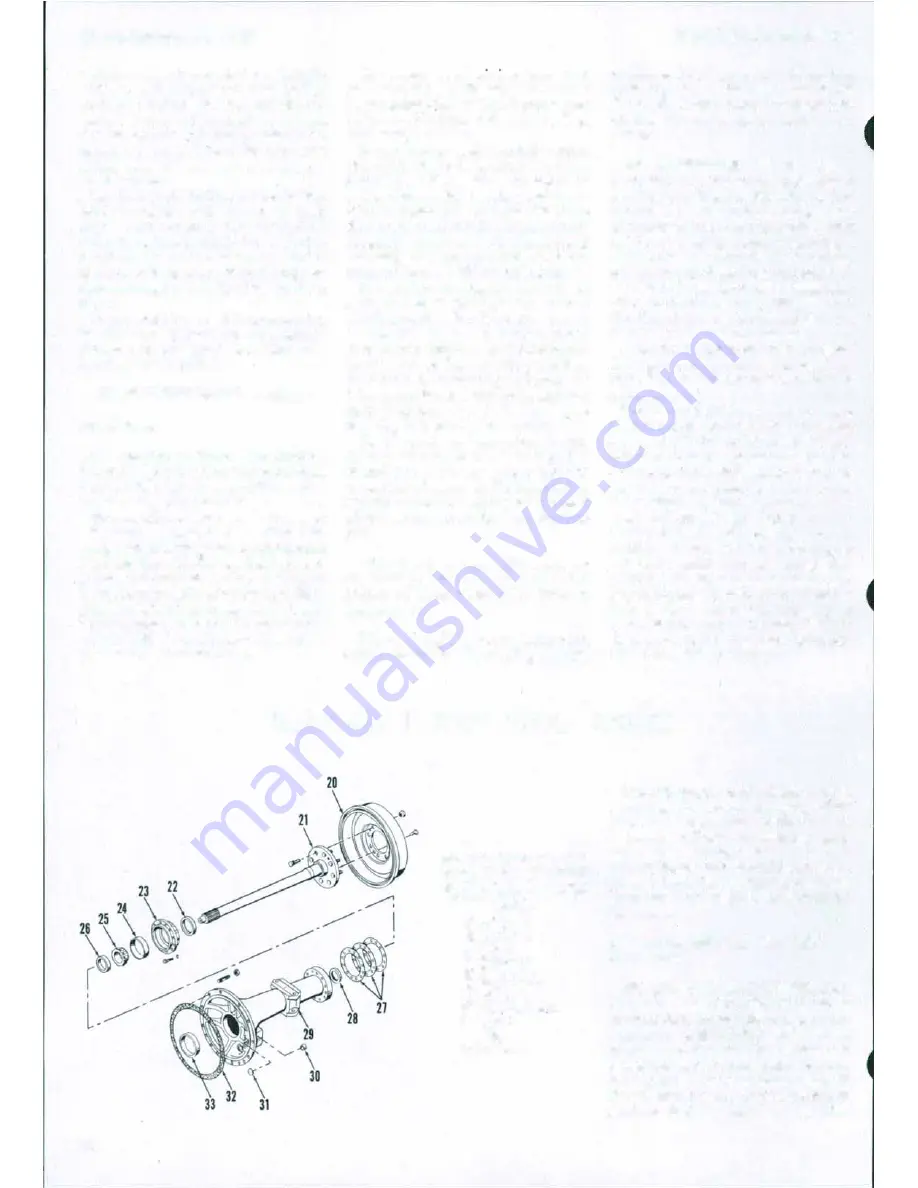
Paragraphs
1 63-1 65
withdraw axle from housing; then lift
out the coupler (7). Shoes (3) will be free
in fork (4) with coupler removed.
'Ib
serv·
ice the actuating mechanism, remove
the clamp bolt (17) and withdraw ac·
tuating shaft (11) from housing and
pedal, then lift out the remaining ac
tuating parts.
'Ib
remove axle half of coupler (2-Fig.
157) on models with planetary final
drive, remove spring pin securing shift
fork (3) to actuating
shaft
(5) and the two
countersunk screws secw·ing carrier
plate to axle housing, then slide plate,
fork and coupler carefully off end of drive
axle.
On all models, assemble by reversing
the disassembly procedure and adjust as
outlined in paragraph 161 after axle
housing is reinstalled.
MAIN DRIVE BEVEL GEARS
All Models
163.
REMOVE AND REINSTALL.
The main drive bevel ring gear {15-Fig.
155) and bevel pinion gear (22) must be
renewed as a matched set.
'Ib
remove bevel ring gear,
first
remove
differential assembly as outlined in
paragraph 158. Ring gear retaining nuts
are installed with thread locking com
pound, and removal
will
be easier using
a slight amount. of heat on the nuts. Ring
gear is a tight fit and may also be bond·
ed to differential case with epoxy, so it
will probably be necessary to press ring
gear from differential case.
'Ib
remove bevel ptmon gear, fu·st
remove hydraulic lift cover as outlined
in paragraph 207 or 216. Remove axle
housings and differential assembly
if
not
previously removed.
On models equipped with independent
pto, Multi-Power transmission or aux.
iliary hydraulics, split the tractor be
tween differential housing and trans·
mission housing. Remove pto side cover,
disconnect hydraulic lines, remove pump
support pins and remove hydraulic pump
assembly and independent pto clutch
unit out front of differential housing.
On models not equipped with indepen
dent pto, Multi-Power transmission or
auxiliary hydraulics, it is not necessary
to split the tractor to remove pinion
shaft. Remove the coupler tube and pin
ion drive shaft. Remove side cover from
left-hand side of housing and move pto
driven gear forward on pto
shaft splines.
Remove ground speed pto drive gear
(30-Fig. 155) from pinion shaft.
On all models, remove cap screws at
taching retainer (25) to housing, then
thread two
of
the cap screws into the
tapped holes in retainer. Tighten the two
cap screws evenly to force retainer with
pinion as an assembly from housing
bore.
NOTE:
Check
and adjust differential car
rier bearing preload, If necessary, before
reinstalling bevel pinion gear. Refer
to
paragraph
159.
When reinstalling be�l pinion gear,
make certain that the locating pin (24)
MASSEY -FERGUSON
is aligned before pressing r·etainer into
place. Tighten retainer cap screws to 108
N
·
m (80 ft.-Ibs.) torque. Complete in
stallation by reversing the removal pro-
cedure.
164.
OVERHAUL.
'Ib
disassemble
bevel pinion gear, proceed as follows: If
bearing adjusting nut (28-Fig. 155) is
retained by a tab washer, unlock tabs
and remove the nut.
If
bearing adjusting
nut is retained by locking pins (29), it
will be necessary to spHt the nut using
a hammer and chisel to remove nut from
the shaft. Be careful to avoid damaging
threads of pinion when splitting the nut.
On
all models, bump the pinion shaft out.
of retainer after nut is removed.
Examine all parts for wear or other
damage and renew as necessary. Bear
ings (23) and retainer (25) are serviced
as
an
assembly.
When reassembling pinion gear,
tighten nut (28) to obtain pinion rolling
torque of 2.25
N
·
m (20 in.-lbs.) to pro
vide correct bearing preload. Secure nut
by bending tabs of lock washer or by driv
ing locking pins down both sides of one
of the pinion splines. Be sure pins are
flush with end of adjusting nut.
When installing the ring gear, make
certain that mating surfaces of ring gear
and differential case are thoroughly
clean and free from nicks or burrs. App·
ly special epoxy to both mating surfaces
and cure for specified time following kit
instructions. Apply Loctite 262 to
threads of retaining nuts and tighten to
108
N
·
m (80 ft.-lbs.) torque.
REAR AXLE AND FINAL DRIVE
66
Fig. 159-ElCploded view of
rear alCie and associated parts
typical of all tractors elCcept
Orchard models and MF250
models.
20. Brake drum
21. Axle
ehafl
22.
Oil
seal
(outerl
23. Re�.elner
24.
Bearing
rup
25.
Bearing
cone
26.
Retaining
collar
27.
ShimJ
28. on seal (inner�
29. Axle
housing
(L
H.l
30.
Bushing
31
Plug
32. Casket
33. Bearing rup
Orchard models and MF250 models
are equipped with a planetary type final
dr
i
ve unit located in outer end of rear ax
le housing. All other models are equip
ped with a straight drive axle that
splines directly into the differential side
gears. Refer to the approp1·iat.e following
paragraphs for removal and overhaul
procedures.
All Models Without Planetary
Final Drive
165.
REMOVE AND REINSTALL.
The axle shafts (21-Fig. 159) can be
removed from tractor without removing
axle housings (29) if desired. Raise and
support rear of tractor, then remove rear
wheel and tire. Remove brake drum re·
taining screws and pull drum from axle
flange. Remove cap screws attaching
retainer (23) to axle housing, then