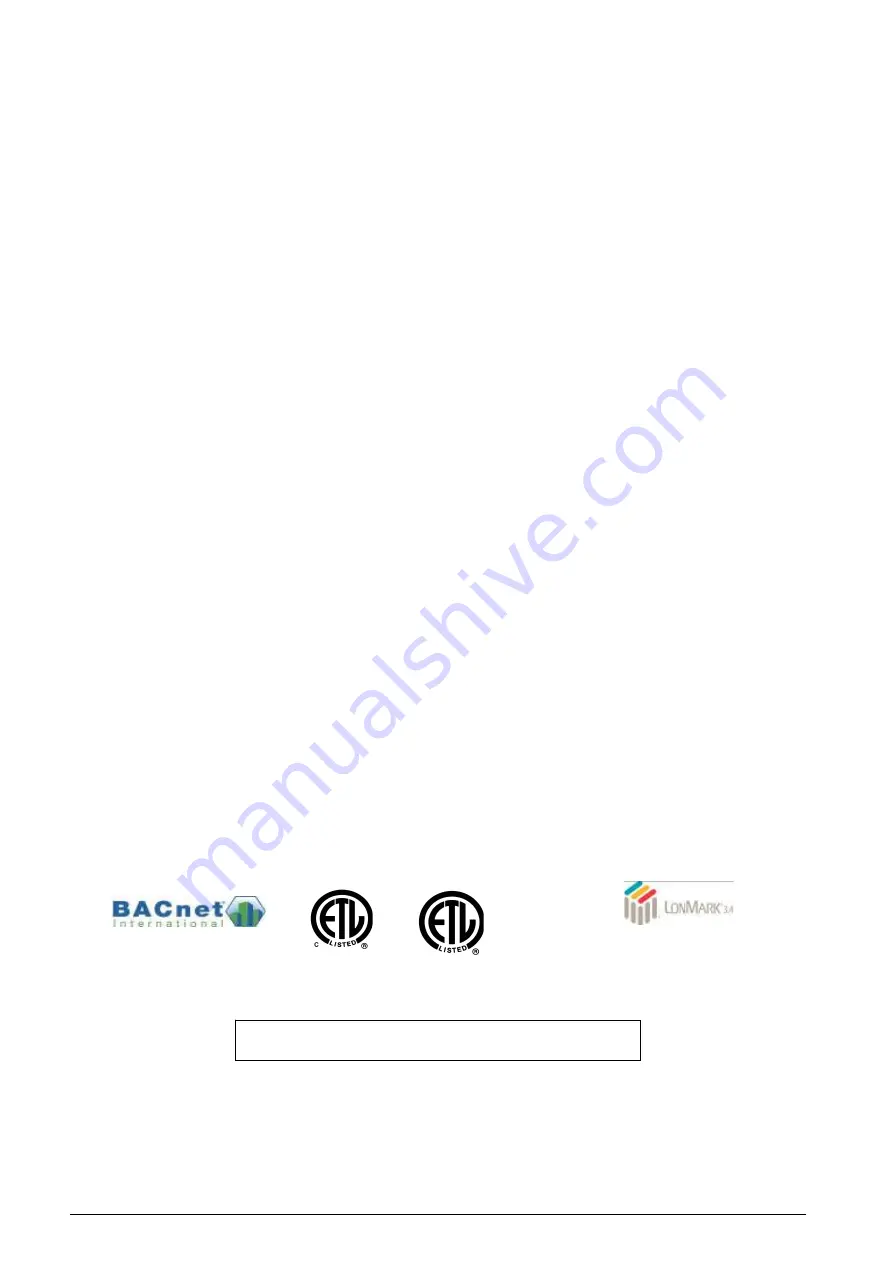
2
KOMAC00607-09EN
Table of Contents
INTRODUCTION.......................................... 3
OPERATING LIMITS:................................. 4
CONTROLLER FEATURES ....................... 4
GENERAL DESCRIPTION ......................... 5
C
ONTROL
P
ANEL
L
AYOUT
............................ 5
P
OWER
P
ANEL
L
AYOUT
................................ 6
E
CONOMIZER
C
OMPONENTS
......................... 7
CONTROLLER DESCRIPTION................. 9
H
ARDWARE
S
TRUCTURE
.............................. 9
S
YSTEM
A
RCHITECTURE
............................. 10
SEQUENCE OF OPERATION .................. 11
CONTROLLER OPERATION .................. 14
M
ICRO
T
ECH
III
I
NPUTS
/O
UTPUTS
.............. 14
E
XTENSION
I/O
C
OMPRESSOR
#1
TO
#3...... 15
I/O
EXV
C
IRCUIT
#1
TO
#3 ........................ 15
E
XTENSION
I/O
F
AN
M
ODULE
C
IRCUIT
#1
&
2 ................................................................. 16
E
XTENSION
I/O
F
AN
M
ODULE
C
IRCUIT
#3 . 16
E
XTENSION
I/O
U
NIT
A
LARM
&
L
IMITING
(POL)......................................................... 16
S
ETPOINTS
.................................................. 17
UNIT FUNCTIONS ..................................... 21
C
ALCULATIONS
.......................................... 21
U
NIT
E
NABLE
............................................. 21
U
NIT
M
ODE
S
ELECTION
.............................. 21
U
NIT
C
ONTROL
S
TATES
.............................. 22
U
NIT
S
TATUS
.............................................. 23
I
CE
M
ODE
S
TART
D
ELAY
........................... 23
E
VAPORATOR
P
UMP
C
ONTROL
................... 23
N
OISE
R
EDUCTION
..................................... 24
L
EAVING
W
ATER
T
EMPERATURE
(LWT)
R
ESET
......................................................... 24
U
NIT
C
APACITY
C
ONTROL
.........................26
U
NIT
C
APACITY
O
VERRIDES
.......................28
CIRCUIT FUNCTIONS ..............................30
C
ALCULATIONS
..........................................30
C
IRCUIT
C
ONTROL
L
OGIC
...........................30
C
IRCUIT
S
TATUS
.........................................32
C
OMPRESSOR
C
ONTROL
.............................32
C
ONDENSER
F
AN
C
ONTROL
........................34
EXV
C
ONTROL
...........................................35
E
CONOMIZER
C
ONTROL
..............................36
L
IQUID
I
NJECTION
......................................36
ALARMS AND EVENTS............................37
S
IGNALING
A
LARMS
...................................37
C
LEARING
A
LARMS
....................................37
D
ESCRIPTION OF
A
LARMS
..........................37
U
NIT
E
VENTS
..............................................39
C
IRCUIT
S
TOP
A
LARMS
..............................40
C
IRCUIT
E
VENTS
........................................44
A
LARM
L
OGGING
.......................................45
USING THE CONTROLLER ....................46
N
AVIGATING
..............................................47
OPTIONAL REMOTE USER INTERFACE
.......................................................................53
START-UP AND SHUTDOWN .................55
T
EMPORARY
S
HUTDOWN
............................55
E
XTENDED
(S
EASONAL
)
S
HUTDOWN
..........56
FIELD WIRING DIAGRAM......................58
SYSTEM MAINTENANCE........................60
P
REVENTATIVE
M
AINTENANCE
S
CHEDULE
63
APPENDIX ...................................................64
D
EFINITIONS
...............................................64
©
2009 McQuay International. Information covers the McQuay International products at the time of publication and we reserve the right to
make changes in design and construction at anytime without notice.
®™
The following are trademarks or registered trademarks of their
respective companies: BACnet from ASHRAE; L
ON
M
ARK and
L
ON
W
ORKS
from Echelon Corporation; McQuay, MicroTech III, Guardister,
and Open Choice from McQuay International.
Unit controllers are L
ON
M
ARK
certified with an optional
L
ON
W
ORKS
communications module
Manufactured in an
ISO Certified facility
Содержание AWS
Страница 8: ...8 KOMAC00607 09EN Figure 5 Piping Schematic with Economizer Circuit One Circuit ...
Страница 12: ...12 KOMAC00607 09EN ...
Страница 54: ...54 KOMAC00607 09EN ...
Страница 67: ......